Introduction
Plain bearings play a crucial role in various industrial applications where friction management and reliable performance are paramount. Tis a comprehensive guide to understanding plain bearings, emphasizing the importance of achieving optimal performance and service life in your application.
Overview of Plain Bearings
Plain bearings, also known as sleeve bearings or bushings, are mechanical components used to reduce friction between moving parts. Unlike rolling-element bearings, which use balls or rollers, plain bearings operate with sliding surfaces. This design choice makes them ideal for applications where simplicity, durability, and cost-effectiveness are priorities.
Importance of Optimal Performance and Longevity in Bearing Applications
Achieving optimal performance and longevity in plain bearings is crucial for several reasons. Firstly, these bearings are often used in heavy-duty machinery and equipment subjected to high loads and harsh operating conditions. Reliable performance ensures operational efficiency and minimizes downtime due to maintenance or failure.
Secondly, longevity is key to reducing lifecycle costs. Bearings that endure longer without significant wear or degradation translate into cost savings through reduced replacement frequency and lower maintenance expenses.
Purpose and Structure of the Manual
The primary purpose of this manual is to provide comprehensive guidance on the selection, installation, operation, and maintenance of plain bearings. It covers various aspects crucial to maximizing the performance and lifespan of plain bearings across different industrial sectors.
Understanding Plain Bearings
Plain bearings are essential components in various industrial applications, providing crucial support and enabling smooth operations in machinery and equipment. delves into the definition, types, key components, materials used, and technical specifications of plain bearings.
Definition and Types of Plain Bearings
Plain bearings, also known as sleeve bearings or bushings, function by providing a sliding surface between two moving parts, such as a shaft and a housing. They operate without the use of rolling elements, relying instead on lubrication to reduce friction and wear. This design makes them suitable for applications where high reliability and low maintenance are required.
Types:
Sleeve Bearings: The simplest form, consisting of a cylindrical sleeve fitted around a shaft.
Flanged Bearings: Similar to sleeve bearings but with a flange to aid in positioning and alignment.
Thrust Bearings: Designed to handle axial loads, providing support for shafts subjected to thrust forces.
Key Components and Materials Used
omponents | Description |
Bearing Surface | Typically made of bronze, brass, or steel, providing the sliding interface in plain bearings. |
Lubrication | Essential for reducing friction and wear; commonly uses oils, greases, or self-lubricating materials. |
Backing Material | Supports the bearing surface and ensures structural integrity of the bearing assembly. |
Materials | Description |
Bronze | Offers excellent wear resistance and corrosion resistance, suitable for various industrial environments. |
Steel | Provides high strength and durability, often used in heavy-duty applications. |
Polymer | Known for its self-lubricating properties and ability to operate without external lubrication, reducing maintenance needs. |
Common Specifications and Technical Details
Specifications:
Inner Diameter (ID) and Outer Diameter (OD): Dimensions crucial for proper fit and function within machinery.
Load Capacity: Indicates the maximum load the bearing can withstand without failure.
Operating Temperature: Defines the range of temperatures at which the bearing can perform effectively.
Clearance: The gap between the shaft and the bearing surface, influencing operational characteristics.
Technical Details:
Friction Coefficient: Measures the resistance to motion when lubricated and under load.
PV Value: Calculated product of pressure and velocity, indicating the maximum load capacity under specific conditions.
Maintenance Intervals: Guidelines for inspection, lubrication, and replacement based on operational hours and environmental factors.
Understanding these aspects of plain bearings is crucial for selecting the right type and ensuring optimal performance and longevity in industrial applications. The next sections will further explore installation, operation, and maintenance practices to maximize the efficiency and lifespan of plain bearings.
provides a comprehensive overview of plain bearings, covering their definition, types, components, materials, specifications, and technical details. It sets the foundation for detailed guidance on effectively utilizing plain bearings to achieve optimal performance and longevity in various industrial settings.
Selection Criteria for Plain Bearings
Choosing the right plain bearings is crucial to ensure optimal performance and longevity in industrial applications. T outlines the factors, including load capacity, speed considerations, environmental factors, and matching bearing types to specific application requirements.
Factors to Consider When Choosing Plain Bearings
Plain bearings serve diverse industrial needs by providing reliable friction management without the use of rolling elements. When selecting these bearings, several factors must be carefully evaluated to match them effectively to the application’s demands.
Load Capacity, Speed, and Environmental Considerations
Load Capacity:
Static Load: The maximum load a bearing can withstand without permanent deformation.
Dynamic Load: The load capacity under moving conditions, considering factors like speed and acceleration.
Impact Load: Temporary loads due to shocks or sudden changes in motion.
Speed Considerations:
Maximum Operating Speed: Determines the rotational or sliding speed at which the bearing can function effectively without overheating or excessive wear.
Lubrication Requirements: Proper lubrication selection based on speed and operating conditions to minimize friction and wear.
Environmental Factors:
Temperature: Operating temperature range that the bearing can withstand without compromising performance.
Corrosive Environments: Resistance to chemicals, moisture, and other environmental factors that could affect bearing lifespan.
Cleanliness Requirements: Bearings used in cleanroom environments or applications with strict contamination control.
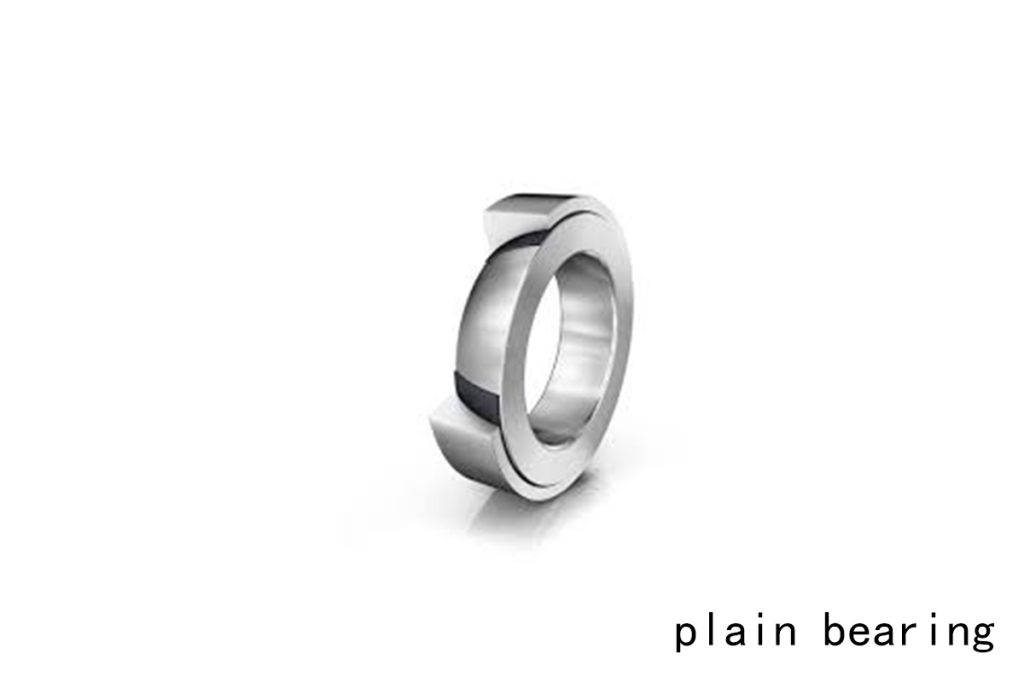
Matching Bearing Type to Application Requirements
Types of Plain Bearings:
Sleeve Bearings: Suitable for low to moderate loads and speeds, commonly used in applications where space is limited.
Flanged Bearings: Provide added stability and alignment control, ideal for applications requiring precise shaft positioning.
Thrust Bearings: Designed to handle axial loads, ensuring stability under thrust forces.
Application-Specific Considerations:
Industrial Machinery: Bearings for heavy-duty machinery requiring high load capacity and durability.
Automotive: Bearings for engine components, chassis systems, and suspension applications.
Aerospace: Bearings for aircraft landing gear, control systems, and flight surfaces.
Conclusion
Choosing the right plain bearings involves a comprehensive evaluation of load capacity, speed capabilities, environmental factors, and specific application requirements. By carefully matching these criteria, industrial operators can optimize performance, enhance reliability, and extend the lifespan of equipment and machinery.
provides a detailed exploration of the selection criteria for plain bearings, highlighting the importance of considering load capacity, speed, environmental factors, and application-specific requirements.
Installation Best Practices
Proper installation of plain bearings is critical to achieving optimal performance and longevity in industrial applications. provides a comprehensive guide to the step-by-step installation process, necessary tools and equipment, and common mistakes to avoid.
Step-by-Step Installation Guide
Preparation:
Inspect Bearing and Components: Ensure the plain bearing and associated parts are free from damage and contaminants.
Prepare Shaft and Housing: Clean and inspect the shaft and housing surfaces for any burrs or imperfections that could affect the bearing’s fit.
Lubrication:
Apply Lubricant: Depending on the type of plain bearing, apply the appropriate lubricant to the bearing surface or shaft to facilitate smooth operation.
Positioning:
Align Bearing: Carefully position the bearing onto the shaft or within the housing, ensuring proper alignment and fit.
Securing:
Secure Bearing: Use fasteners or locking mechanisms to secure the bearing in place, following manufacturer recommendations for torque specifications.
Verification:
Check Alignment: Verify the alignment of the shaft and housing to prevent undue stress on the bearing during operation.
Verify Clearance: Ensure adequate clearance between moving parts to prevent binding or excessive wear.
Testing:
Operational Test: Conduct a test run to verify that the bearing operates smoothly under load conditions without abnormal noise or vibration.
Tools and Equipment Required for Installation
Tools:
Torque Wrench: For accurate tightening of fasteners.
Cleaning Tools: Brushes, solvents, and cloths for cleaning surfaces.
Alignment Tools: Straightedges, feeler gauges, or laser alignment tools to ensure precise alignment.
Equipment:
Lubrication System: Applicators or systems for uniform lubricant application.
Hoisting Equipment: If necessary, for handling heavy bearings or components during installation.
Common Installation Mistakes and How to Avoid Them
Mistakes:
Improper Alignment: Leads to premature wear and failure of the bearing.
Insufficient Lubrication: Causes increased friction and heat generation.
Over-Tightening: Can distort bearings or lead to stress fractures.
Preventive Measures:
Follow Manufacturer Guidelines: Adhere strictly to installation instructions provided by the bearing manufacturer.
Training and Skill: Ensure installers are trained in proper installation techniques and safety protocols.
Regular Inspections: Periodically inspect installed bearings to detect early signs of wear or misalignment.
Conclusion
Proper installation practices are fundamental to maximizing the performance and longevity of plain bearings. By following a systematic approach, using the right tools and equipment, and avoiding common mistakes, industrial operators can ensure that their plain bearings operate efficiently and reliably in various applications.
Lubrication and Maintenance
Proper lubrication and maintenance are essential for maximizing the performance and lifespan of plain bearings in industrial applications. explores the significance of lubrication, types of suitable lubricants, recommended schedules, and routine maintenance practices.
Importance of Proper Lubrication for Plain Bearings
Proper lubrication is critical for plain bearings as it:
Reduces Friction: Minimizes wear between bearing surfaces, enhancing operational efficiency.
Dissipates Heat: Helps in maintaining optimal operating temperatures, preventing overheating and premature failure.
Protects Against Corrosion: Shields bearing surfaces from moisture and contaminants that can lead to corrosion.
Types of Lubricants Suitable for Plain Bearings
Oil-Based Lubricants | Description |
Mineral Oils | Standard lubricants suitable for moderate loads and speeds. |
Synthetic Oils | Provide enhanced performance in extreme temperatures and conditions. |
Biodegradable Oils | Environmentally friendly options suitable for specific applications where eco-friendliness is crucial. |
Grease Lubrication | Description |
Grease Lubrication | Description |
Lithium Grease | Commonly used for general-purpose lubrication in plain bearings. |
Calcium-Based Grease | Offers good water resistance and protection against rust. |
Polyurea Grease | Ideal for high-speed applications due to its shear stability and resistance to oxidation. |
Lubrication Schedules and Methods
Lubrication Schedules:
Regular Intervals: Follow manufacturer recommendations based on operating conditions and load requirements.
Condition-Based: Monitor bearing performance and lubricant condition to adjust lubrication frequency as needed.
Lubrication Methods:
Manual Lubrication: Applying lubricant directly to the bearing surface using oil cans or grease guns.
Automatic Lubrication Systems: Install systems that deliver precise amounts of lubricant at set intervals, reducing maintenance effort and ensuring consistent lubrication.
Routine Maintenance Practices to Ensure Longevity
Inspection:
Visual Checks: Regularly inspect bearings for signs of wear, corrosion, or misalignment.
Measurement: Monitor bearing clearances and play to detect early signs of deterioration.
Cleaning:
Remove Contaminants: Clean bearing surfaces and housings to prevent abrasive particles from causing damage.
Re-lubrication: Flush and replenish lubricants according to maintenance schedules to maintain optimal performance.
Alignment and Installation Checks:
Ensure Proper Alignment: Misalignment can lead to premature wear and failure.
Verify Installation: Check fastener torque and bearing fit periodically to prevent loosening or displacement.
Conclusion
Lubrication and maintenance practices play a crucial role in ensuring the optimal performance and longevity of plain bearings. By selecting appropriate lubricants, adhering to recommended schedules, and implementing routine maintenance practices, industrial operators can maximize efficiency, reduce downtime, and extend the lifespan of their equipment.
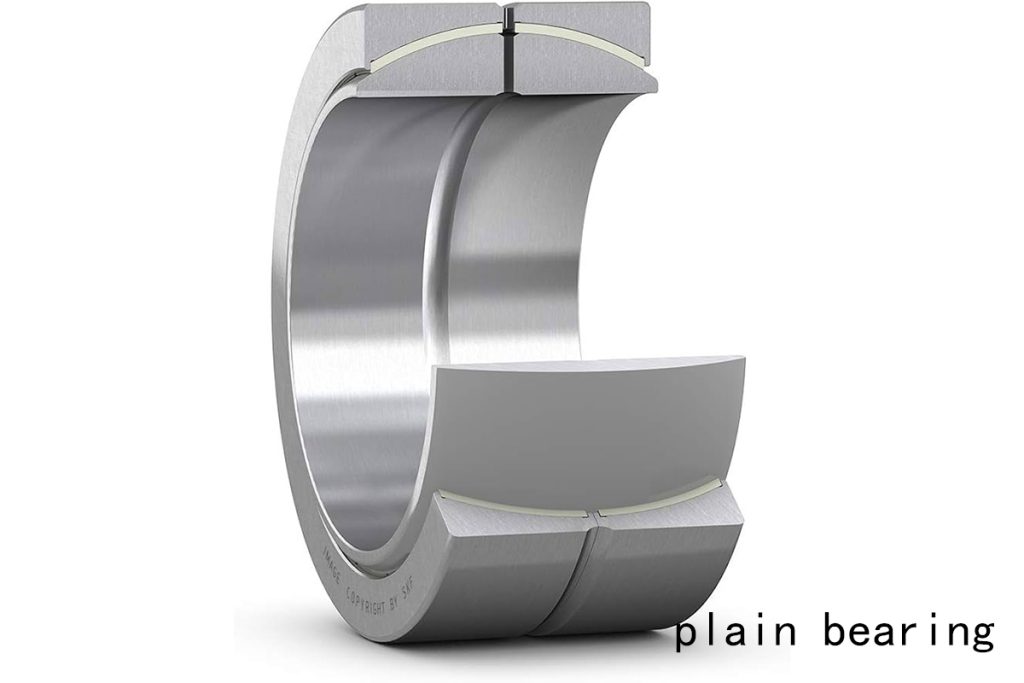
Performance Optimization Techniques
Plain bearings are integral components in industrial machinery, providing crucial support and minimizing friction between moving parts. explores design considerations for enhanced performance, the impact of operating conditions on bearing life, and practical tips for improving efficiency and reliability.
Design Considerations for Enhanced Performance
Bearing Materials:
Bearing Surface: Choose materials such as bronze or steel that offer excellent wear resistance and durability.
Backing Material: Ensure adequate support to maintain structural integrity under varying loads.
Bearing Geometry:
Lubrication Grooves: Incorporate lubrication grooves to enhance oil distribution and reduce frictional heat buildup.
Clearance Design: Optimize clearance to balance load capacity and reduce wear.
Surface Finishes:
Polishing: Smooth bearing surfaces to minimize friction and wear, promoting longer operational life.
Coatings: Apply self-lubricating coatings for enhanced performance in extreme conditions.
Impact of Operating Conditions on Bearing Life
Temperature and Environmental Factors:
Temperature Control: Maintain optimal operating temperatures to prevent thermal degradation and lubricant breakdown.
Contaminants: Protect bearings from dust, moisture, and corrosive substances to extend lifespan.
Load and Speed:
Dynamic Load: Consider load distribution and bearing capacity under varying speeds to prevent premature wear.
Impact Loads: Mitigate shock loads through proper bearing selection and installation.
Tips for Improving Bearing Efficiency and Reliability
Lubrication Management:
Regular Lubrication: Follow manufacturer guidelines for lubrication intervals and use appropriate lubricants.
Monitoring: Implement condition-based lubrication to adjust schedules based on operating conditions and performance.
Alignment and Installation:
Precision Alignment: Ensure accurate alignment of shafts and housings to prevent uneven wear and load distribution.
Proper Installation: Use correct installation techniques to avoid stress concentrations and misalignment.
Maintenance Practices:
Inspection: Conduct routine inspections to detect early signs of wear, corrosion, or misalignment.
Cleaning: Maintain cleanliness of bearing surfaces and housings to prevent contamination and abrasive wear.
Conclusion
Performance optimization of plain bearings requires careful consideration of design, operating conditions, and maintenance practices. By incorporating appropriate design elements, monitoring operating conditions, and implementing effective maintenance strategies, industrial operators can enhance bearing efficiency, reliability, and lifespan.
Troubleshooting Common Issues
Proper maintenance and troubleshooting are crucial for maximizing the performance and longevity of plain bearings in industrial applications. This section focuses on identifying and diagnosing common problems, providing solutions, preventative measures, and when to seek professional assistance.
Identifying and Diagnosing Common Plain Bearing Problems
Excessive Wear:
Symptoms: Increased friction, noise, or vibration during operation.
Causes: Insufficient lubrication, misalignment, or inadequate bearing material hardness.
Diagnosis: Visual inspection for wear patterns and measuring bearing clearances.
Overheating:
Symptoms: Elevated operating temperatures, discoloration of bearing surfaces.
Causes: Inadequate lubrication, excessive load, or poor heat dissipation.
Diagnosis: Monitoring temperature during operation and inspecting lubrication effectiveness.
Noise and Vibration:
Symptoms: Audible noise or noticeable vibration during equipment operation.
Causes: Misalignment, insufficient lubrication, or bearing damage.
Diagnosis: Conducting vibration analysis and visual inspection for damaged components.
Solutions and Preventative Measures
Lubrication Optimization:
Solution: Implementing a proper lubrication schedule using recommended lubricants.
Preventative Measures: Regularly monitor lubricant condition and application to prevent wear and overheating.
Alignment and Installation:
Solution: Ensuring precision alignment of shafts and bearings during installation.
Preventative Measures: Use alignment tools and follow manufacturer guidelines for installation procedures.
Temperature Control:
Solution: Improving heat dissipation through enhanced bearing design or cooling systems.
Preventative Measures: Maintain optimal operating temperatures and monitor environmental conditions.
When to Seek Professional Help
Complex Issues:
Symptoms: Persistent problems despite corrective actions.
Reason: Requires specialized expertise or diagnostic equipment.
Action: Consult with bearing manufacturers or certified technicians for thorough analysis and resolution.
Critical Failures:
Symptoms: Severe damage or operational failure affecting production.
Reason: Immediate intervention to minimize downtime and equipment damage.
Action: Contact emergency maintenance services for prompt resolution.
Conclusion
Troubleshooting common issues with plain bearings involves systematic diagnosis, proactive solutions, and knowing when to involve professional expertise. By addressing problems early, implementing preventive measures, and seeking timely assistance when needed, industrial operators can maintain optimal performance, extend bearing longevity, and ensure reliable operation.
Innovations and Future Trends
Plain bearings continue to evolve with advancements in technology, driving improvements in performance, reliability, and longevity. explores recent innovations, emerging trends, and future developments shaping the landscape of plain bearing technology.
Recent Advancements in Plain Bearing Technology
Advancement | Benefits |
Self-Lubricating Materials | Introduction of composite materials with embedded solid lubricants like graphite or PTFE. Reduces dependency on external lubrication. Enhances wear resistance. Extends maintenance intervals. |
Advanced Coatings | Development of nano-coatings for enhanced durability and reduced friction. Improves performance in extreme conditions. Reduces wear rates. Enhances corrosion resistance. |
Digital Monitoring and Predictive Maintenance | Integration of sensor technology for real-time monitoring of bearing conditions. Enables early detection of abnormalities. Optimizes maintenance schedules. Minimizes downtime. |
Emerging Trends and Their Potential Impact on Performance
Industry 0 Integration:
Trend: Adoption of IoT and machine learning for smart bearing systems.
Impact: Enhances operational efficiency, predicts failure modes, and supports proactive maintenance strategies.
Sustainability Focus:
Trend: Shift towards eco-friendly materials and recyclable bearings.
Impact: Reduces environmental footprint, meets regulatory requirements, and aligns with corporate sustainability goals.
Customization and Application-Specific Solutions:
Trend: Demand for tailored bearing solutions to meet unique performance requirements.
Impact: Optimizes performance in diverse applications such as aerospace, automotive, and renewable energy sectors.
Future Developments to Watch for in the Plain Bearing Market
Nanotechnology Advancements:
Potential: Integration of nanomaterials for superior strength-to-weight ratios and enhanced tribological properties.
Impact: Redefines bearing performance in high-speed and high-load applications.
Energy Efficiency Innovations:
Potential: Development of bearings with lower friction coefficients and energy-efficient designs.
Impact: Contributes to overall system efficiency, reduces energy consumption, and lowers operating costs.
Augmented Reality (AR) and Virtual Prototyping:
Potential: Use of AR for virtual assembly and prototyping of complex bearing systems.
Impact: Accelerates design cycles, enhances precision, and facilitates training and troubleshooting.
Conclusion
The future of plain bearings is marked by continuous innovation and adaptation to meet evolving industrial demands. From self-lubricating materials to digital monitoring and sustainable practices, advancements are poised to elevate performance and longevity. By staying abreast of emerging trends and embracing technological innovations, stakeholders in the plain bearing market can drive efficiency, reliability, and sustainability across diverse applications.
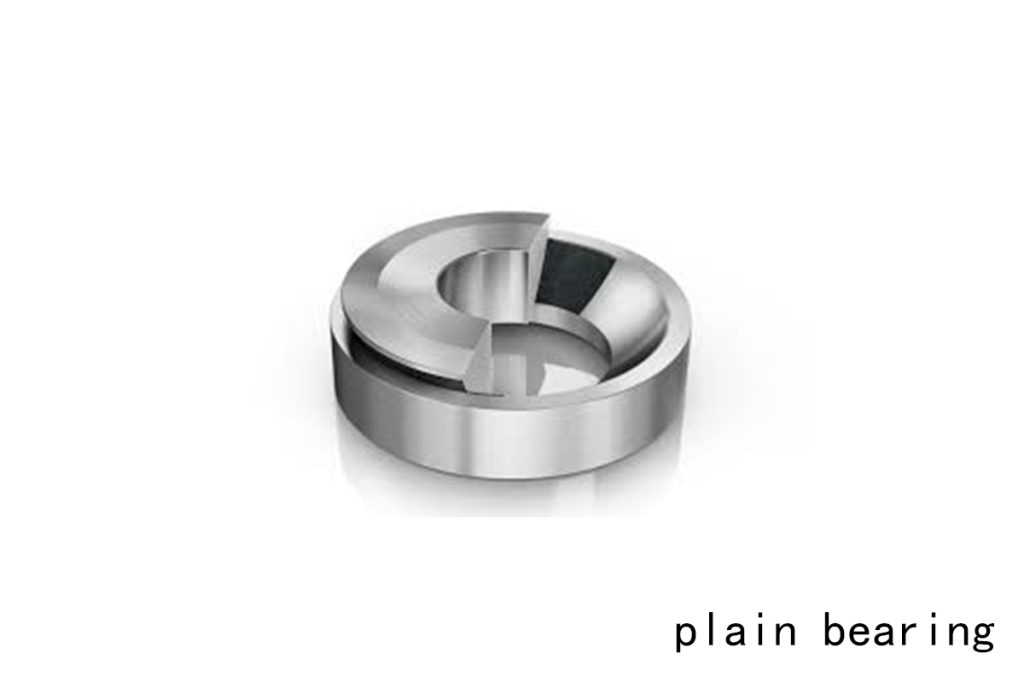
Conclusion
As we conclude this comprehensive manual on plain bearings, we reflect on the key insights, tips, and strategies discussed to enhance their performance and longevity in various industrial applications. This section recaps essential points, offers final tips, and encourages ongoing maintenance and innovation.
Recap of Key Points Covered in the Manual
Throughout this manual, we have explored the fundamental aspects of plain bearings, including their definition, types, materials, and crucial considerations for selection. We delved into installation best practices, lubrication techniques, troubleshooting common issues, and examined recent innovations and future trends in bearing technology.
Key Takeaways:
Understanding the role and importance of plain bearings in industrial machinery.
Factors influencing bearing performance and longevity.
Practical guidance on installation, lubrication, and maintenance.
Insights into advancements and emerging trends shaping the future of bearing technology.
Final Tips for Ensuring Optimal Performance and Longevity of Plain Bearings
Regular Maintenance: Implement a proactive maintenance schedule, including lubrication checks, alignment inspections, and condition monitoring to detect early signs of wear or issues.
Proper Lubrication: Use recommended lubricants and adhere to prescribed schedules to minimize friction, reduce wear, and extend bearing life.
Correct Installation: Ensure precise alignment and proper mounting techniques to prevent premature wear and maximize load-bearing capacity.
Monitoring and Analysis: Embrace digital monitoring tools and techniques for real-time performance tracking, enabling predictive maintenance and proactive interventions.
Continuous Improvement: Stay updated on industry advancements and adopt innovative solutions to optimize efficiency, reliability, and sustainability.
Encouragement for Continuous Maintenance and Innovation
Optimizing the performance and longevity of plain bearings requires a commitment to continuous improvement and proactive maintenance practices. By leveraging technological advancements and embracing new methodologies, industries can achieve higher operational efficiency, reduced downtime, and enhanced equipment reliability.
In conclusion, the journey towards ensuring optimal performance and longevity of plain bearings is a collaborative effort involving meticulous attention to detail, adherence to best practices, and a proactive approach to embracing advancements in bearing technology. By applying the knowledge and strategies outlined in this manual, stakeholders can confidently navigate challenges and leverage opportunities in the dynamic field of plain bearing applications.
This manual serves as a foundational resource for engineers, technicians, and industry professionals seeking to maximize the reliability and efficiency of plain bearings in their operational environments. As technology evolves, so too will the capabilities and performance benchmarks of plain bearings, paving the way for future innovations and advancements in industrial machinery.
FAQs: Common Questions about Plain Bearings
What are plain bearings, and how do they differ from other types of bearings?
Plain bearings, also known as sleeve bearings or journal bearings, are simple devices used to reduce friction between moving parts. Unlike ball bearings or roller bearings, which use rolling elements, plain bearings have a sliding contact surface. They are typically made of materials such as bronze, brass, or polymers and rely on lubrication to minimize friction and wear.
What is an eccentric bearing, and how does it function differently?
An eccentric bearing is a type of plain bearing where the center axis of the bearing is offset from the center of the bore. This eccentricity allows for controlled adjustments in shaft positioning. Eccentric bearings are particularly useful in applications where precise alignment or vibration damping is required, offering flexibility in mechanical designs.
What are the advantages of using eccentric bearings in industrial applications?
Eccentric bearings offer several advantages:
Adjustability: They allow for precise adjustments in shaft positioning.
Vibration Damping: Effective in reducing vibrations and noise.
Compact Design: They can simplify mechanical assemblies.
Low Maintenance: Often self-lubricating and require minimal upkeep.
Where are plain bearings commonly used?
Plain bearings are ubiquitous across various industries:
Automotive: In engines for crankshaft and camshaft support.
Industrial Machinery: In pumps, compressors, and gearboxes.
Aerospace: In landing gear systems and flight control mechanisms.
Marine: In propulsion systems and steering mechanisms.
How should eccentric bearings be lubricated, and why is proper lubrication critical?
Proper lubrication is essential for the performance and longevity of eccentric bearings. Lubricants reduce friction, prevent wear, and dissipate heat generated during operation. It’s crucial to use lubricants recommended by the manufacturer and adhere to lubrication schedules to maintain optimal bearing function.
What maintenance practices are recommended for eccentric bearings?
Key maintenance practices include:
Regular Inspection: Check for signs of wear or damage.
Lubrication Management: Ensure proper lubrication levels.
Alignment Checks: Verify shaft alignment to prevent premature wear.
Environmental Protection: Shield bearings from contaminants and moisture.
How can eccentric bearings contribute to energy efficiency in industrial applications?
By reducing friction and minimizing energy losses, eccentric bearings contribute to overall energy efficiency in machinery. Their low-friction design helps optimize performance and reduce operational costs associated with energy consumption and maintenance.
These FAQs provide a foundational understanding of plain bearings, specifically focusing on eccentric bearings and their applications in various industrial settings. Understanding these principles can help in optimizing bearing selection, maintenance practices, and overall equipment performance.
Robinson, P., & Harris, L. (2015). Maintenance Practices and Performance Optimization of Plain Bearings. Maintenance Engineering