Introduction
Timken bearings are integral components used across various industries, ensuring smooth operations and reliable performance. From automotive to aerospace applications, Timken bearings play a crucial role in supporting rotating shafts while minimizing friction and facilitating motion. Understanding the significance of Timken bearings is essential for optimizing machinery performance and ensuring longevity.
Timken bearings are engineered with precision and durability to withstand harsh operating conditions, making them indispensable in diverse industrial settings. Whether it’s heavy machinery in manufacturing plants or critical components in aircraft engines, Timken bearings contribute to the seamless functioning of countless systems.
Proper maintenance of Timken bearings is paramount to prolonging their lifespan and maximizing their efficiency. Neglecting maintenance can lead to premature wear, reduced performance, and costly downtime. By implementing effective maintenance practices, businesses can safeguard their investments and maintain peak operational efficiency.
In this comprehensive guide, we’ll delve into essential tips for maintaining Timken bearings, covering everything from lubrication techniques to troubleshooting common issues. By following these guidelines, businesses can ensure the longevity and optimal performance of their Timken bearings, ultimately enhancing productivity and profitability.
Understanding Timken Bearings
Timken bearings represent a pinnacle of engineering excellence in the field of industrial bearings. Timken bearings are renowned for their precision, durability, and ability to withstand extreme conditions, making them indispensable across a wide range of industries, including automotive, aerospace, agriculture, and manufacturing.
Overview of Timken Bearings
Timken offers a diverse range of bearings to cater to various applications and requirements. These include:
Tapered Roller Bearings
Tapered roller bearings are designed to handle both radial and axial loads. They feature tapered inner and outer ring raceways, along with tapered rollers, enabling efficient distribution of load stress and enhanced performance in applications such as automotive wheel hubs and gearboxes.
Spherical Roller Bearings
Spherical roller bearings accommodate high radial loads and moderate axial loads in both directions. They are equipped with spherical rolling elements, which allow for misalignment compensation, making them ideal for applications subjected to shaft deflections or misalignments.
Cylindrical Roller Bearings
Cylindrical roller bearings utilize cylindrical rolling elements to support high radial loads. They are characterized by their high radial rigidity and suitability for applications such as electric motors, machine tools, and conveyor systems.
Ball Bearings
Ball bearings are versatile bearings that can accommodate radial and axial loads in both directions. They feature smooth, low-friction operation, making them suitable for high-speed applications such as automotive transmissions, pumps, and fans.
Key Features and Components
Timken bearings are distinguished by several key features and components that contribute to their exceptional performance and reliability:
High-Quality Materials
Timken bearings are manufactured from premium-quality materials, including high-grade steel and advanced alloys, ensuring superior strength, durability, and resistance to wear and fatigue.
Precision Engineering
Each Timken bearing undergoes rigorous precision engineering and manufacturing processes to ensure consistent dimensional accuracy, smooth operation, and optimal performance under varying operating conditions.
Sealing and Lubrication
Timken bearings are equipped with advanced sealing and lubrication systems to protect against contamination, reduce friction, and extend bearing life. These features help maintain peak performance and reliability in demanding environments.
Innovative Designs
Timken continuously innovates its bearing designs to enhance performance, efficiency, and service life. From advanced cage designs to optimized internal geometries, Timken bearings are engineered to deliver superior performance and reliability in diverse applications.
Understanding the diverse range of Timken bearings and their key features is essential for selecting the right bearing for specific applications and ensuring optimal performance and longevity. we will explore essential maintenance practices to prolong the lifespan of Timken bearings and maximize their efficiency.
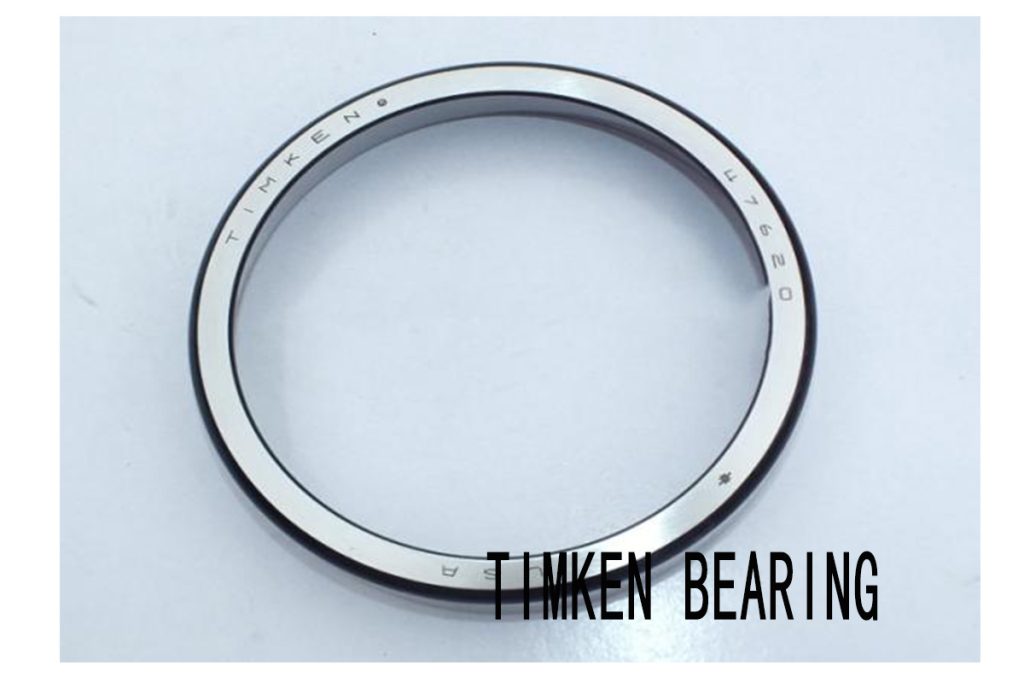
Essential Maintenance Practices
Proper maintenance is paramount to ensure the longevity and optimal performance of Timken bearings. Implementing effective maintenance practices not only extends the lifespan of the bearings but also minimizes the risk of unexpected failures and costly downtime. Let’s delve into some essential maintenance practices to keep your Timken bearings in top condition.
Regular Lubrication | Regular lubrication is crucial for maintaining the smooth operation and longevity of Timken bearings. Lubrication reduces friction between moving parts, minimizes wear, and dissipates heat generated during operation. Choosing the right lubricant and following the manufacturer’s recommendations are essential steps in ensuring optimal performance. |
Impact on Timken Bearing Lifespan | Proper lubrication significantly extends the lifespan of Timken bearings by reducing friction-induced wear and preventing premature failure. Insufficient or improper lubrication can lead to increased friction, overheating, and accelerated wear, ultimately shortening the bearing’s lifespan. |
Inspection Techniques | Routine inspection is essential for detecting signs of wear, damage, or early failure in Timken bearings. Inspection techniques such as visual inspection, vibration analysis, and temperature monitoring help identify potential issues before they escalate into major problems. |
Detecting Wear and Damage | Visual inspection allows maintenance personnel to visually inspect Timken bearings for signs of wear, such as pitting, scoring, or discoloration, indicating inadequate lubrication or contamination. Vibration analysis and temperature monitoring can detect abnormal vibrations or temperature fluctuations, indicating potential bearing defects or misalignment. |
Proper Handling and Storage Procedures | Proper handling and storage procedures are critical to prevent damage to Timken bearings during transportation, storage, and installation. Mishandling or improper storage can lead to contamination, surface damage, or deformation, compromising the bearing’s performance and longevity. |
Handling Guidelines | When handling Timken bearings, it’s essential to avoid dropping or impacting the bearings, as this can cause internal damage or deformation. Using appropriate handling equipment, such as lifting slings or bearing pullers, minimizes the risk of damage during handling and installation. |
Storage Recommendations | Timken bearings should be stored in a clean, dry environment to prevent contamination and corrosion. Storing bearings in their original packaging or protective covers helps shield them from dust, moisture, and other contaminants. Additionally, bearings should be stored in a horizontal position to prevent distortion or misalignment of internal components. |
By adhering to these essential maintenance practices, industries can maximize the longevity and performance of Timken bearings, minimizing downtime and optimizing operational efficiency. we will explore advanced maintenance techniques and troubleshooting strategies to further enhance Timken bearing reliability and longevity.
Maintenance Procedures
Maintaining Timken bearings is crucial to ensure their longevity and optimal performance throughout their service life.we will outline step-by-step procedures for cleaning and re-greasing Timken bearings, as well as guidelines for adjusting clearance and preload to maximize their efficiency.
Cleaning and Re-greasing Timken Bearings Preparation
Before starting the cleaning process, gather the necessary tools and materials, including solvent, cleaning brushes, lint-free cloths, and appropriate lubricant.
Removal
Carefully remove the Timken bearings from their housing or equipment using suitable tools, taking care not to damage the bearing surfaces.
Cleaning
Using a suitable solvent, such as mineral spirits or a degreaser recommended by Timken, thoroughly clean the bearing surfaces to remove old grease, dirt, and contaminants. Use cleaning brushes and lint-free cloths to ensure all surfaces are clean and free from debris.
Step 4: Inspection
Inspect the cleaned bearings for signs of wear, damage, or corrosion. Pay attention to bearing races, rollers, and cages, checking for any abnormalities that may affect performance.
Re-greasing
Apply a sufficient amount of high-quality grease recommended by Timken to the bearing surfaces, ensuring even coverage and adequate lubrication. Avoid over-greasing, as it can lead to overheating and premature bearing failure.
Reassembly
Carefully reassemble the cleaned and re-greased Timken bearings into their housing or equipment, following the manufacturer’s specifications and guidelines. Ensure proper alignment and seating of the bearings to prevent misalignment or binding.
Adjusting Clearance and Preload
Measurement
Using precision instruments such as feeler gauges or dial indicators, measure the clearance or preload of the Timken bearings according to the manufacturer’s specifications.
Adjustment
If the clearance or preload does not meet the specified requirements, adjust the bearing components accordingly. This may involve tightening or loosening bearing nuts, adjusting shims, or using specialized tools for precise adjustment.
Verification
After adjusting the clearance or preload, re-measure the bearing components to verify that they meet the specified requirements. Ensure that the bearings rotate smoothly without excessive play or binding.
Final Inspection
Perform a final visual inspection of the adjusted Timken bearings to ensure they are correctly installed and aligned. Check for any signs of abnormal wear or damage that may indicate improper adjustment.
By following these maintenance procedures for cleaning, re-greasing, and adjusting Timken bearings, industries can prolong their lifespan and optimize their performance. Regular maintenance and adherence to manufacturer’s guidelines are essential to ensure the reliability and longevity of Timken bearings in various applications.
Feature | Timken Bearings | FAG Bearings |
Brand Reputation | Timken is a renowned American brand known for its high-quality bearings and long history of reliability and innovation. | FAG, part of the Schaeffler Group, is a respected German brand recognized for precision engineering. |
Manufacturing Origin | Timken bearings are manufactured primarily in the United States, with some production facilities located worldwide. | FAG bearings are primarily produced in Germany, with additional manufacturing plants in other countries. |
Product Range | Timken offers a diverse range of bearings, including tapered roller bearings, spherical roller bearings, and cylindrical bearings. | FAG provides a wide range of bearings, including ball bearings, roller bearings, and plain bearings. |
Technology | Timken bearings often incorporate advanced technologies such as alloy steel compositions and innovative sealing solutions. | FAG is known for its cutting-edge bearing technologies, including advanced materials and lubrication systems. |
Application Focus | Timken bearings are widely used in various industries, including automotive, aerospace, and industrial equipment. | FAG bearings are commonly found in automotive applications, heavy machinery, and industrial machinery. |
Troubleshooting Common Issues
In the realm of Timken bearings, encountering common problems such as overheating and contamination is not uncommon. Understanding these issues and implementing effective strategies to address them are essential for ensuring the longevity and optimal performance of Timken bearings. Let’s delve into the identification of common problems and explore strategies for troubleshooting and prevention.
Overheating
Overheating is a common issue that can affect Timken bearings and is often indicative of underlying problems such as inadequate lubrication, excessive loads, or improper installation.
Identification
Elevated Temperature: Monitoring the temperature of Timken bearings during operation using infrared thermometers or temperature sensors can help identify overheating.
Abnormal Noise: Overheating may be accompanied by unusual noise, such as grinding or squealing, indicating friction-induced heat generation.
Strategies for Addressing Overheating
Proper Lubrication: Ensure Timken bearings are adequately lubricated with the correct type and amount of lubricant to reduce friction and dissipate heat effectively.
Optimized Clearance: Adjust clearance and preload settings according to manufacturer’s specifications to minimize friction and prevent overheating.
Monitoring and Maintenance: Implement routine monitoring and maintenance procedures to detect overheating early and address underlying issues promptly.
Contamination
Contamination of Timken bearings can lead to accelerated wear, premature failure, and reduced performance. Common contaminants include dirt, dust, moisture, and metal particles.
Identification
Visual Inspection: Regular visual inspection of Timken bearings for signs of contamination, such as discoloration, debris buildup, or rust, can help identify potential issues.
Irregular Operation: Contaminated bearings may exhibit irregular operation, including increased noise, vibration, or reduced rotational smoothness.
Strategies for Addressing Contamination
Proper Sealing: Ensure Timken bearings are adequately sealed to prevent ingress of contaminants. Use appropriate seals and shields to protect bearing surfaces from external elements.
Regular Cleaning: Implement routine cleaning procedures to remove contaminants from Timken bearings and housing components. Use suitable cleaning agents and methods recommended by Timken.
Environment Control: Minimize exposure of Timken bearings to environments prone to contamination, such as dusty or humid conditions. Implement measures to control environmental factors and maintain cleanliness in the operating environment.
By proactively identifying common problems such as overheating and contamination in Timken bearings and implementing effective strategies for troubleshooting and prevention, industries can ensure the reliability, longevity, and optimal performance of their equipment. Regular maintenance, adherence to manufacturer’s guidelines, and ongoing monitoring are key to mitigating potential issues and maximizing the efficiency of Timken bearings in various applications.
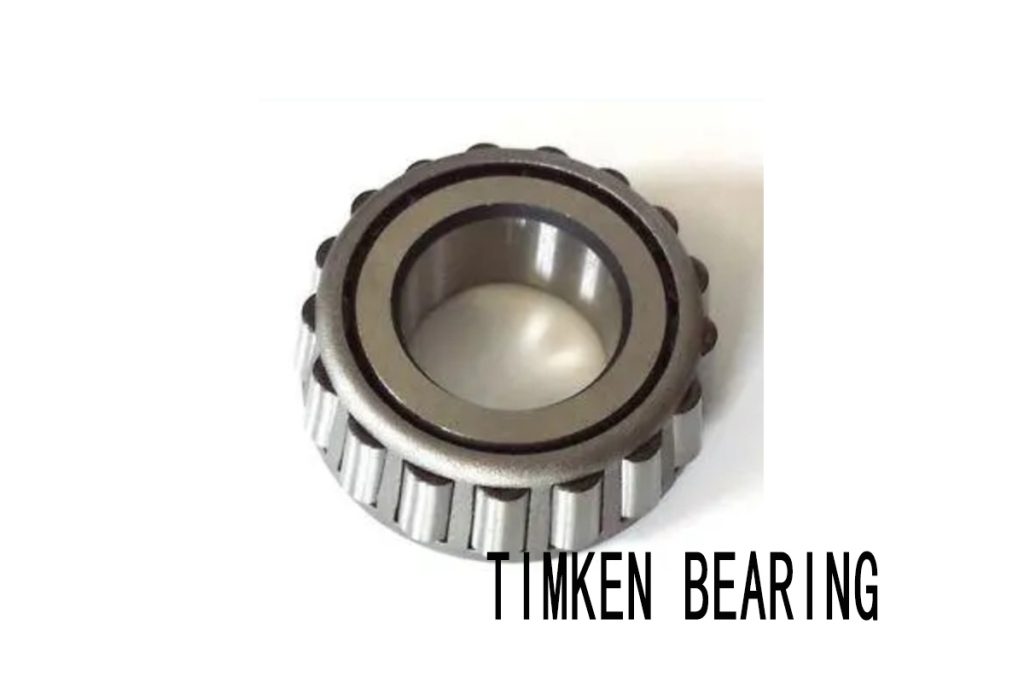
Advanced Maintenance Techniques
Implementing advanced maintenance techniques is essential for maximizing the longevity and optimizing the performance of Timken bearings. we will explore predictive maintenance strategies and advanced techniques aimed at extending the lifespan of Timken bearings and ensuring their optimal functionality.
Implementation of Predictive Maintenance Strategies
Predictive Monitoring
Predictive monitoring involves the use of advanced monitoring techniques, such as vibration analysis, thermal imaging, and oil analysis, to assess the condition of Timken bearings and predict potential failures before they occur.
Maintenance Technique | Description |
Vibration Analysis | Monitoring vibration levels to detect abnormalities in bearing operation, such as imbalance, misalignment, or defects. |
Thermal Imaging | Using thermal imaging to detect temperature variations in Timken bearings, indicating issues like friction or lubrication breakdown. |
Oil Analysis | Analyzing lubricating oil condition to detect contaminants, wear particles, or degradation products signaling potential failure. |
Condition-Based Maintenance
Condition-based maintenance involves scheduling maintenance activities based on the actual condition of Timken bearings rather than predetermined intervals, optimizing maintenance efforts and minimizing downtime.
Condition Monitoring Systems: Implementing automated condition monitoring systems that continuously monitor the health of Timken bearings and trigger maintenance alerts based on predefined thresholds ensures timely intervention and proactive maintenance.
Remote Monitoring: Leveraging remote monitoring technologies allows for real-time monitoring of Timken bearings’ condition from a centralized location, enabling timely diagnosis and intervention, even for remote or inaccessible equipment.
Advanced Techniques for Extending Lifespan
Lubrication Optimization
Optimizing lubrication practices is crucial for extending the lifespan of Timken bearings and maximizing their performance.
Automated Lubrication Systems: Implementing automated lubrication systems ensures consistent and precise lubrication of Timken bearings, minimizing the risk of under or over-lubrication and extending bearing lifespan.
Lubricant Analysis: Performing regular analysis of lubricating oil or grease can help optimize lubrication practices, ensuring the use of the right lubricant type and quantity to maintain bearing health and performance.
Bearing Protection
Protecting Timken bearings from external contaminants and environmental factors is essential for prolonging their lifespan.
Sealing Solutions: Utilizing advanced sealing solutions, such as labyrinth seals or magnetic seals, helps prevent ingress of contaminants and moisture into Timken bearings, enhancing their durability and reliability.
Environmental Controls: Implementing environmental controls, such as dust suppression systems or temperature regulation, helps maintain clean and stable operating conditions for Timken bearings, minimizing wear and extending lifespan.
By implementing predictive maintenance strategies and advanced techniques for extending the lifespan of Timken bearings, industries can optimize their operations, minimize downtime, and ensure the long-term reliability and performance of critical equipment. Investing in advanced maintenance technologies and practices demonstrates a commitment to excellence and ensures the continued success of industrial operations relying on Timken bearings.
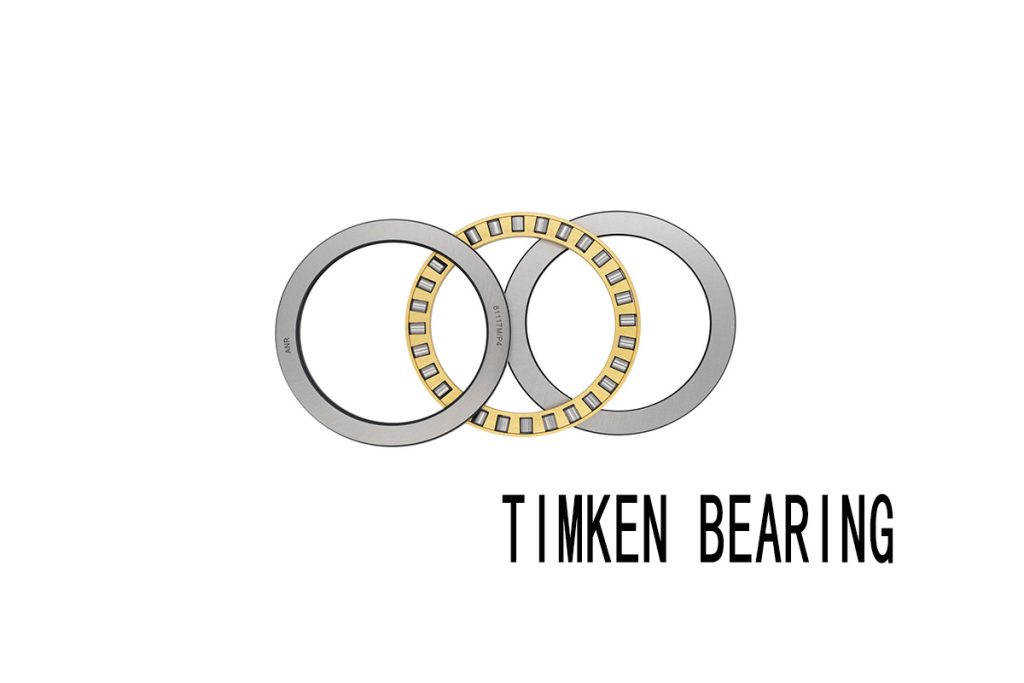
Conclusion
In conclusion, the maintenance of Timken bearings is paramount for ensuring their longevity and optimal performance in various industrial applications. Throughout this guide, we have explored essential tips and advanced techniques aimed at prolonging the lifespan of Timken bearings and maximizing their efficiency.
Recap of Essential Tips
Regular Lubrication: Proper lubrication is essential for minimizing friction, reducing wear, and dissipating heat, thus extending the lifespan of Timken bearings.
Inspection Techniques: Routine inspection allows for the early detection of wear, damage, or abnormalities, enabling timely intervention and preventive maintenance.
Proper Handling and Storage: Adequate handling and storage procedures are critical for preventing damage to Timken bearings and preserving their integrity during transportation, storage, and installation.
Final Thoughts
Maintaining Timken bearings for longevity requires a proactive approach to maintenance, encompassing regular inspection, lubrication, and adherence to manufacturer’s guidelines. By implementing predictive maintenance strategies and advanced techniques, industries can optimize the performance and reliability of Timken bearings, minimizing downtime and maximizing productivity.
In essence, investing in the maintenance of Timken bearings is not just about preserving equipment; it’s about safeguarding operational efficiency, ensuring safety, and driving long-term success in industrial operations. By prioritizing maintenance and adopting a proactive mindset, industries can reap the benefits of prolonged bearing lifespan, reduced downtime, and enhanced profitability.
As you embark on your journey of maintaining Timken bearings, remember that every action taken to preserve their integrity contributes to the overall success and longevity of your equipment and operations. With a commitment to excellence in maintenance practices, you can trust in the reliability and performance of Timken bearings for years to come.
FAQs: Common Questions About Timken Bearing
we address some common questions related to Timken bearings, providing clarity and insights into various aspects of their maintenance and performance.
What are Timken bearings?
Timken bearings are precision-engineered components used in a wide range of industrial applications to facilitate rotational motion and reduce friction between moving parts. They consist of inner and outer rings, rolling elements (such as balls or rollers), cages, and often seals or shields to protect against contamination.
How do Timken bearings differ from other types of bearings?
Timken bearings are known for their exceptional quality, precision engineering, and durability. Unlike standard bearings, Timken bearings undergo stringent manufacturing processes and quality control measures to ensure consistent performance and reliability in demanding operating conditions. They are designed to withstand high loads, speeds, and temperatures, making them ideal for critical applications across various industries.
Why is proper maintenance important for Timken bearings?
Proper maintenance is essential for ensuring the longevity and optimal performance of Timken bearings. Regular maintenance practices, such as lubrication, inspection, and proper handling, help prevent premature wear, reduce the risk of unexpected failures, and extend the lifespan of Timken bearings. Neglecting maintenance can lead to increased downtime, costly repairs, and compromised equipment performance.
How often should Timken bearings be lubricated?
The frequency of lubrication depends on factors such as operating conditions, load, speed, and environment. In general, Timken recommends regular lubrication intervals based on their specific product recommendations and guidelines. It’s essential to use the correct type and amount of lubricant and follow proper lubrication procedures to ensure effective lubrication and prevent over-lubrication or under-lubrication.
What are some common signs of bearing failure?
Common signs of bearing failure include abnormal noise, vibration, increased operating temperature, and visible signs of wear or damage. Timely detection of these symptoms through routine inspection and monitoring allows for proactive maintenance and preventive measures to address underlying issues before they escalate into major problems.
How can I extend the lifespan of Timken bearings?
Several factors contribute to extending the lifespan of Timken bearings, including proper lubrication, regular maintenance, correct installation, and adherence to manufacturer’s recommendations. Implementing advanced maintenance techniques, such as predictive monitoring and condition-based maintenance, can also help optimize bearing lifespan and performance.
Where can I find more information about Timken bearings and maintenance practices?
For comprehensive information about Timken bearings and maintenance practices, including technical specifications, installation instructions, and troubleshooting guidelines, refer to Timken’s official documentation, website resources, or consult with authorized distributors and technical support personnel.
By addressing these common questions, we aim to provide valuable insights into Timken bearings and empower users with the knowledge and understanding needed to maintain and optimize the performance of these critical components. For further assistance or inquiries, feel free to reach out to Timken’s dedicated support channels.
Timken Company.(2018). Timken Bearing Installation and Maintenance. Timken Company. Retrieved from