In the realm of precision engineering, there exists a critical component that silently powers a multitude of industrial applications, yet often remains shrouded in mystery. These unsung heroes of machinery are none other than double direction thrust ball bearings. As we embark on this journey to demystify the intricacies of these bearings, it becomes evident that they are pivotal to the seamless operation of numerous industries.
Double direction thrust ball bearings are designed to handle bidirectional axial loads, making them indispensable in scenarios where axial forces need to be precisely managed. Their role in ensuring the smooth functioning of machinery and equipment cannot be overstated. In this exploration, we will delve into the design principles, applications across industries, manufacturing excellence, maintenance strategies, and the future innovations that surround these remarkable components. It is our aim to shed light on the significance of double direction thrust ball bearings and their indispensable role in precision engineering.
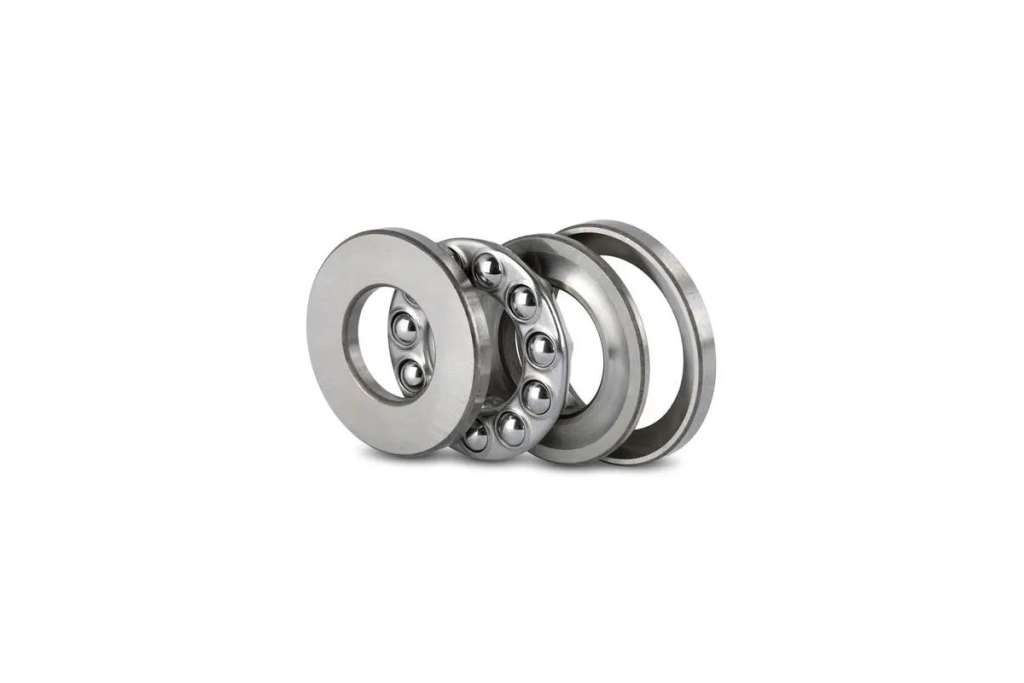
Design and Principles
To truly demystify double direction thrust ball bearings, we must start by delving into the very heart of their design and the principles that govern their operation. These precision components are engineered with meticulous attention to detail, enabling them to perform their crucial role in machinery and industrial applications.
Design Principles
Double direction thrust ball bearings are meticulously designed to handle axial loads in both directions, making them invaluable in scenarios where precision is paramount. The design revolves around the utilization of two sets of balls, held within a cage, and guided by raceways. These components work in tandem to distribute axial loads evenly and efficiently, ensuring optimal performance.
Bidirectional Axial Load Capacity
One of the standout features of double direction thrust ball bearings is their ability to carry axial loads in both directions, often referred to as bidirectional axial load capacity. This characteristic is made possible through the symmetrical design of the bearing, with grooves and raceways carefully engineered to accommodate axial forces from opposing directions. This is particularly crucial in applications where the load direction may change, ensuring the smooth and reliable operation of machinery.
Precision Engineering
The manufacturing of double direction thrust ball bearings demands the highest level of precision engineering. Each component, from the balls to the raceways, must meet strict tolerances to guarantee a perfect fit and smooth operation. The use of advanced materials, cutting-edge machining techniques, and stringent quality control measures ensures that these bearings perform flawlessly under the most demanding conditions.
As we navigate the intricate world of double direction thrust ball bearings, it becomes apparent that their design and principles are the foundation upon which their exceptional performance rests. In the subsequent sections, we will explore their applications across various industries, the manufacturing excellence that goes into their production, strategies for maintenance and longevity, as well as the future innovations set to further elevate their role in precision engineering.
Applications Across Industries
As we continue our journey in demystifying double direction thrust ball bearings, it’s essential to explore the wide array of industries that depend on these precision components to achieve outstanding results. Their versatility and reliability make them indispensable in numerous applications, contributing to the smooth operation of machinery and equipment across various sectors.
Diverse Range of Industries
One of the remarkable aspects of double direction thrust ball bearings is their adaptability to diverse industrial settings. These bearings have found their way into an impressive range of industries, where their unique properties are harnessed to solve specific engineering challenges. Let’s take a closer look at some of the sectors where these bearings play a pivotal role:
Automotive Industry | In the automotive sector, double direction thrust ball bearings are employed in various components, including transmissions and steering systems. Their ability to handle axial loads in both directions ensures the efficient transfer of power and precise control in vehicles. |
Aerospace Sector | Precision is paramount in the aerospace industry, and double direction thrust ball bearings are up to the task. They are utilized in critical applications such as landing gear systems and aircraft engines, where their bidirectional axial load capacity enhances safety and reliability. |
Industrial Machinery | Across a spectrum of industrial machinery, these bearings contribute to the smooth and reliable operation of equipment. Whether in heavy-duty manufacturing machinery or precision instruments, their unique design allows for efficient load distribution, reducing wear and tear. |
Marine Applications | Even in the challenging marine environment, double direction thrust ball bearings find their place. They are utilized in ship propulsion systems and other marine equipment, ensuring the necessary thrust and performance even in corrosive conditions. |
Unique Design Enhancements
The design of double direction thrust ball bearings is a key factor in their widespread application. Their symmetrical configuration, with grooves and raceways engineered to handle axial loads from both directions, sets them apart from other bearing types. This design feature ensures that these bearings can operate seamlessly in various orientations and under changing load conditions.
In summary, the demystification of double direction thrust ball bearings involves understanding the industries that rely on them and recognizing their unique design features. In the following sections, we will delve deeper into the precision manufacturing processes, maintenance strategies, and future innovations that continue to shape the role of these bearings in the world of engineering and industry.
Manufacturing Excellence
In the world of precision engineering, the manufacturing process of double direction thrust ball bearings stands as a testament to human ingenuity and dedication to quality. These remarkable components are essential in various industries, and their flawless performance hinges on the precision with which they are manufactured. In this section, we will embark on a journey through the intricacies of manufacturing excellence, shedding light on the meticulous processes and stringent quality control measures that ensure the reliability and superiority of double direction thrust ball bearings.
Precision Manufacturing Processes
The journey of a double direction thrust ball bearing begins with the selection of high-quality materials, often bearing steel, which forms the foundation of its durability and performance. The manufacturing process that follows is a testament to precision engineering. Here are the key steps involved:
Machining of Components
Precision machinery is used to create the intricate components of the bearing, including the inner and outer rings, ball bearings, and cages. Computer Numerical Control (CNC) machines play a crucial role in achieving the exact dimensions and tolerances required for optimal functioning.
Heat Treatment
The components undergo a carefully controlled heat treatment process to enhance their hardness and resistance to wear. This step ensures that the bearing can withstand the high axial loads it will encounter in its operational life.
Grinding and Assembly
The surfaces of the bearing components are meticulously ground to achieve the required smoothness and precision. The assembly of the bearing involves the placement of precision balls within the grooves, ensuring uniform distribution of load.
Quality Control
Throughout the manufacturing process, stringent quality control measures are in place to monitor dimensions, tolerances, and material properties. Advanced measurement techniques, including laser scanning and coordinate measuring machines, are employed to verify the components’ accuracy.
Quality Control Measures
The reliability and longevity of double direction thrust ball bearings are non-negotiable in industries where precision is paramount. To achieve this, quality control measures are implemented at every stage of manufacturing. These measures include:
Dimensional Inspection
Precise measurements are taken to ensure that each component meets the required specifications. Any deviations are promptly addressed to maintain uniformity.
Material Testing
The quality of the bearing steel is rigorously tested to verify its composition and purity, ensuring it meets the highest industry standards.
Durability Testing
Some bearings undergo extensive durability testing to simulate real-world conditions, including high axial loads and varying temperatures, to ensure they meet performance expectations.
Enhancing Manufacturing Quality
Double direction thrust ball bearings, with their capacity to handle axial loads from both directions, are at the heart of many critical industrial applications. Their exceptional performance relies on the precision manufacturing processes and quality control measures in place. By adhering to these standards of excellence, manufacturers guarantee the reliability and superiority of these bearings, making them a vital component in industries where precision and dependability are paramount.
Maintenance and Longevity
Ensuring the long-term reliability and optimal performance of double direction thrust ball bearings is essential for industries that rely on precision machinery. In this section, we will explore the best practices for maintenance, strategies for monitoring wear and tear, and cost-effective solutions for extending the service life of these critical components.
Best Practices for Maintenance
Proper maintenance is the cornerstone of maximizing the lifespan of double direction thrust ball bearings. Implementing these best practices can significantly contribute to their longevity:
Lubrication
Regularly lubricating the bearings with the appropriate grease or oil is vital for reducing friction and preventing premature wear. The choice of lubricant depends on the application and operating conditions.
Alignment Checks
Periodically checking and adjusting the alignment of the machinery where the bearings are installed helps distribute loads evenly and prevents excessive stress on the bearings.
Temperature Monitoring
Monitoring the operating temperature of the bearings is crucial. Elevated temperatures can indicate issues such as overloading or inadequate lubrication, which need to be addressed promptly.
Cleanliness
Maintaining a clean environment around the bearings is essential. Dust, debris, or contaminants can infiltrate the bearings and accelerate wear. Regular cleaning and sealing mechanisms can help prevent this.
Strategies for Monitoring Wear and Tear
To ensure the early detection of potential issues and to prevent catastrophic failures, implementing monitoring strategies is essential:
Vibration Analysis
Advanced vibration analysis techniques can detect irregularities in bearing operation. Anomalies in vibration patterns can signal problems like misalignment or imbalance.
Noise Monitoring
Unusual noises coming from the bearings can be indicative of problems. Regularly monitoring noise levels can help identify issues before they escalate.
Periodic Inspections
Scheduled inspections, which may include disassembling and inspecting the bearings, can reveal wear, damage, or contamination that might go unnoticed otherwise.
Cost-Effective Solutions for Replacement and Repairs
When maintenance measures are no longer sufficient, and bearings reach the end of their service life, it’s essential to have cost-effective solutions in place:
Timely Replacement | Regularly monitoring the condition of the bearings allows for planned replacements when necessary. This minimizes unexpected downtime and ensures continued productivity. |
Bearing Refurbishment | In some cases, bearings can be refurbished by replacing damaged components or applying specialized coatings. This can be a cost-effective alternative to complete replacement. |
Vendor Partnerships | Establishing partnerships with reliable bearing manufacturers and suppliers can ensure a steady supply of quality replacement bearings at competitive prices. |
Conclusion
In conclusion, the service life and performance of double direction thrust ball bearings can be maximized through diligent maintenance practices, effective monitoring strategies, and cost-effective solutions for replacements and repairs. By adhering to these guidelines, industries can navigate the path to precision and reliability, ensuring that their machinery continues to operate at peak efficiency. In the final section of this article, we will look ahead to the future innovations and sustainability in the realm of double direction thrust ball bearings.
Future Innovations and Sustainability
As we delve into the future of double direction thrust ball bearings, it’s clear that this critical component of precision machinery is on the brink of remarkable advancements. we will explore the evolving trends, innovations, and their contributions to sustainability and efficiency across various industries.
Evolving Trends in Double Direction Thrust Ball Bearings
Materials Advancements
One of the most significant trends in bearing technology is the development of advanced materials. Engineers are exploring new alloys and coatings that can enhance bearing performance, reduce friction, and extend service life.
Miniaturization
With the increasing demand for compact and lightweight machinery, the trend towards miniaturization of double direction thrust ball bearings continues. This allows for more precise and efficient designs in various applications.
Enhanced Sealing Mechanisms
Improved sealing mechanisms are being incorporated into bearing designs to enhance protection against contamination, moisture, and harsh environmental conditions. This is especially crucial in industries like aerospace and automotive.
Innovations in Design and Manufacturing Techniques
3D Printing
Additive manufacturing, particularly 3D printing, is poised to revolutionize bearing production. It offers greater design flexibility, rapid prototyping, and the ability to create complex geometries, leading to custom bearings optimized for specific applications.
Nanotechnology
Nanotechnology is being harnessed to modify bearing surfaces at the molecular level. This technology reduces friction, improves load capacity, and enhances overall performance.
Predictive Maintenance
The integration of sensors and IoT (Internet of Things) technology allows for real-time monitoring of bearing health. Predictive maintenance systems can detect abnormalities and provide data-driven insights for proactive maintenance, reducing downtime and optimizing operations.
Sustainability and Efficiency in Various Industries
Energy Efficiency
Efforts to reduce energy consumption in industrial processes have led to the development of more energy-efficient bearings. These innovations contribute to sustainable practices and cost savings.
Reduced Environmental Impact
Bearings that require less frequent replacement due to longer service life result in fewer discarded components and reduced environmental impact. Sustainability is a driving force behind these advancements.
Increased Reliability
The integration of cutting-edge bearing technology enhances the reliability of machinery, reducing unplanned downtime and improving productivity across industries.
In conclusion, the future of double direction thrust ball bearings is marked by ongoing innovation and a commitment to sustainability. Advancements in materials, design, and manufacturing techniques are shaping a future where precision machinery operates at the highest levels of efficiency and reliability. These bearings, once shrouded in complexity, are gradually being demystified to pave the way for a more precise and sustainable industrial landscape.
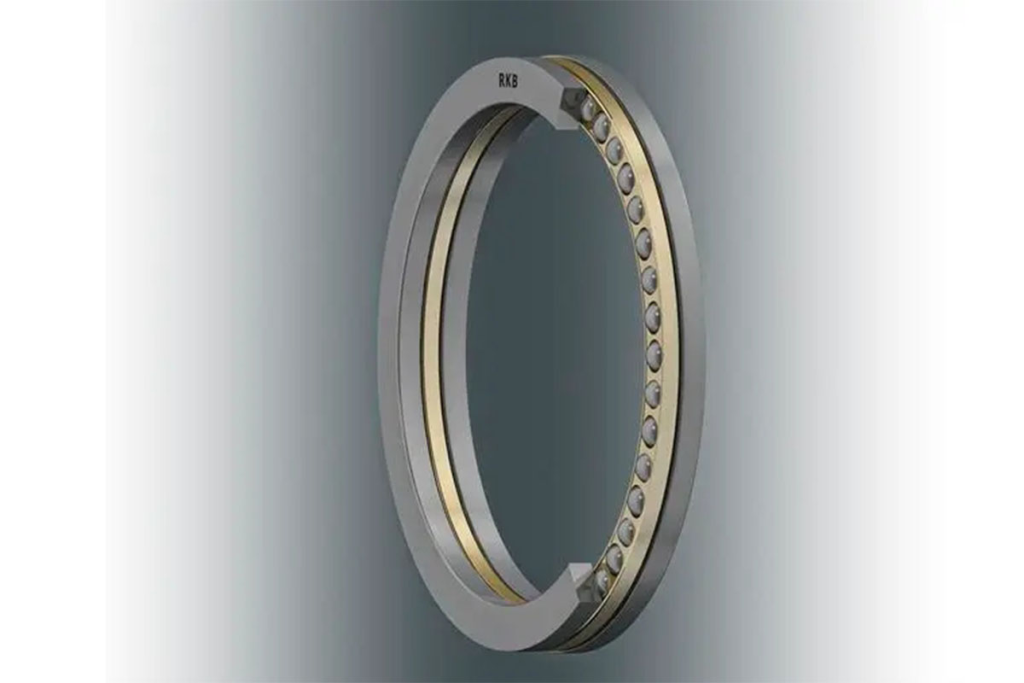
Conclusion
In this comprehensive exploration, we’ve embarked on a journey to demystify double direction thrust ball bearings and their pivotal role in precision engineering. These remarkable components are the unsung heroes behind the smooth and efficient operation of machinery across various industries.
We began our journey by introducing the significance of double direction thrust ball bearings and their central role in precision engineering. As we navigated through the design and principles of these bearings, we uncovered the intricacies that allow them to carry bidirectional axial loads with exceptional precision. Their importance in manufacturing excellence became evident as we delved into the precision manufacturing processes and quality control measures that ensure their reliability.
Exploring their applications across industries, we discovered how double direction thrust ball bearings are the silent force driving automotive, aerospace, and machinery, among others. Their unique design characteristics enhance performance and reliability in a multitude of applications, making them indispensable in modern engineering.
Looking towards the future, we witnessed evolving trends and innovations that promise even greater efficiency and sustainability. Advanced materials, miniaturization, enhanced sealing mechanisms, 3D printing, nanotechnology, and predictive maintenance are reshaping the landscape of bearing technology. These innovations are not only driving energy efficiency but also reducing environmental impact and increasing overall reliability.
In conclusion, double direction thrust ball bearings are the navigational stars guiding precision engineering into the future. Their crucial role in maintaining the performance and reliability of machinery cannot be overstated. As we conclude this journey, we encourage industries to embrace the benefits of these precision components fully. By leveraging the advancements in bearing technology, they can achieve improved reliability, reduced downtime, and enhanced overall performance in their machinery and equipment.
As we bid farewell to the world of double direction thrust ball bearings, we leave with a deeper understanding of their significance, complexities, and the bright future that lies ahead. These demystified components will continue to be the cornerstone of precision engineering, ensuring that machinery operates at the highest levels of efficiency and reliability.
FAQs: Common Questions About Double Direction Thrust Ball Bearings
we will address some common questions and inquiries related to double direction thrust ball bearings. We aim to provide clarity and insights into these precision components, further demystifying their role in the world of engineering and machinery.
What are double direction thrust ball bearings, and how do they work?
– Double direction thrust ball bearings are precision components designed to accommodate axial loads in both directions. They consist of two grooved washers with ball bearings positioned between them. The axial load is transmitted from one washer to the other through the balls, allowing bidirectional load-carrying capacity.
Where are double direction thrust ball bearings typically used?
– These bearings find applications in various industries, including automotive, aerospace, industrial machinery, and more. They are commonly used in applications where axial loads need to be supported, such as in gearboxes, pumps, and machine tool spindles.
What are the advantages of using double direction thrust ball bearings?
– Double direction thrust ball bearings offer high axial load-carrying capacity and precision. They are self-aligning and can accommodate misalignments, making them suitable for applications with slight shaft deflections. Their compact design is advantageous in space-constrained machinery.
How are double direction thrust ball bearings manufactured?
– The manufacturing process involves precision machining of grooved washers and the use of high-quality steel balls. Strict quality control measures are employed to ensure dimensional accuracy and consistency. Lubrication and sealing mechanisms are also integrated during the manufacturing process.
What maintenance practices should be followed to ensure the longevity of these bearings?
– Regular lubrication is essential to minimize friction and wear. Monitoring for signs of wear, such as increased noise or reduced performance, is crucial. Replacement or repairs should be carried out promptly to avoid costly downtime.
Are there any recent innovations in double direction thrust ball bearings?
– Yes, recent innovations include advancements in materials, such as ceramic balls for reduced friction and increased durability. Enhanced sealing mechanisms and predictive maintenance techniques using sensor technology are also emerging trends.
How can industries benefit from leveraging double direction thrust ball bearings?
– Industries can benefit from improved machinery reliability, reduced downtime, and enhanced overall performance. By adopting the latest innovations in bearing technology, they can achieve higher levels of efficiency and contribute to sustainability efforts.
In this FAQ section, we have addressed some of the common questions and inquiries surrounding double direction thrust ball bearings. These precision components continue to play a crucial role in various industries, and understanding their features and applications is key to navigating the world of precision engineering. If you have more specific questions or require further information, please feel free to reach out to our experts in the field.