NoWear coated bearings
NoWear is a wear-resistant carbon coating that can be applied to the rolling elements and inner ring raceway(s) of a bearing (designation suffix L7DA) or only the rolling elements (designation suffix L5DA) (fig. 1).
A physical vapour deposition process applies the wear-resistant carbon coating. Thickness of the coating ranges from 1 to 3 μm, depending on the size of the bearing. The hardness of the coating is 1 200 HV10.
NoWear coated bearing surfaces retain the toughness of the underlying material while adopting the hardness, improved friction properties and wear-resistance of the coating.
During the running-in period, minute amounts of the coating material are transferred to the counter-surfaces. This coating reduces friction and improves resistance against wear and smearing, even in bearings where only the rolling elements are coated.
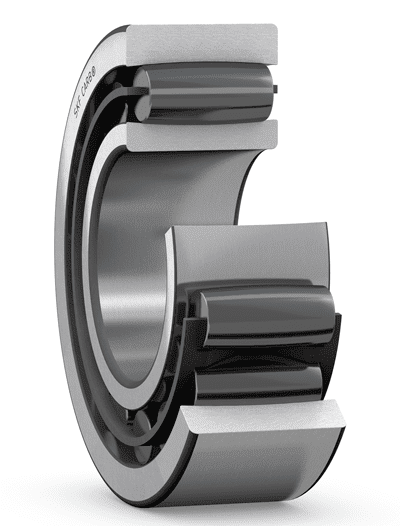
Bearing features
Long service life
Withstand severe operating conditions
increased risk of smearing
insufficient lubricating film
sudden load variations
light loads
rapid speed changes
vibration and oscillations