In the world of machinery and mechanical systems, precision engineering stands as a beacon of excellence. One crucial component that exemplifies this precision is the single row tapered roller bearing. These bearings are not just vital; they are the unsung heroes that ensure the smooth functioning of countless machines across various industries. In this introduction, we will embark on a journey to unveil the importance of single row tapered roller bearings, the role of precision engineering in their design and manufacturing, and how these bearings significantly impact machinery performance and reliability.
Importance of Single Row Tapered Roller Bearings:
Single row tapered roller bearings are an essential part of modern machinery, serving as the interface between rotating components. Their primary function is to handle both radial and axial loads efficiently, making them indispensable in various industries. These bearings are designed for precision and reliability, ensuring that machinery operates smoothly even under challenging conditions.
Precision Engineering and its Role:
At the heart of every single row tapered roller bearing is precision engineering. The design and manufacturing processes involved in creating these bearings are a testament to the meticulous attention to detail required. Precision engineering ensures that every component, from the tapered rollers to the inner and outer rings, is crafted to perfection. The raceways are meticulously designed to enable smooth rolling contact, reducing friction and heat generation. This precision is what sets these bearings apart and makes them capable of handling the demands of modern machinery.
Impact on Machinery Performance and Reliability:
The performance and reliability of machinery are often determined by the quality of the components within. Single row tapered roller bearings play a pivotal role in this regard. Their ability to efficiently distribute loads, reduce friction, and handle high stresses results in machinery that operates at its best. When these bearings are of high quality and properly maintained, they can extend the service life of machinery, minimize downtime, and reduce maintenance costs.
As we delve deeper into the world of single row tapered roller bearings, we will uncover the intricate design principles, structural features, and real-world applications that make them an epitome of precision engineering. By understanding their significance, we can appreciate the vital role these bearings play in ensuring the smooth and reliable operation of machinery across various industries.
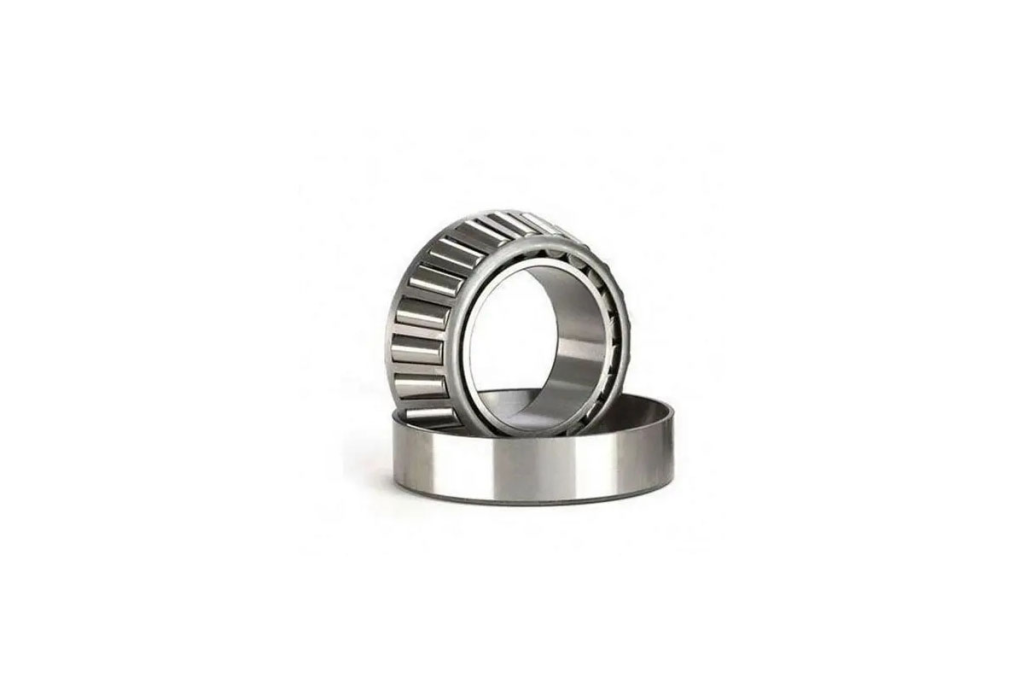
Design and Structure
Single row tapered roller bearings are a fundamental component in various mechanical systems, offering exceptional load-bearing capabilities and unmatched durability. we will delve into the intricate design principles and structural features that make these bearings a cornerstone of precision engineering.
Design Principles:
The design of single row tapered roller bearings is a result of meticulous engineering to achieve optimal performance. These bearings are meticulously crafted to handle radial and axial loads efficiently. The primary design principles include:
– Tapered Rollers: Single row tapered roller bearings feature tapered rollers that are inclined to the bearing axis. This design allows for an efficient distribution of radial and axial loads, providing excellent thrust and radial load-carrying capacity.
– Inner and Outer Rings: These bearings consist of inner and outer rings, each with raceways. The design of these raceways ensures smooth rolling contact between the rollers and the rings, reducing friction and heat generation.
– Cage and Lubrication: A cage or separator maintains proper spacing between the rollers, preventing friction and wear due to contact. Adequate lubrication is essential to minimize friction and reduce wear over time.
Structural Characteristics:
Single row tapered roller bearings exhibit distinct structural characteristics that set them apart from other bearing types. These characteristics include:
– Conical Shape: The rollers have a conical shape, with different cone angles on the inner and outer rings. This design contributes to the axial and radial load-bearing capabilities.
– Cup and Cone Configuration: The bearings typically consist of a cup (outer ring) and a cone (inner ring) assembly. The cup and cone configuration provides precision in bearing alignment and load distribution.
– Versatility: Single row tapered roller bearings come in various designs, including different angles and sizes. This versatility allows engineers to choose the most suitable bearing for a particular application, ensuring optimal performance.
Real-World Applications:
The design and structural features of single row tapered roller bearings make them indispensable in various industries and applications. These bearings are commonly found in:
Automotive | They are widely used in wheel hubs, transmissions, and differentials, where they endure high radial and axial loads. |
Aerospace | In aircraft, single row tapered roller bearings support critical components like landing gear, thrust reversers, and engine accessories. |
Industrial Machinery | From mining equipment to construction machinery, these bearings play a vital role in ensuring smooth operation and reliability. |
In conclusion, understanding the intricate design and structural characteristics of single row tapered roller bearings is essential to appreciate their role in precision engineering. These bearings are the epitome of reliability and load-carrying capability, making them a cornerstone in various industries and applications.
Applications and Industries
Single row tapered roller bearings, with their precision engineering and exceptional load-bearing capabilities, find applications in a diverse range of industries. we will explore the wide array of sectors that rely on these bearings and provide specific examples of how they are utilized. Additionally, we’ll delve into the performance advantages these bearings offer in these various applications.
Automotive Industry:
The automotive industry is one of the largest consumers of single row tapered roller bearings. These bearings are commonly found in wheel hubs, axles, transmissions, and differential assemblies. Their ability to handle both radial and axial loads makes them ideal for supporting the heavy loads and rotational forces encountered in vehicles. Whether in passenger cars, trucks, or commercial vehicles, single row tapered roller bearings contribute to the smooth operation and reliability of automotive systems.
Aerospace Sector:
In the aerospace industry, precision and reliability are paramount. Single row tapered roller bearings are employed in aircraft landing gear systems, where they ensure the safe landing and takeoff of airplanes. These bearings provide the necessary support for the landing gear’s movement, allowing for smooth and controlled deployment. Their durability and ability to withstand high loads make them crucial for aviation safety.
Industrial Machinery:
Across various industrial machinery applications, single row tapered roller bearings play a crucial role. From heavy-duty conveyor systems to large-scale manufacturing equipment, these bearings enable efficient operation. Their ability to handle both radial and thrust loads is invaluable in equipment where axial forces are a concern. Industries such as mining, construction, and manufacturing rely on these bearings for their durability and performance under demanding conditions.
Railway and Transportation:
Railway systems depend on single row tapered roller bearings for their wheels and axles. These bearings contribute to the smooth and reliable movement of trains, ensuring passenger safety and comfort. Additionally, they are used in other forms of transportation, including trams and light rail systems, where they help distribute loads and reduce friction.
Agricultural Machinery:
In the agricultural sector, where heavy equipment is subjected to challenging environments, single row tapered roller bearings find their place. They are used in various agricultural machinery, including tractors, combines, and harvesting equipment. Their robust design and load-carrying capacity make them suitable for the rigors of farming operations.
Performance Advantages:
The performance advantages of single row tapered roller bearings are evident across these diverse applications. Their ability to handle both radial and axial loads reduces the need for multiple bearings in a single assembly, simplifying designs and reducing costs. Moreover, their precision engineering ensures minimal friction, leading to increased efficiency and reduced heat generation. This, in turn, contributes to extended bearing life and reduced maintenance requirements, further enhancing their appeal to industries worldwide.
In conclusion, single row tapered roller bearings are indispensable in a multitude of applications and industries, from automotive and aerospace to industrial machinery and transportation. Their precision engineering and exceptional load-handling capabilities make them the cornerstone of many mechanical systems, ensuring efficiency, reliability, and safety. As we continue to unveil the world of single row tapered roller bearings, we will explore more aspects of their design, manufacturing, and benefits in the subsequent sections of this comprehensive guide.
Manufacturing and Quality Control
we will delve into the intricate world of manufacturing single row tapered roller bearings and the stringent quality control measures employed to guarantee their precision and reliability. Additionally, we will explore how advancements in manufacturing technology have contributed to the enhanced quality of these essential components.
Precision Manufacturing Processes:
The production of single row tapered roller bearings begins with the selection of high-quality raw materials, typically bearing-grade steel. The manufacturing process involves several precise steps to create the final product:
Turning and Grinding: The initial shaping of the bearing components involves turning and grinding operations, where the outer and inner rings are formed to exact dimensions. Precision is paramount, as any deviation can impact the bearing’s performance.
Heat Treatment: After shaping, the components undergo heat treatment processes to enhance their hardness and durability. This step involves quenching and tempering to achieve the desired material properties.
Assembly: The inner and outer rings, along with tapered rollers and a cage, are meticulously assembled. The design and arrangement of these components determine the bearing’s load-carrying capacity and ability to withstand axial and radial forces.
Grinding of Tapered Rollers: The tapered rollers are ground to precision dimensions, ensuring uniform load distribution and reduced friction during operation.
Surface Finishing: The bearing’s surface finish is critical for minimizing friction and wear. Precision surface grinding and superfinishing processes are employed to achieve an exceptionally smooth surface.
Quality Control Measures:
Quality control is integral to the manufacturing of single row tapered roller bearings. Rigorous inspection and testing processes are in place to maintain the highest standards of accuracy and reliability. Key quality control measures include:
Dimensional Accuracy: Precise measurements are taken at every stage of production to ensure that components meet specified tolerances. Any deviations are immediately addressed to maintain consistency.
Material Analysis: Thorough material analysis is conducted to verify the composition and quality of the bearing-grade steel. This analysis helps identify any potential defects or impurities that could compromise the bearing’s performance.
Non-Destructive Testing: Advanced non-destructive testing methods, such as ultrasonic testing and magnetic particle inspection, are employed to detect internal flaws or defects that may not be visible to the naked eye.
Functional Testing: Bearings undergo functional testing to evaluate their load-carrying capacity, rotational accuracy, and resistance to axial and radial forces. This ensures that the final product meets or exceeds industry standards.
Advancements in Manufacturing Technology:
Advancements in manufacturing technology have revolutionized the production of single row tapered roller bearings. Computer-aided design (CAD) and computer numerical control (CNC) machining have enhanced precision and consistency in manufacturing processes. These technologies enable engineers to design bearings with optimal geometries, resulting in improved load distribution and reduced friction.
Additionally, the use of advanced materials, such as ceramic rolling elements and innovative cage designs, has further increased the performance and longevity of single row tapered roller bearings.
In conclusion, the manufacturing of single row tapered roller bearings is a testament to precision engineering and quality control. These bearings are the result of meticulous craftsmanship and cutting-edge technology, ensuring that they meet the rigorous demands of various industries. As we continue our exploration of single row tapered roller bearings, we will uncover more aspects of their applications, advantages, and maintenance in the subsequent sections of this comprehensive guide.
Maintenance and Longevity
we will explore the critical aspects of maintaining single row tapered roller bearings to ensure their longevity and optimal performance. We’ll delve into best practices for upkeep, strategies for monitoring wear and tear, and cost-effective solutions for replacement and repairs when necessary.
Best Practices for Maintenance:
Maintaining single row tapered roller bearings is essential for their extended service life. Here are some best practices to keep in mind:
Regular Lubrication: Adequate lubrication is paramount to reduce friction and wear. Follow manufacturer recommendations for lubrication intervals and use the appropriate lubricant.
Monitoring Temperature: Pay attention to the operating temperature of the bearings. Abnormal temperature increases can indicate issues like inadequate lubrication or misalignment.
Alignment Checks: Periodically check for proper alignment of the bearing components. Misalignment can lead to premature wear and reduced bearing life.
Seal Inspection: Examine the seals for damage or leaks. Damaged seals can allow contaminants to enter the bearing, leading to accelerated wear.
Vibration Analysis: Employ vibration analysis techniques to detect abnormal vibrations that may signal bearing problems. Early detection can prevent further damage.
Strategies for Monitoring Wear and Tear:
To ensure the longevity of single row tapered roller bearings, it’s crucial to monitor their condition regularly:
Visual Inspections: Visually inspect the bearings for signs of wear, corrosion, or damage. Look for indications such as pitting, rust, or discoloration.
Condition Monitoring: Implement condition monitoring techniques, such as vibration analysis, thermography, and oil analysis, to identify potential issues before they become critical.
Measurement of Clearances: Measure internal clearances within the bearing assembly to ensure they remain within acceptable limits.
Periodic Disassembly: In some cases, it may be necessary to disassemble the bearing for a thorough inspection. This should be performed by qualified technicians.
Cost-Effective Solutions for Replacement and Repairs:
When single row tapered roller bearings reach the end of their service life or experience significant damage, it’s essential to consider cost-effective solutions:
Timely Replacement | When bearings have reached their expected lifespan or show severe signs of wear, timely replacement is the most reliable solution to prevent machinery downtime and potential damage to other components. |
Reconditioning | In some cases, reconditioning or refurbishing the bearing may be a cost-effective alternative to replacement. This process involves cleaning, regrinding, and reassembly, restoring the bearing to a serviceable condition. |
Upgrades and Retrofits | Consider upgrades or retrofits that may enhance bearing performance or extend service life, especially in critical applications. |
Proactive Spare Parts Inventory | Maintain a spare parts inventory that includes replacement bearings. This ensures quick access to components when replacements are needed. |
In conclusion, the maintenance and longevity of single row tapered roller bearings are vital to ensure machinery’s reliable operation and minimize downtime. By following best practices for maintenance, implementing effective monitoring strategies, and considering cost-effective solutions when necessary, industries can benefit from the extended service life and consistent performance of these precision-engineered bearings. As we conclude our exploration of single row tapered roller bearings, we’ll recap the significance of precision engineering in their design and application in the final section.
Future Trends and Innovations
As we look ahead to the future of single row tapered roller bearings, it’s clear that this critical component of machinery is poised for exciting developments and innovations. we will explore the evolving trends and innovations in single row tapered roller bearing technology, expected advancements in materials, design, and manufacturing techniques, and how these innovations will impact machinery efficiency and various industrial applications.
Evolving Trends in Single Row Tapered Roller Bearings:
Advanced Materials: The quest for enhanced performance continues to drive the development of advanced materials for tapered roller bearings. Innovations in material science are expected to yield bearings with superior strength, wear resistance, and fatigue life.
Miniaturization: In industries where space is at a premium, there is a growing demand for smaller, more compact bearing solutions. Miniaturized tapered roller bearings are expected to gain prominence in applications such as robotics and medical devices.
Integration of Smart Technologies: Industry 0 and the Internet of Things (IoT) are transforming the way machinery operates. Single row tapered roller bearings are likely to incorporate smart sensors and monitoring capabilities to provide real-time performance data, allowing for predictive maintenance and improved operational efficiency.
Advancements in Design and Manufacturing:
Topology Optimization: Computational techniques like topology optimization are enabling engineers to design bearing structures with optimized load-carrying capacity and reduced weight. This results in more efficient and lightweight bearings.
Precision Engineering: The core of single row tapered roller bearing technology lies in precision engineering. Advancements in manufacturing techniques, including 3D printing and precision machining, will continue to refine the manufacturing process, ensuring the highest standards of accuracy.
Customization: Industries are increasingly seeking customized bearing solutions tailored to specific applications. Manufacturers are expected to offer more options for customization, allowing for optimized bearing configurations based on individual requirements.
Impact on Machinery Efficiency and Industrial Applications:
Enhanced Efficiency: Future innovations in single row tapered roller bearings will contribute to increased machinery efficiency. Reduced friction, improved load distribution, and enhanced wear resistance will lead to higher productivity and lower energy consumption.
Aerospace Advancements: The aerospace industry relies on precision engineering and lightweight components. Innovations in tapered roller bearing technology will play a crucial role in developing aircraft that are more fuel-efficient and reliable.
Automotive Evolution: In the automotive sector, the demand for fuel-efficient and electric vehicles is on the rise. Tapered roller bearings are vital components in transmissions and wheel assemblies. Innovations in materials and design will contribute to more efficient and environmentally friendly vehicles.
In conclusion, the future of single row tapered roller bearings holds promise for significant advancements in materials, design, and manufacturing techniques. These innovations will have a profound impact on machinery efficiency across various industrial sectors, including aerospace, automotive, and manufacturing. As we wrap up our exploration of the precision engineering behind single row tapered roller bearings, let’s take a moment to summarize the key takeaways from this comprehensive guide.
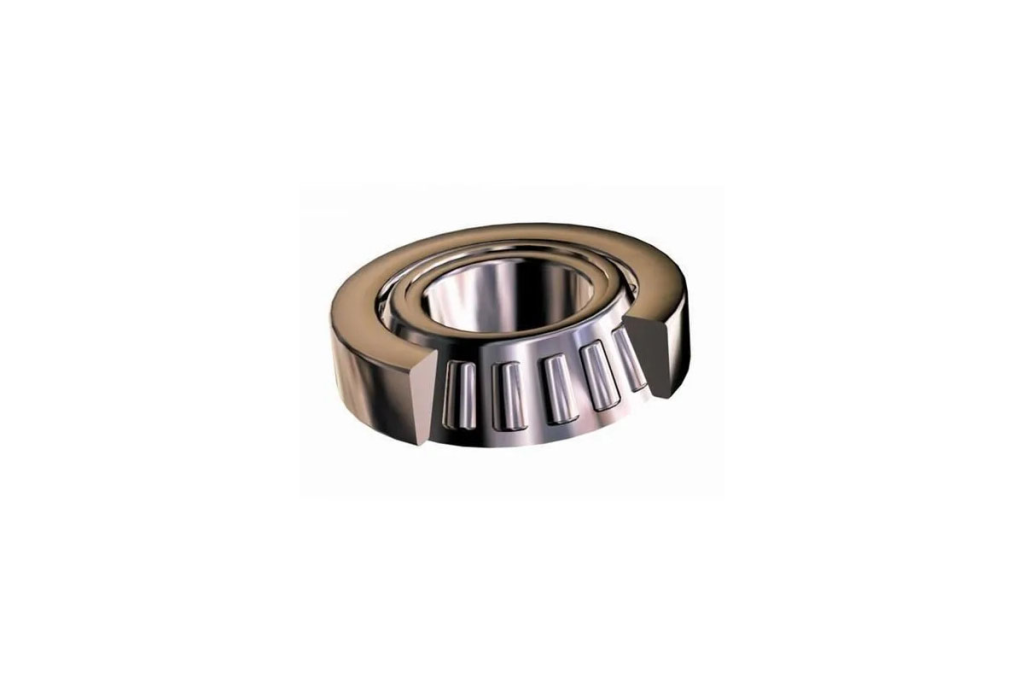
Conclusion
In this comprehensive exploration of single row tapered roller bearings, we have delved deep into the world of precision engineering and the critical role these bearings play in machinery performance across diverse industries. As we conclude our journey through the realm of single row tapered roller bearings, let’s recap the significance of these precision components and underscore the importance of embracing them for improved reliability and productivity.
Significance of Single Row Tapered Roller Bearings:
Single row tapered roller bearings are the unsung heroes of machinery. Their precision design, meticulous engineering, and robust construction make them indispensable in various applications. These bearings excel in handling axial and radial loads, ensuring smooth and efficient machinery operation. They are the cornerstone of precision engineering, providing the necessary support for rotating elements in countless machines.
The Precision Engineering Difference:
Precision engineering is not just a buzzword; it’s the essence of single row tapered roller bearings. The intricate design principles, advanced materials, and meticulous manufacturing processes result in bearings that offer exceptional performance and longevity. Whether it’s reducing friction, increasing load-carrying capacity, or ensuring minimal wear and tear, precision engineering lies at the heart of these bearings.
Leveraging the Benefits:
Industries that rely on machinery cannot afford to overlook the benefits of single row tapered roller bearings. These precision components contribute to improved machinery reliability, reduced downtime, and enhanced productivity. As a result, companies can optimize their operations, reduce maintenance costs, and deliver products and services more efficiently.
A Call to Action:
In closing, we encourage industries and businesses to recognize the value of single row tapered roller bearings. Embracing these precision-engineered components is not merely an investment; it’s a commitment to better performance, increased reliability, and enhanced competitiveness. By integrating these bearings into their machinery, industries can pave the way for a future of precision, efficiency, and innovation.
As we bid farewell to our journey into the world of single row tapered roller bearings, remember that precision engineering is not just a science; it’s a promise of excellence and reliability. It’s a testament to the relentless pursuit of perfection in machinery design and operation. With these bearings as your steadfast partners, the future of precision engineering looks brighter than ever.
FAQs: Common Questions About Single Row Tapered Roller Bearings
we will address some of the frequently asked questions about single row tapered roller bearings. These bearings are critical components in machinery, and understanding them better can help industries and professionals make informed decisions regarding their applications.
What Are Single Row Tapered Roller Bearings?
Single row tapered roller bearings are a type of rolling-element bearing designed to handle both radial and axial loads. They consist of an inner ring, an outer ring, tapered rollers, and a cage to guide the rollers. The inner and outer ring raceways and the rollers’ axes converge at a common point on the bearing’s axis, allowing them to support axial loads in one direction.
Where Are Single Row Tapered Roller Bearings Used?
These bearings find applications in various industries, including automotive, aerospace, construction, and industrial machinery. They are commonly used in vehicle wheel hubs, gearboxes, and differentials, as well as in heavy machinery like mining equipment.
What Are the Advantages of Single Row Tapered Roller Bearings?
Single row tapered roller bearings offer several advantages, including high load-carrying capacity, excellent axial and radial rigidity, and the ability to handle both thrust and radial loads simultaneously. They also provide precise rotational accuracy and are known for their durability.
How Do I Choose the Right Single Row Tapered Roller Bearings for My Application?
Selecting the right bearings involves considering factors such as load capacity, speed, operating temperature, and mounting conditions. It’s essential to consult the manufacturer’s specifications and recommendations to ensure a proper fit for your application.
What Maintenance Is Required for Single Row Tapered Roller Bearings?
Maintenance includes regular lubrication, monitoring for signs of wear, and periodic inspections. Proper lubrication helps reduce friction and wear, extending the bearing’s service life. Any signs of damage or wear should be addressed promptly.
Can Single Row Tapered Roller Bearings Be Replaced or Repaired?
Yes, damaged or worn-out single row tapered roller bearings can be replaced or repaired. However, it’s crucial to follow industry best practices for replacement or repairs to maintain machinery performance and safety.
Are There Any Innovations in Single Row Tapered Roller Bearings?
Advancements in materials, design, and manufacturing techniques continue to drive innovations in single row tapered roller bearings. These innovations lead to bearings with improved performance, reduced friction, and increased longevity.
In conclusion, single row tapered roller bearings are vital components in machinery across various industries. Understanding their features, applications, and maintenance requirements is essential for achieving optimal machinery performance and reliability. If you have more specific questions or need guidance on a particular aspect of these bearings, consult with a qualified bearing expert or the bearing manufacturer for tailored solutions.