In the world of bearings and machinery, the significance of flanged housings cannot be overstated. These unassuming components play a crucial role in ensuring the secure mounting of bearings, which is essential for the reliable operation of various mechanical systems. In this article, we will delve into the realm of flanged housings, exploring their design, types, advantages, and best practices for selection and installation. By the end of this journey, you’ll have a comprehensive understanding of why flanged housings are indeed the cornerstone of secure bearing mounting.
Flanged housings, although often overlooked, are pivotal in the field of bearing technology. They provide a stable and secure base for the installation of bearings, ensuring that they are held firmly in place within machinery. This secure mounting is essential to prevent premature wear, reduce friction, and maintain the overall efficiency and performance of the machinery.
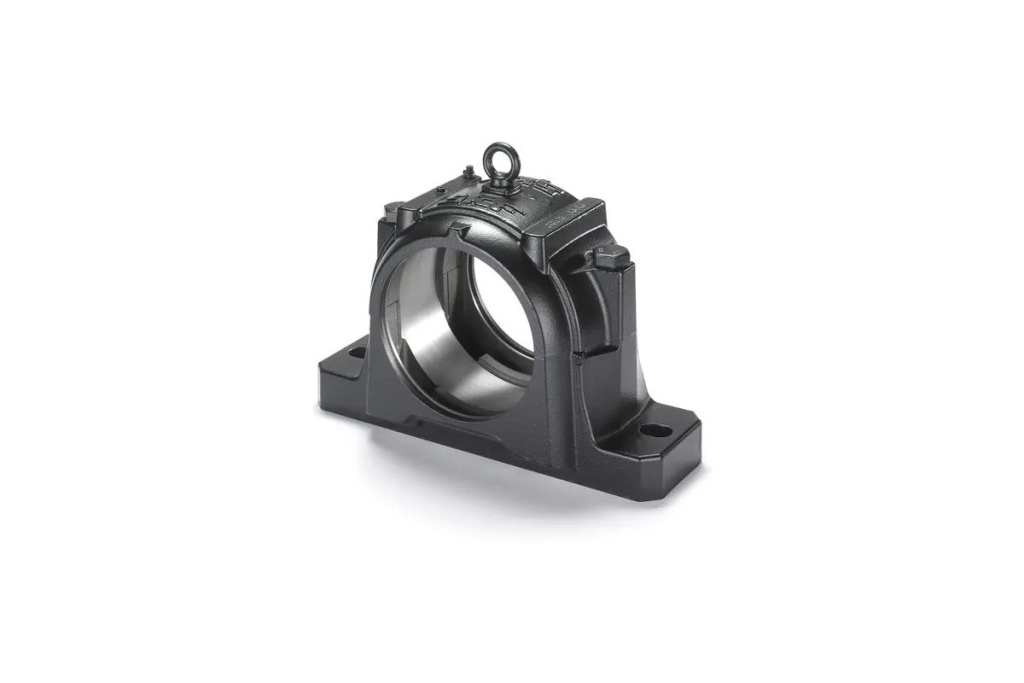
Design and Types of Flanged Housings
Now that we have established the fundamental importance of flanged housings in bearing mounting, let’s delve deeper into their design and explore the various types available in the market. Understanding the intricacies of their design and the range of options will help you make informed decisions when selecting the right flanged housing for your specific needs.
Design of Flanged Housings
Flanged housings are engineered with precision to provide a sturdy and secure platform for bearing installation. They are typically made from robust materials such as cast iron, ductile iron, or various types of steel, ensuring durability and resistance to environmental factors.
The design of flanged housings includes several key components:
Flange: This is the most distinctive feature of a flanged housing, and it provides the mounting surface for the bearing. Flanges come in various shapes, including square, round, or oval, and their dimensions may vary based on the housing’s size and application.
Bore: The bore is the central opening within the housing where the bearing is inserted. It is designed to match the dimensions of the bearing, ensuring a snug fit and proper alignment.
Mounting Holes: Flanged housings are equipped with holes through which bolts or screws are inserted to secure the housing to the machine’s structure. These holes are strategically placed to distribute the load evenly.
Seals and Lubrication: Many flanged housings are designed with integrated seals to protect the bearing from contaminants and retain lubrication. Proper sealing is crucial for extending bearing life and minimizing maintenance.
Types of Flanged Housings
Flanged housings come in a variety of types, each tailored to specific requirements and industries. Some common types include:
Square Flanged Housings | These housings feature a square flange and are suitable for applications where space is limited or when a compact design is preferred. |
Round Flanged Housings | With a round flange, these housings offer stability and versatility. They are commonly used in applications where alignment is critical. |
Oval Flanged Housings | Oval flanged housings combine the benefits of square and round designs, providing a unique solution for certain applications. |
Two-Bolt and Four-Bolt Flanged Housings | The number of bolts used to secure the housing can vary. Two-bolt designs are often used for lighter loads, while four-bolt housings provide added stability and support for heavier loads. |
Take-Up Flanged Housings | These specialized housings are adjustable, allowing for the easy tensioning or alignment of the bearing within the housing. They are commonly used in conveyor systems. |
Understanding the design and types of flanged housings is crucial when selecting the right housing for your bearing application. The choice of housing can significantly impact the performance, longevity, and reliability of your machinery. In the next sections, we will delve further into the advantages of using flanged housings and provide guidance on their selection and installation.
Advantages and Benefits
Flanged housings, often regarded as the unsung heroes of bearing mounting, offer a multitude of advantages and benefits that significantly contribute to the secure and efficient operation of various mechanical systems. we will shed light on the key advantages and real-world applications of flanged housings.
Enhanced Stability and Load Distribution
One of the primary advantages of using flanged housings is their ability to provide enhanced stability to the bearings they support. The flange acts as a secure and rigid foundation, preventing the bearing from shifting or misaligning during operation. This stability is particularly crucial in applications subject to heavy loads, vibrations, or dynamic forces.
Flanged housings also excel at distributing loads evenly across the bearing, mitigating the risk of premature wear and ensuring that the bearing can withstand the demands of its intended application. This even load distribution results in extended bearing life and reduced maintenance requirements.
Precise Bearing Alignment
Proper alignment is paramount when it comes to bearing performance. Flanged housings play a pivotal role in achieving precise bearing alignment, ensuring that the bearing’s load-carrying capacity is fully utilized. This precision alignment not only enhances the efficiency of the mechanical system but also minimizes the risk of bearing damage due to misalignment.
Protection Against Contaminants
In many industrial settings, bearings are exposed to various contaminants such as dust, dirt, moisture, and chemicals. Flanged housings often incorporate effective sealing mechanisms that shield the bearing from these contaminants. This protection not only prolongs the bearing’s service life but also reduces the need for frequent maintenance and replacements.
Versatility in Design
Flanged housings come in a variety of designs, shapes, and sizes to cater to diverse application requirements. Whether you need a square, round, oval, two-bolt, or four-bolt flanged housing, there’s a design to suit your needs. This versatility allows engineers and designers to select the most appropriate housing based on the specific demands of their machinery.
Real-World Applications
Flanged housings find their applications across a wide range of industries and mechanical systems. Some notable examples include:
– Agriculture: Flanged housings are employed in agricultural machinery to support bearings in tillage equipment, tractors, and harvesting machines, ensuring reliable performance in demanding conditions.
– Mining: In the mining industry, flanged housings are utilized to secure bearings in conveyor systems, crushers, and mineral processing equipment, where robustness and durability are paramount.
– Manufacturing: Precision manufacturing equipment relies on flanged housings to maintain the accuracy and longevity of the machinery, contributing to efficient production processes.
– Construction: Cranes, excavators, and construction equipment benefit from flanged housings, ensuring the stability and load-bearing capacity of vital components.
In conclusion, flanged housings serve as the cornerstone of secure bearing mounting, offering advantages such as stability, precise alignment, protection against contaminants, versatility in design, and a wide array of real-world applications. As we continue our exploration, we will delve into essential aspects like the selection and installation of flanged housings to maximize their benefits in various industrial contexts.
Selection and Installation Best Practices
When it comes to achieving secure bearing mounting, the selection and installation of flanged housings play a pivotal role. we will delve into the critical factors that engineers and maintenance professionals need to consider when choosing flanged housings and the best practices for their proper installation.
Factors to Consider in Flanged Housing Selection
Load Capacity and Bearing Size
The first and foremost consideration when selecting flanged housings is the anticipated load capacity and the size of the bearing they will support. Flanged housings come in various sizes and configurations to accommodate different bearing types and sizes. Ensuring compatibility between the housing and bearing is essential for optimal performance.
Environmental Conditions
The operating environment plays a significant role in the choice of flanged housings. Consider whether the application is exposed to extreme temperatures, moisture, corrosive chemicals, or other harsh conditions. In such cases, it is crucial to select flanged housings with appropriate sealing mechanisms and materials to protect the bearing from contaminants and environmental stressors.
Alignment and Precision Requirements
Flanged housings are integral for achieving precise bearing alignment. If your application demands high precision or involves the transmission of axial or radial loads, opt for flanged housings designed to meet these requirements. Precision flanged housings often include features such as dowel pin holes for accurate alignment.
Lubrication and Maintenance
Consider the lubrication needs of the bearing within the flanged housing. Some applications may require frequent lubrication, while others can benefit from self-lubricating flanged housings. Additionally, assess the ease of maintenance and accessibility of lubrication points to ensure the longevity of the bearing.
Industry Standards and Regulations
Adherence to industry standards and regulations is essential for safety and compliance. Ensure that the selected flanged housings meet the relevant standards and guidelines for your industry and application. This step is particularly critical in industries with strict regulatory requirements, such as aerospace or medical devices.
Best Practices for Flanged Housing Installation
Inspection and Cleaning
Before installation, carefully inspect the flanged housing and bearing components for any defects or contaminants. Clean both the housing and the bearing to remove dirt, debris, or any residue that may hinder proper mounting.
Proper Alignment
Achieving precise bearing alignment is paramount. Use alignment tools and methods to ensure that the bearing is correctly positioned within the flanged housing. Misalignment can lead to premature wear and reduced bearing lifespan.
Lubrication
Follow the manufacturer’s recommendations for lubrication. Ensure that the bearing is adequately lubricated to reduce friction and heat generation. Proper lubrication extends the bearing’s service life and enhances its performance.
Torque and Fastening
Use the specified torque values and fasteners recommended by the flanged housing manufacturer. Over-tightening or under-tightening can lead to bearing damage or housing deformation. Proper torque ensures a secure and stable fit.
Sealing and Protection
Verify that sealing elements, if present, are correctly installed and functioning. Adequate sealing protects the bearing from contaminants and extends its operational life. Ensure that protective covers or shields are in place, as required.
In conclusion, selecting the right flanged housing and following best practices during installation are crucial steps in ensuring the secure mounting of bearings. Proper selection and installation not only enhance bearing performance but also contribute to the overall efficiency and reliability of the mechanical system. As we move forward, we will explore maintenance practices and strategies for maximizing the longevity of flanged housings and bearings.
Maintenance and Longevity
Flanged housings are undoubtedly essential components in ensuring the secure mounting of bearings. However, like any other mechanical parts, they require proper maintenance to maximize their service life. we will explore strategies for maintaining flanged housings and cost-effective solutions for replacement and repairs when necessary.
Strategies for Maintaining Flanged Housings
Regular Inspection
Routine inspection of flanged housings is crucial to detect early signs of wear, damage, or misalignment. Inspect for visible cracks, corrosion, or any deviations from the original specifications. Regular inspections help in identifying issues before they escalate.
Lubrication Management
Proper lubrication is vital for reducing friction and preventing premature wear in flanged housings. Follow the manufacturer’s recommendations for lubrication intervals and use the appropriate lubricants. Consider automated lubrication systems for applications that require frequent lubrication.
Environmental Protection
Shield flanged housings from harsh environmental conditions whenever possible. Implement protective measures such as covers or shields to prevent contamination by dust, debris, or moisture. In extremely corrosive environments, consider specialized coatings or materials for added protection.
Alignment Checks
Misalignment can significantly impact the lifespan of flanged housings and the bearings they support. Periodically check and adjust the alignment of the housing to ensure that it remains within tolerance. Proper alignment reduces stress on the bearing and extends its service life.
Temperature Monitoring
Temperature extremes can affect the performance of flanged housings and the bearings they house. Implement temperature monitoring systems to identify overheating or freezing conditions promptly. This proactive approach helps prevent damage caused by temperature-related stress.
Replacement and Repair Solutions
Timely Replacement
Flanged housings have a finite service life, and there may come a point when replacement becomes necessary. When signs of wear or damage indicate that the housing is no longer effective, it is essential to replace it promptly. Delaying replacement can lead to further damage to the bearing and other components.
Cost-effective Repairs
In some cases, repair may be a viable and cost-effective option. Engage with qualified maintenance professionals or technicians who specialize in repairing flanged housings. They can assess the extent of damage and determine whether repair is feasible.
OEM Parts and Expertise
When replacing flanged housings or repairing them, always opt for original equipment manufacturer (OEM) parts. OEM parts are designed to meet the original specifications and ensure compatibility with the bearing. Additionally, seek the expertise of OEM service providers for guidance on proper installation and maintenance.
In conclusion, the longevity of flanged housings is contingent on proper maintenance practices and timely replacement when required. Regular inspections, lubrication management, environmental protection, alignment checks, and temperature monitoring are integral to extending the service life of these critical components. When replacement or repair is necessary, prioritize the use of OEM parts and seek expert assistance to maintain the integrity and security of your bearing mounting system. By following these strategies, you can ensure that flanged housings continue to serve as the cornerstone of secure bearing mounting in various industrial applications.
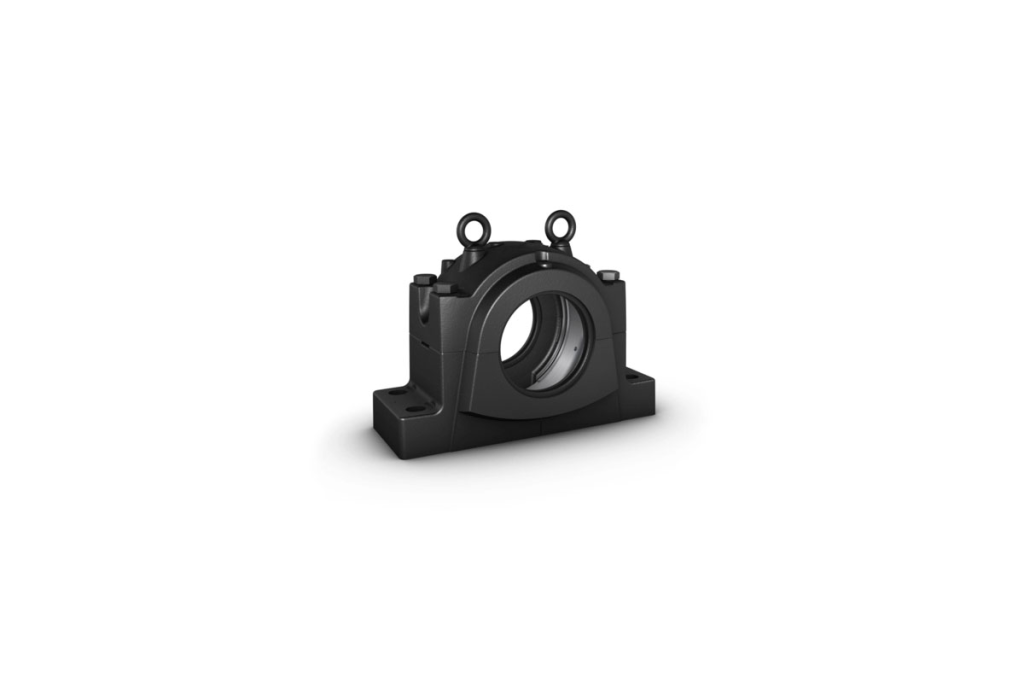
Future Innovations in Flanged Housings
As we delve into the future of flanged housings, it becomes evident that this critical component in bearing mounting is poised for significant advancements. Innovations in design, materials, and manufacturing processes are on the horizon, and they promise to revolutionize the way we approach bearing mounting. we will explore the exciting developments expected in the world of flanged housings and their potential impact on bearing mounting processes and overall performance.
Emerging Trends in Flanged Housing Design
Integration of Smart Technologies
One of the most promising trends is the integration of smart technologies into flanged housing design. IoT (Internet of Things) sensors and monitoring systems will enable real-time data collection on the condition and performance of bearings and housings. This data can be used for predictive maintenance, reducing downtime and preventing catastrophic failures.
Lightweight and High-Strength Materials
Advancements in materials science are driving the development of lightweight yet high-strength materials for flanged housings. These materials will offer improved load-bearing capacity while reducing the overall weight of bearing assemblies. The result is enhanced energy efficiency and reduced operational costs.
Customization and 3D Printing
Flanged housing customization will become more prevalent, allowing manufacturers to tailor designs to specific applications. 3D printing technology will play a significant role in achieving this level of customization. Manufacturers can rapidly produce complex, customized flanged housings, reducing lead times and costs.
Enhanced Sealing and Contamination Prevention
Innovations in sealing technology will lead to flanged housings that provide superior protection against contaminants, moisture, and debris. This advancement is crucial for applications in harsh environments where contamination can compromise bearing performance.
Impact on Bearing Mounting Processes
Streamlined Installation
Future flanged housing designs will prioritize ease of installation. Manufacturers will incorporate features such as self-aligning housings and simplified attachment mechanisms, reducing the time and expertise required for bearing mounting.
Extended Service Life
The use of advanced materials and sealing technologies will contribute to extended service life for both flanged housings and bearings. Bearings will experience less wear and reduced friction, resulting in longer intervals between maintenance and replacement.
Improved Performance Monitoring
Real-time data from smart flanged housings will empower maintenance teams to monitor bearing and housing conditions continuously. This data-driven approach will enable proactive maintenance strategies, reducing unplanned downtime and costly repairs.
Conclusion
The future of flanged housings in bearing mounting is marked by innovation and transformation. Emerging trends in design, materials, and manufacturing processes promise to enhance the performance, longevity, and reliability of bearing assemblies. With the integration of smart technologies, customization options, and improved sealing mechanisms, flanged housings will continue to serve as the cornerstone of secure bearing mounting, setting new standards for efficiency and reliability in various industrial applications. As these innovations take shape, industries that rely on precision bearings can look forward to more robust and efficient machinery, ultimately leading to increased productivity and reduced operational costs.