Introduction
Overview of Sleeve Bearings
Definition and Basic Function: Sleeve bearings, also known as plain bearings or bushings, are a simple type of bearing comprising a cylindrical sleeve made of various materials, such as bronze, plastic, or composite materials. Their primary function is to provide a smooth surface for rotating or sliding shafts, reducing friction and wear within machinery. Unlike roller bearings, sleeve bearings have no moving parts, which allows for simpler design and manufacturing.
Importance in Mechanical Engineering: In the realm of mechanical engineering, sleeve bearings play a crucial role. They are widely used in applications where high load capacity and low maintenance are required. The absence of rolling elements means they can withstand higher loads at lower speeds, making them ideal for heavy machinery, automotive engines, and industrial equipment. Their ability to dampen vibrations and accommodate misalignments further enhances their utility in engineering applications.
This article aims to provide a comprehensive guide on sleeve bearings, exploring their development, utility, and recent innovations. By delving into the historical evolution of sleeve bearings, we will understand how advancements in materials and design have enhanced their performance. The article will also examine the various applications of sleeve bearings across different industries, highlighting their significance in modern engineering. Furthermore, we will explore cutting-edge innovations that are shaping the future of sleeve bearings, ensuring they continue to meet the demands of increasingly complex and high-performance machinery.
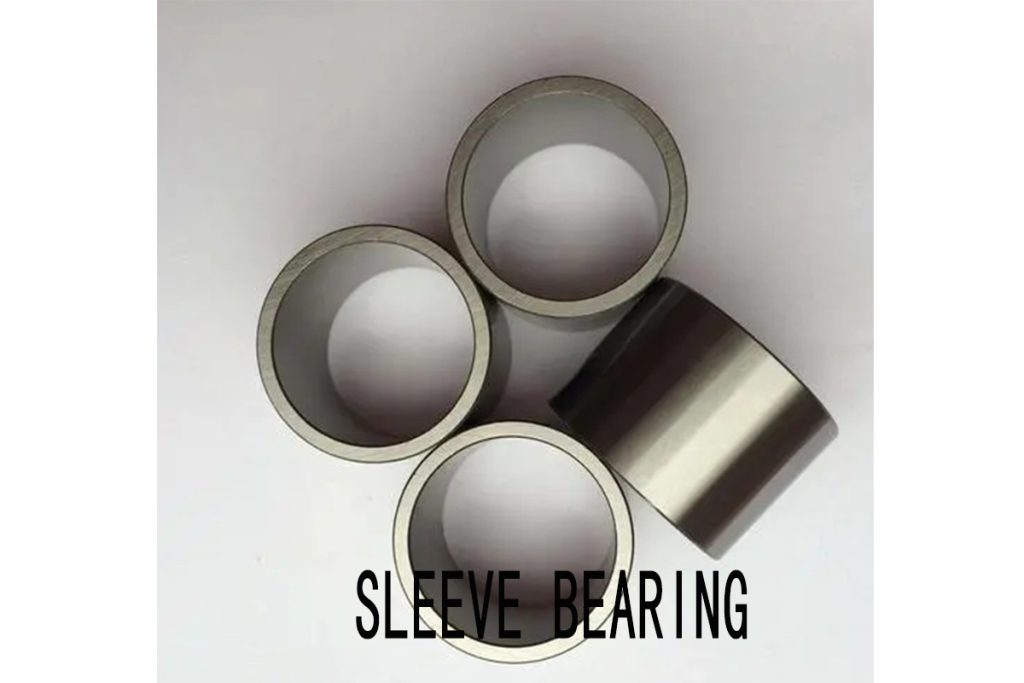
Historical Background
Early Inventions and Uses
Sleeve bearings have a long history dating back to ancient times. Early civilizations, such as the Egyptians and Romans, used simple bearings made from wood or stone to reduce friction in primitive machines like carts and water wheels. These early versions were rudimentary but laid the groundwork for the development of more sophisticated bearing systems. The concept of a bearing, which allows for smoother rotation or movement of objects, was fundamental to the advancement of engineering and machinery.
Evolution of Materials and Design
The evolution of sleeve bearings has been marked by significant advancements in materials and design. Initially, natural materials like wood and stone were replaced by metals such as bronze and brass, which offered better durability and load-bearing capabilities. The introduction of bronze in bearing design was particularly revolutionary, as it provided excellent wear resistance and could be easily lubricated to reduce friction.
In the 20th century, the development of synthetic materials like plastics and composites further revolutionized the sleeve bearing industry. Materials such as PTFE (Teflon) and nylon offered low friction coefficients and good wear resistance, making them suitable for a wide range of applications. Composite materials, which combine the properties of different substances, have enabled engineers to tailor sleeve bearings for specific uses, enhancing their performance and longevity.
Significant Milestones in Development
Several milestones have marked the development of sleeve bearings:
Milestone | Description |
Industrial Revolution | The Industrial Revolution saw a surge in the use of bearings in machinery. The increased demand for efficient and reliable bearings spurred innovations in design and materials. Bronze and brass bearings became standard in many industrial applications due to their superior properties. |
Introduction of Lubrication Techniques | The development of advanced lubrication techniques in the late 19th and early 20th centuries significantly improved the performance of sleeve bearings. Proper lubrication reduces friction, prevents wear, and extends the lifespan of bearings, making it a critical factor in bearing design. |
Advent of Synthetic Materials | Advent of Synthetic Materials |
Modern Engineering Innovations | In recent decades, advancements in engineering and materials science have led to the development of high-performance sleeve bearings. Innovations such as self-lubricating bearings and the use of advanced composites have further enhanced their reliability and efficiency. These modern bearings can operate in extreme conditions, including high temperatures and corrosive environments, making them indispensable in various high-tech industries. |
The historical development of sleeve bearings reflects the ongoing quest for materials and designs that improve performance, durability, and versatility. From ancient wooden bearings to modern composites, the evolution of sleeve bearings demonstrates the ingenuity and adaptability of engineers in meeting the ever-changing demands of technology and industry.
Technological Advances in Sleeve Bearings
Advances in Manufacturing Techniques
Manufacturing techniques for sleeve bearings have evolved significantly over the years, leading to improved precision, efficiency, and cost-effectiveness. Modern manufacturing methods such as CNC machining and additive manufacturing allow for the production of bearings with tighter tolerances and more complex geometries. These advancements ensure that sleeve bearings meet the high standards required in various applications. Additionally, advancements in surface finishing technologies, such as precision grinding and superfinishing, have enhanced the wear resistance and lifespan of sleeve bearings by creating smoother surfaces that reduce friction.
Improvements in Material Science
The field of material science has seen remarkable progress, directly impacting the performance and application range of sleeve bearings. Traditional materials like bronze and brass are now complemented by advanced composites and engineered plastics. For instance, high-performance polymers such as PEEK (polyether ether ketone) and PTFE (polytetrafluoroethylene) offer excellent wear resistance, low friction, and high thermal stability. These materials are particularly useful in applications where traditional metal bearings might fail due to high temperatures or corrosive environments. The development of these new materials has expanded the use of sleeve bearings into areas such as chemical processing, food and beverage industries, and medical equipment.
Evolution of Design Standards
Design standards for sleeve bearings have also evolved to accommodate new materials and manufacturing techniques. Modern design standards emphasize not only the physical dimensions and tolerances but also the performance characteristics under various operating conditions. Standards such as ISO (International Organization for Standardization) and ASTM (American Society for Testing and Materials) provide guidelines for the design, testing, and application of sleeve bearings. These standards ensure that bearings meet specific criteria for load capacity, friction, wear resistance, and thermal stability, which are crucial for their reliable operation in different industries. Furthermore, the integration of computer-aided design (CAD) and finite element analysis (FEA) in the design process has enabled engineers to simulate and optimize the performance of sleeve bearings before production, reducing the risk of failure and improving overall efficiency.
In conclusion, the technological advances in manufacturing techniques, material science, and design standards have significantly enhanced the performance, reliability, and application range of sleeve bearings. These innovations have made it possible for sleeve bearings to meet the demanding requirements of modern industries, ensuring their continued relevance and utility in various mechanical systems.
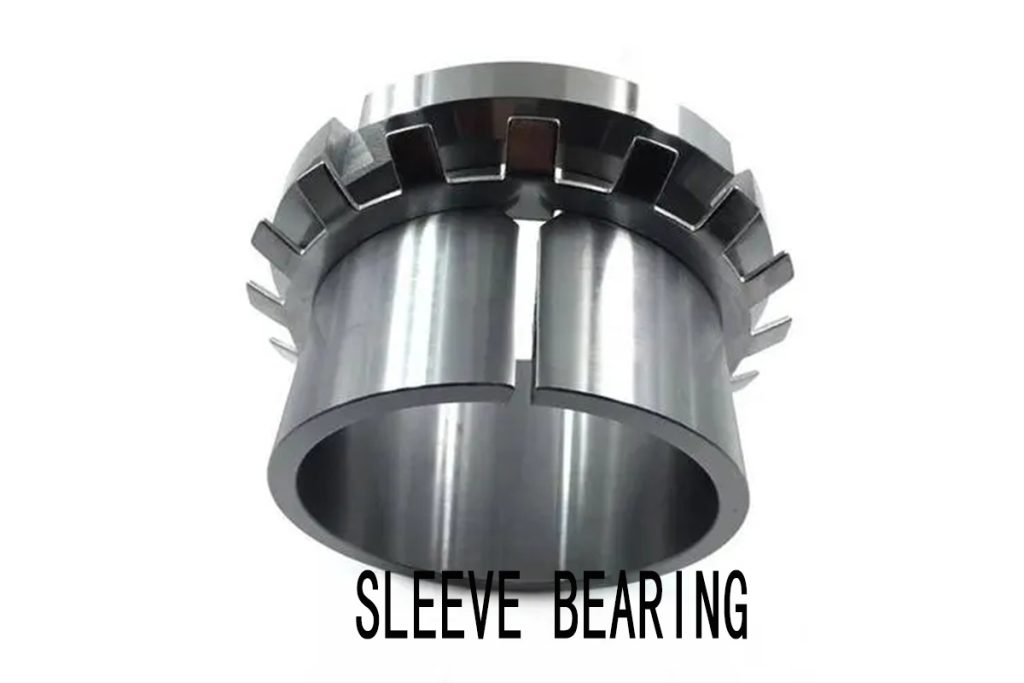
Industrial Applications of Sleeve Bearings
Automotive and Transportation
In the automotive and transportation sectors, sleeve bearings play a crucial role due to their reliability, efficiency, and ability to operate under harsh conditions. These bearings are commonly used in engines, transmissions, and suspension systems where they reduce friction and wear between moving parts. In engines, sleeve bearings support crankshafts and camshafts, ensuring smooth rotation and reducing metal-to-metal contact. The use of advanced materials, such as PTFE and high-strength alloys, allows these bearings to withstand high temperatures and loads, extending the life of automotive components.
In the transportation industry, including railways and marine applications, sleeve bearings are essential for their ability to function in environments with high moisture and varying temperatures. They are often employed in the bearings of locomotive engines, ship propeller shafts, and various rotating components where maintenance access can be challenging. The durability and low maintenance requirements of sleeve bearings make them ideal for these demanding applications.
Heavy Machinery and Manufacturing
Heavy machinery and manufacturing industries rely heavily on sleeve bearings due to their robustness and ability to handle substantial loads. In industrial machinery, such as conveyor systems, pumps, and gearboxes, sleeve bearings ensure smooth operation and reduce the wear on mechanical components. These bearings are chosen for their ability to distribute loads evenly and their capacity to operate without extensive lubrication, which is crucial in environments where contamination is a concern.
Manufacturing processes often involve high-speed operations and heavy-duty equipment. Sleeve bearings used in these applications are designed to withstand the stresses of continuous operation, shock loads, and exposure to various chemicals and particulates. The development of self-lubricating bearings and the use of advanced composites have further enhanced the performance of sleeve bearings in these sectors, reducing downtime and maintenance costs.
Aerospace and Defense
In the aerospace and defense industries, the performance and reliability of sleeve bearings are paramount. These bearings are used in critical applications such as aircraft engines, landing gear, and various control systems where failure is not an option. Sleeve bearings in aerospace applications must withstand extreme temperatures, high speeds, and significant stress. The use of high-performance materials, such as ceramics and advanced composites, ensures that these bearings meet stringent standards for durability and performance.
In defense applications, sleeve bearings are found in military vehicles, missile systems, and naval equipment. These bearings must perform reliably in extreme conditions, including high shock, vibration, and exposure to harsh environments. The advancements in material science and precision manufacturing techniques have made it possible for sleeve bearings to meet the rigorous demands of these applications, providing reliable performance and enhancing the operational readiness of defense systems.
Overall, sleeve bearings are indispensable in a wide range of industrial applications. Their ability to reduce friction, support loads, and operate reliably under various conditions makes them a critical component in automotive, heavy machinery, aerospace, and defense industries. The continuous advancements in materials and manufacturing techniques ensure that sleeve bearings will continue to meet the evolving needs of these sectors, driving innovation and efficiency in mechanical engineering.
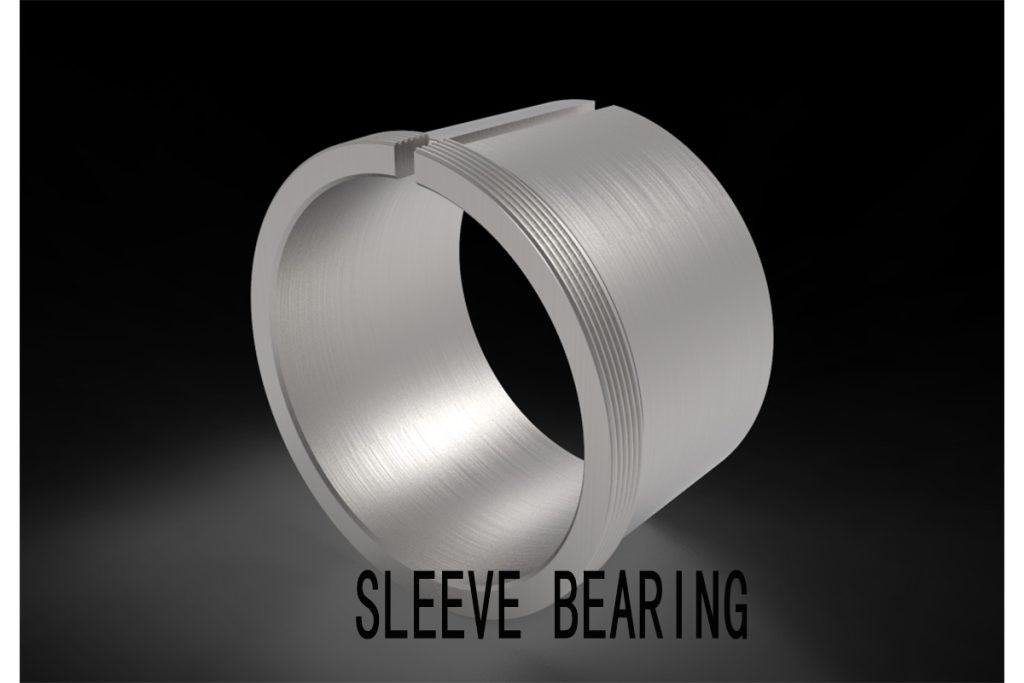
Advanced Materials in Sleeve Bearings
Development of Composite Materials
The development of composite materials has revolutionized the performance and application of sleeve bearings. Composites, which combine two or more distinct materials, offer superior properties compared to traditional materials like bronze or brass. These advanced composites often include polymers reinforced with fibers such as carbon or glass, providing enhanced strength, wear resistance, and reduced friction.
For example, polymer-based composites have become popular in sleeve bearings due to their lightweight, corrosion resistance, and ability to operate without external lubrication. This makes them ideal for applications in harsh environments where traditional metal bearings would corrode or fail. The integration of fibers within the polymer matrix improves the structural integrity and load-bearing capacity, ensuring long-term performance in demanding applications.
Self-lubricating Bearings
Self-lubricating bearings represent a significant advancement in bearing technology, particularly for sleeve bearings. These bearings are designed to operate with minimal or no external lubrication, relying on embedded lubricants within the bearing material itself.
One common self-lubricating material is PTFE (polytetrafluoroethylene), which is often combined with other materials to form a composite. PTFE has excellent low-friction properties and can withstand a wide range of temperatures, making it suitable for both high and low-temperature applications. Self-lubricating sleeve bearings reduce maintenance needs, minimize downtime, and enhance the reliability of machinery by providing consistent lubrication throughout the bearing’s lifespan.
Another innovative approach involves using porous metal bearings impregnated with lubricating oils. These oil-impregnated bearings slowly release lubricant during operation, ensuring continuous lubrication and reducing wear and friction. This technology is particularly beneficial in applications where regular maintenance is challenging or impractical.
High-temperature and Corrosion-resistant Alloys
The use of high-temperature and corrosion-resistant alloys has expanded the application range of sleeve bearings. These advanced alloys are designed to maintain their structural integrity and performance under extreme conditions, such as high temperatures, corrosive environments, and heavy loads.
High-temperature alloys like Inconel, Hastelloy, and ceramics are used in sleeve bearings for applications involving extreme heat, such as in aerospace engines, industrial furnaces, and power generation turbines. These materials can withstand temperatures well above those that traditional bearings can handle, ensuring reliable operation and longevity in harsh conditions.
Corrosion-resistant alloys, including stainless steels and certain bronzes, are crucial for applications involving exposure to harsh chemicals, moisture, and saltwater. These materials prevent degradation and ensure the bearings maintain their performance and lifespan in corrosive environments, such as chemical processing plants, marine applications, and wastewater treatment facilities.
Conclusion
The continuous advancements in material science have significantly enhanced the performance and application scope of sleeve bearings. The development of composite materials, self-lubricating technologies, and high-temperature and corrosion-resistant alloys has enabled sleeve bearings to meet the rigorous demands of modern industries. These innovations ensure that sleeve bearings remain an essential component in various applications, offering reliability, durability, and efficiency. As technology progresses, further advancements in materials and design will continue to drive the evolution of sleeve bearings, cementing their role in the future of engineering and machinery.
Cutting-Edge Innovations in Sleeve Bearings
In recent years, the field of sleeve bearings has seen significant innovations aimed at improving performance and sustainability. These innovations are driven by advancements in materials science, manufacturing techniques, and the integration of smart technologies.
Innovations | Description |
Integration of Smart Sensors | Smart sensors are integrated into sleeve bearings to monitor performance in real-time. They provide critical data on parameters like temperature, vibration, and lubrication. |
IoT and Predictive Maintenance Solutions | Sleeve bearings are connected to IoT networks, enabling predictive maintenance. Data from sensors is analyzed to predict potential failures, reducing downtime. |
Environmentally Sustainable Designs | Researchers are developing eco-friendly materials, coatings, and lubricants for sleeve bearings to minimize environmental impact. Energy-efficient manufacturing is also explored. |
Conclusion
The evolution of sleeve bearings from simple wooden components to advanced, sensor-integrated devices highlights their critical role in modern machinery. The ongoing innovations in materials, smart technology, and sustainable design ensure that sleeve bearings will continue to be a vital component in a wide range of applications. As technology progresses, the potential for further enhancements in sleeve bearing performance and efficiency remains vast, promising even greater contributions to engineering and industry.
Conclusion
Summary of Key Points
Recap of Development and Historical Context
The development of sleeve bearings has been a journey marked by innovation and adaptation to the needs of various industries. From their early use in ancient civilizations, where rudimentary wooden bearings were employed to reduce friction in carts and simple machinery, sleeve bearings have evolved significantly. The advent of the Industrial Revolution was a pivotal moment, introducing metal alloys such as bronze and brass. These materials greatly enhanced the durability and performance of sleeve bearings, making them more suitable for the increasing demands of industrial applications.
As technology progressed through the 20th century, the development of composite materials and advanced lubrication techniques further improved the efficiency and lifespan of sleeve bearings. This period also saw the introduction of more precise manufacturing processes, which allowed for tighter tolerances and improved performance characteristics. Today, sleeve bearings continue to benefit from ongoing research and development, making them indispensable components in many modern applications.
Importance and Versatility in Various Applications
Sleeve bearings are crucial due to their simplicity, reliability, and versatility. They are employed in a wide array of applications, ranging from automotive engines to household appliances. In automotive engines, sleeve bearings reduce friction between moving parts, thereby improving performance and extending the engine’s lifespan. Their ability to operate under high loads and at various speeds makes them ideal for industrial machinery, where reliability and efficiency are paramount.
Moreover, sleeve bearings are particularly well-suited for environments where other types of bearings might fail. They can function effectively in conditions with high levels of dust, dirt, or moisture, making them perfect for agricultural and construction equipment. Their simple design allows for easy installation and maintenance, which reduces downtime and operational costs. The versatility of sleeve bearings is a testament to their importance in both traditional and modern engineering applications.
Future Directions and Innovations
The future of sleeve bearings is being shaped by exciting innovations aimed at enhancing their performance and sustainability. One of the most significant developments is the integration of smart sensors into sleeve bearings. These sensors can provide real-time data on temperature, vibration, and lubrication levels, enabling more precise monitoring and maintenance. This capability is particularly valuable in predictive maintenance strategies, where potential issues can be identified and addressed before they lead to equipment failure.
The rise of the Internet of Things (IoT) has also impacted sleeve bearings. By connecting sleeve bearings to IoT networks, manufacturers can implement sophisticated predictive maintenance solutions. This approach not only improves the reliability of machinery but also extends the lifespan of the bearings themselves.
Environmental sustainability is another key area of innovation. Researchers are exploring the use of eco-friendly materials and lubricants to minimize the environmental impact of sleeve bearings. Biodegradable materials and sustainable manufacturing processes are being developed to reduce pollution and enhance the recyclability of bearings. These efforts align with global trends towards more sustainable industrial practices.
In summary, the evolution of sleeve bearings reflects their critical role in modern engineering. From their historical development to their diverse applications and future innovations, sleeve bearings continue to be a fundamental component in a wide range of industries. As technology advances, the potential for further enhancements in sleeve bearing performance and sustainability remains vast, promising continued relevance and importance in the years to come.