Introduction
Overview of Bush Bearings and Their Significance
Bush bearings, also known as plain bearings or sleeve bearings, are a fundamental component in a wide range of mechanical applications. These bearings provide a surface for rotating or sliding motion between machine parts, reducing friction and wear. Unlike rolling-element bearings, bush bearings have no moving parts, which makes them simpler, more cost-effective, and often more suitable for high-load, low-speed applications. They are widely used in industries such as automotive, aerospace, manufacturing, and construction.
Bush bearings come in various materials, including bronze, plastic, graphite, and composites, each offering distinct advantages for specific applications. Their ability to support heavy loads, resist corrosion, and operate quietly makes them an essential choice for many engineers and designers.
Importance of Longevity and Performance in Bush Bearings
The longevity and performance of bush bearings are critical factors that influence the overall efficiency and reliability of machinery. Prolonged bearing life reduces the frequency of maintenance and replacements, leading to lower operational costs and minimized downtime. High-performance bush bearings ensure smooth operation, maintain alignment, and prevent damage to other machine components.
Investing in quality bush bearings and adhering to best practices for their maintenance and operation can significantly enhance their lifespan and functionality. Proper selection, installation, lubrication, and regular inspection are essential practices that contribute to achieving optimal performance.
Purpose and Structure of the Guide
This guide aims to provide a comprehensive understanding of bush bearings and offer best practices for maximizing their longevity and performance. It is structured to cover various aspects of bush bearing usage, including:
Selection Criteria: Factors to consider when choosing the right bush bearing for specific applications.
Installation Tips: Best practices for installing bush bearings to ensure proper fit and alignment.
Lubrication and Maintenance: Guidelines for effective lubrication and routine maintenance to extend bearing life.
Common Issues and Troubleshooting: Identifying and addressing common problems associated with bush bearings.
Innovations and Technological Advances: Latest advancements in bush bearing materials and designs that enhance performance.
Case Studies: Real-world examples of successful bush bearing applications and the benefits achieved.
By following the insights and recommendations provided in this guide, engineers and maintenance professionals can optimize the performance and longevity of their bush bearings, ensuring reliable and efficient operation of their machinery.
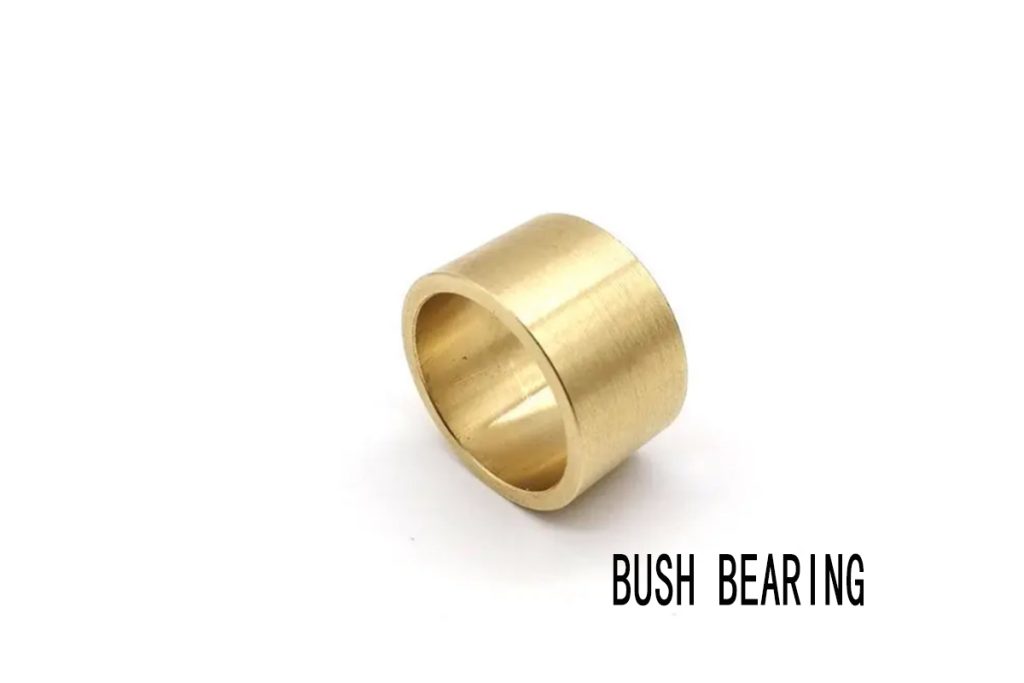
Understanding Bush Bearings
Definition and Types of Bush Bearings
Bush bearings, also known as plain bearings or sleeve bearings, are mechanical components designed to reduce friction between moving parts. They consist of a simple cylindrical sleeve that houses a rotating or sliding shaft. Unlike rolling-element bearings, bush bearings operate on a sliding motion, which allows them to support heavier loads and perform well under high-stress conditions.
There are several types of bush bearings, each suited to specific applications:
Type of Bush Bearing | Description |
Solid Bush Bearings | Made from a single piece of material, these bearings offer high strength and are used in heavy-duty applications. |
Split Bush Bearings | Designed in two halves, these bearings are easier to install and replace, making them ideal for applications requiring frequent maintenance. |
Flanged Bush Bearings | These bearings have a flange at one end, providing an axial locating surface and making them suitable for axial load applications. |
Sintered Bush Bearings | Manufactured using powder metallurgy, these bearings are porous and can retain lubricants, offering self-lubricating properties. |
Composite Bush Bearings | Made from a combination of materials such as metal and polymers, these bearings offer a balance of strength, low friction, and resistance to wear. |
Key Components and Materials Used in Bush Bearings
Bush bearings are constructed from various materials, each chosen for its specific properties that contribute to the bearing’s performance and durability. The key components and materials used include:
Bronze: Known for its excellent wear resistance and high load-carrying capacity, bronze is a common material for bush bearings used in heavy machinery.
Graphite: This material is often used in bush bearings for high-temperature applications due to its self-lubricating properties and resistance to thermal expansion.
Plastic: Bearings made from plastic, such as PTFE (Polytetrafluoroethylene), offer low friction and are corrosion-resistant, making them suitable for chemical and food processing industries.
Composite Materials: These bearings combine metals with polymers or other materials to provide a balance of strength, wear resistance, and low friction.
The selection of materials and components is crucial in ensuring the longevity and performance of bush bearings, as different applications demand specific characteristics.
Common Applications Across Various Industries
Bush bearings are versatile components used in a wide range of industries due to their ability to handle heavy loads and operate in harsh environments. Some common applications include:
Automotive Industry: Used in suspension systems, steering components, and transmission systems for their durability and ability to withstand high loads.
Aerospace Industry: Employed in landing gear, control systems, and actuators where reliability and performance are critical.
Manufacturing Industry: Found in conveyor systems, machinery, and robotic arms, where they facilitate smooth and efficient operations.
Construction Industry: Used in heavy equipment such as cranes, excavators, and loaders due to their robustness and load-carrying capacity.
Marine Industry: Applied in ship propellers, rudder systems, and deck machinery, offering corrosion resistance and long-lasting performance.
By understanding the types, components, and applications of bush bearings, engineers and designers can make informed decisions when selecting the appropriate bearing for their specific needs, ensuring optimal performance and extended service life.
Selection Criteria
Selecting the appropriate bush bearing is critical to ensuring optimal performance and longevity in any application. Several key factors must be considered when choosing the right bush bearing for your specific needs:
Factors to Consider When Choosing Bush Bearings
When selecting a bush bearing, it’s essential to evaluate the following factors to ensure that the bearing meets the application’s requirements:
Material: The material of the bush bearing affects its durability, load capacity, and suitability for various environments. Common materials include bronze, plastic, graphite, and composite materials, each offering specific benefits.
Type of Bearing: Different types of bush bearings, such as solid, split, flanged, sintered, and composite, are designed for specific applications. Understanding the strengths and limitations of each type helps in making an informed decision.
Cost: Budget considerations play a significant role in the selection process. While initial cost is important, consider the long-term value, including maintenance and replacement costs.
Load Capacity, Size, and Speed Considerations
Load capacity, size, and speed are critical factors in selecting the right bush bearing.
Load Capacity: The bearing must support the maximum load it will encounter during operation. Overloading a bush bearing can lead to premature failure and increased wear.
Size: The physical dimensions of the bush bearing must fit the available space within the machinery. Proper sizing ensures that the bearing functions correctly and does not interfere with other components.
Speed: The operational speed of the machinery impacts the choice of bush bearing. Bearings designed for high-speed applications must handle increased friction and heat generation, while low-speed bearings focus more on load capacity.
Environmental Factors (e.g., Temperature, Corrosion Resistance)
Environmental conditions play a crucial role in the performance and longevity of bush bearings. Consider the following environmental factors:
Environmental Factor | Description |
Temperature | High or fluctuating temperatures can affect the material properties of the bush bearing. Bearings made from materials with high thermal stability are suitable for high-temperature applications. |
Corrosion Resistance | In corrosive environments, such as those involving exposure to chemicals or moisture, selecting bush bearings made from corrosion-resistant materials, like certain plastics or composites, is essential. |
Contamination | Dust, dirt, and other contaminants can degrade the performance of bush bearings. Bearings with protective seals or those made from self-lubricating materials can mitigate the impact of contamination. |
By carefully considering these factors, engineers and designers can select the most suitable bush bearing for their specific application, ensuring reliability, efficiency, and extended service life.
Installation Best Practices
Proper installation of a bush bearing is crucial to ensuring its optimal performance and longevity. Following best practices during the installation process can prevent premature wear, operational inefficiencies, and equipment failure. This section provides a step-by-step guide to installing bush bearings, outlines the necessary tools and equipment, and highlights common installation mistakes and how to avoid them.
Step-by-Step Guide to Proper Bush Bearing Installation
Preparation: Begin by cleaning the housing and shaft where the bush bearing will be installed. Ensure that all surfaces are free of dirt, dust, and debris to prevent contamination and ensure a secure fit.
Inspection: Check the bush bearing for any signs of damage or defects. Ensure that the bearing is of the correct size and type for the application.
Lubrication: Apply a thin layer of lubricant to the bearing and the housing. This reduces friction during installation and helps in seating the bearing properly.
Positioning: Carefully position the bush bearing into the housing. Use a press or a gentle tapping tool to ensure the bearing is seated evenly. Avoid using excessive force, as this can damage the bearing or the housing.
Alignment: Ensure that the bearing is aligned correctly with the shaft. Misalignment can cause uneven wear and reduce the bearing’s lifespan.
Securing: Secure the bush bearing in place according to the manufacturer’s recommendations. This may involve tightening screws, bolts, or clamps.
Final Checks: After installation, perform a final inspection to ensure that the bearing is properly seated and aligned. Rotate the shaft by hand to check for smooth operation and ensure that there is no binding or resistance.
Tools and Equipment Required for Installation
Clean Cloths and Cleaning Solution: To clean the housing and shaft.
Inspection Tools: Such as a micrometer or caliper to measure and inspect the bearing and housing dimensions.
Lubricant: Appropriate for the type of bush bearing and application.
Press or Tapping Tool: For seating the bearing into the housing.
Alignment Tools: Such as alignment pins or laser alignment tools to ensure proper bearing alignment.
Securing Tools: Wrenches, screwdrivers, or other tools required to secure the bearing in place.
Common Installation Mistakes and How to Avoid Them
Insufficient Cleaning: Failing to clean the housing and shaft can lead to contamination and premature bearing failure. Always ensure that all surfaces are thoroughly cleaned before installation.
Incorrect Lubrication: Using the wrong type or amount of lubricant can cause excessive wear or bearing failure. Always follow the manufacturer’s recommendations for lubrication.
Excessive Force: Using too much force during installation can damage the bearing or housing. Use appropriate tools and techniques to seat the bearing gently and evenly.
Misalignment: Installing the bearing without ensuring proper alignment can lead to uneven wear and reduced lifespan. Always use alignment tools and check the alignment before securing the bearing.
Neglecting Final Checks: Skipping the final inspection can result in overlooking potential issues. Always perform a thorough check after installation to ensure proper operation.
By following these best practices for bush bearing installation, you can enhance the performance and longevity of your bearings, reducing downtime and maintenance costs in the long run.
Lubrication Techniques
Importance of Lubrication for Bush Bearing Performance
Proper lubrication is critical to the performance and longevity of bush bearings. Lubrication reduces friction between the bearing surfaces, minimizes wear, and prevents overheating. It also acts as a protective barrier against contaminants and corrosion. Without adequate lubrication, bush bearings can experience increased friction, leading to premature wear, operational inefficiencies, and potential failure.
Types of Lubricants Suitable for Bush Bearings
Choosing the right lubricant is essential for maintaining the optimal performance of bush bearings. The following are the most commonly used types of lubricants:
Oil-Based Lubricants: These are ideal for high-speed applications where low friction is required. Oils can penetrate the bearing surfaces easily, providing a consistent lubrication film.
Grease-Based Lubricants: Suitable for applications requiring a thicker lubricant film, grease-based lubricants offer better adhesion and longer-lasting protection. They are especially useful in environments where re-lubrication is infrequent.
Solid Lubricants: These are used in extreme conditions where liquid lubricants may fail. Examples include graphite and molybdenum disulfide, which provide excellent lubrication in high-temperature or vacuum environments.
Self-Lubricating Materials: Some bush bearings are made from materials that contain lubricating properties within their structure, such as sintered bronze or certain polymers. These bearings can operate without additional lubrication, making them suitable for maintenance-free applications.
Proper Lubrication Methods and Schedules
To ensure the best performance of bush bearings, it is important to follow proper lubrication methods and schedules. Here are some best practices:
Lubrication Method | Description |
Initial Lubrication | During installation, apply a thin layer of the chosen lubricant to both the bearing and the housing. This initial lubrication helps reduce friction during the first operation. |
Regular Re-Lubrication | Depending on the application and operating conditions, regular re-lubrication is necessary to maintain optimal performance. Follow the manufacturer’s recommendations for re-lubrication intervals. |
Manual Lubrication | For applications requiring manual lubrication, use a grease gun or oil dispenser to apply the lubricant directly to the bearing surfaces. Ensure that the lubricant is evenly distributed and that there are no air pockets. |
Automated Lubrication Systems | In high-maintenance or hard-to-reach applications, automated lubrication systems can provide consistent and precise lubrication. These systems can be programmed to deliver the right amount of lubricant at regular intervals. |
Monitoring and Maintenance | Regularly monitor the condition of the lubricant and the performance of the bush bearings. Check for signs of lubricant degradation, contamination, or insufficient lubrication, and take corrective action as needed. |
Environmental Considerations | Consider the operating environment when selecting and applying lubricants. In high-temperature or corrosive environments, choose lubricants specifically designed to withstand these conditions. |
By adhering to these lubrication techniques, you can significantly enhance the performance and longevity of your bush bearings. Proper lubrication reduces friction, prevents wear, and ensures smooth operation, ultimately leading to reduced maintenance costs and improved equipment reliability.
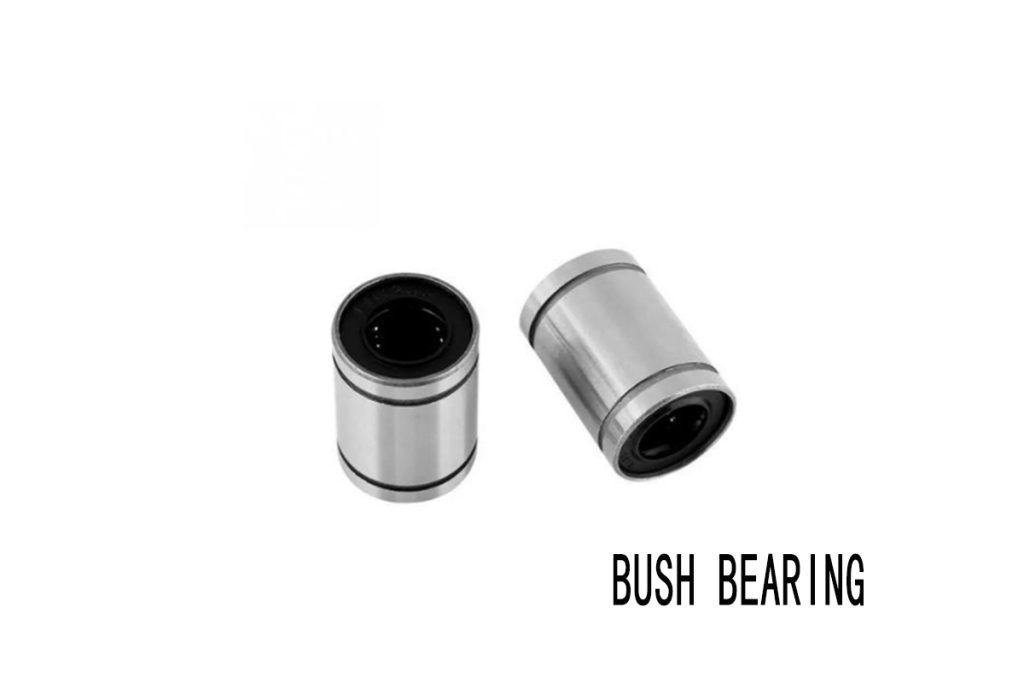
Maintenance and Care
Routine Maintenance Procedures for Bush Bearings
Proper maintenance of bush bearings is crucial for ensuring their longevity and optimal performance. Regular inspections and maintenance routines can prevent unexpected failures and extend the lifespan of the bearings. Here are the essential routine maintenance procedures for bush bearings:
Inspection and Cleaning: Regularly inspect the bush bearings for signs of wear, contamination, or damage. Clean the bearings and surrounding areas to remove dust, dirt, and other debris that can cause abrasion and increase friction.
Lubrication: Ensure that the bush bearings are properly lubricated according to the manufacturer’s specifications. Regularly check the lubricant levels and quality, and reapply lubrication as needed. This helps to reduce friction, minimize wear, and prevent overheating.
Alignment Checks: Misalignment can cause uneven wear and reduce the lifespan of bush bearings. Periodically check and adjust the alignment of the bearings to ensure they are properly seated and aligned with the shaft and housing.
Load and Speed Monitoring: Monitor the load and speed conditions of the bush bearings to ensure they are operating within the recommended limits. Excessive loads or speeds can cause premature wear and failure.
Temperature Monitoring: Keep an eye on the operating temperature of the bush bearings. Abnormally high temperatures can indicate insufficient lubrication, excessive loads, or other issues that need to be addressed.
Signs of Wear and Tear to Look For
Recognizing the signs of wear and tear in bush bearings can help prevent failures and extend their service life. Here are some common indicators to watch for:
Unusual Noises: Squealing, grinding, or knocking noises can indicate that the bush bearings are worn or damaged. These noises are often caused by insufficient lubrication, contamination, or excessive wear.
Vibration: Excessive vibration or wobbling in the equipment can be a sign that the bush bearings are misaligned, worn, or damaged. Vibration analysis can help identify the source of the problem.
Increased Operating Temperature: A significant increase in the operating temperature of the bush bearings can indicate lubrication issues, excessive loads, or internal damage. Regular temperature monitoring can help detect these problems early.
Visible Damage: Inspect the bush bearings for visible signs of wear, such as scoring, pitting, or cracking. These physical signs indicate that the bearings are deteriorating and may need to be replaced.
Reduced Performance: If the equipment is not operating as efficiently as it should, it could be due to worn or damaged bush bearings. Performance issues such as reduced speed, increased energy consumption, or decreased accuracy can all be linked to bearing wear.
Tips for Extending the Lifespan of Bush Bearings
To maximize the lifespan of your bush bearings, follow these best practices:
Proper Installation: Ensure that bush bearings are installed correctly, following the manufacturer’s guidelines. Improper installation can lead to misalignment, uneven wear, and premature failure.
Regular Maintenance: Implement a routine maintenance schedule that includes regular inspections, cleaning, lubrication, and alignment checks. Consistent maintenance helps to identify and address issues before they become serious problems.
Use Quality Lubricants: Choose high-quality lubricants that are compatible with your bush bearings and the operating conditions. Proper lubrication is essential for reducing friction, minimizing wear, and preventing overheating.
Control Operating Conditions: Monitor and control the operating conditions, such as load, speed, and temperature, to ensure they remain within the recommended limits. Avoid overloading or running the bearings at excessive speeds.
Environmental Protection: Protect the bush bearings from environmental contaminants such as dust, dirt, and moisture. Use protective seals or covers to prevent contamination and ensure a clean operating environment.
Timely Replacement: Replace bush bearings at the first sign of significant wear or damage. Continuing to use worn bearings can lead to more serious equipment failures and higher repair costs.
By following these maintenance and care guidelines, you can ensure that your bush bearings perform reliably and have a long service life. Proper attention to maintenance not only enhances performance but also reduces the likelihood of unexpected downtime and costly repairs.
Innovations and Advances
Recent Technological Advancements in Bush Bearing Design
The bush bearing industry has seen significant technological advancements in recent years, driven by the need for improved performance, durability, and efficiency. These innovations have led to the development of bush bearings that offer enhanced load capacities, reduced friction, and extended service life. One of the key advancements is the incorporation of advanced manufacturing techniques, such as precision machining and additive manufacturing (3D printing), which allow for the creation of complex bearing geometries with greater accuracy and consistency. Additionally, the use of computer-aided design (CAD) and simulation tools has enabled engineers to optimize bush bearing designs for specific applications, resulting in bearings that are better suited to withstand the demands of modern machinery.
New Materials and Their Benefits
The introduction of new materials has also played a crucial role in advancing bush bearing technology. Traditional materials like bronze and brass are being supplemented or replaced by advanced composites, polymers, and ceramics, each offering unique benefits:
Advanced Composites: These materials combine the strength of metals with the lightweight and low-friction properties of polymers. Composite bush bearings are particularly advantageous in applications where weight reduction is critical, such as in aerospace and automotive industries.
Polymers: High-performance polymers, such as PTFE (Polytetrafluoroethylene) and PEEK (Polyether ether ketone), provide excellent chemical resistance, low friction, and self-lubricating properties. These materials are ideal for applications involving corrosive environments or where lubrication is difficult.
Ceramics: Ceramic bush bearings offer superior hardness, high-temperature resistance, and exceptional wear resistance. They are suitable for high-temperature applications and environments with abrasive particles.
These new materials not only enhance the performance of bush bearings but also contribute to longer service life and reduced maintenance requirements.
Future Trends in Bush Bearing Manufacturing
Looking ahead, several trends are likely to shape the future of bush bearing manufacturing:
Smart Bearings: The integration of sensors and IoT (Internet of Things) technology into bush bearings is expected to become more prevalent. Smart bearings can provide real-time data on operating conditions, such as temperature, load, and vibration, enabling predictive maintenance and reducing the risk of unexpected failures.
Sustainable Manufacturing: As environmental concerns continue to grow, the bush bearing industry is moving towards more sustainable manufacturing practices. This includes the use of eco-friendly materials, energy-efficient production processes, and the development of recyclable or biodegradable bearings.
Customization and Flexibility: Advances in manufacturing technologies, such as 3D printing, will allow for greater customization and flexibility in bush bearing design. This means that bearings can be tailored to meet the specific needs of different applications, leading to improved performance and efficiency.
Enhanced Surface Treatments: Innovations in surface treatment technologies, such as coatings and surface texturing, will enhance the properties of bush bearings. These treatments can improve wear resistance, reduce friction, and provide additional protection against corrosion and environmental contaminants.
Nanotechnology: The application of nanotechnology in bush bearing manufacturing holds promise for creating materials with superior properties. Nano-coatings and nano-composites can enhance the strength, durability, and thermal stability of bearings, pushing the boundaries of what is possible in bearing performance.
In conclusion, the ongoing advancements in bush bearing design, materials, and manufacturing processes are paving the way for bearings that are more efficient, durable, and adaptable to the evolving needs of various industries. By staying abreast of these innovations, manufacturers and users can ensure that they are utilizing the most advanced and effective bush bearings available, thereby optimizing the performance and longevity of their machinery and equipment.
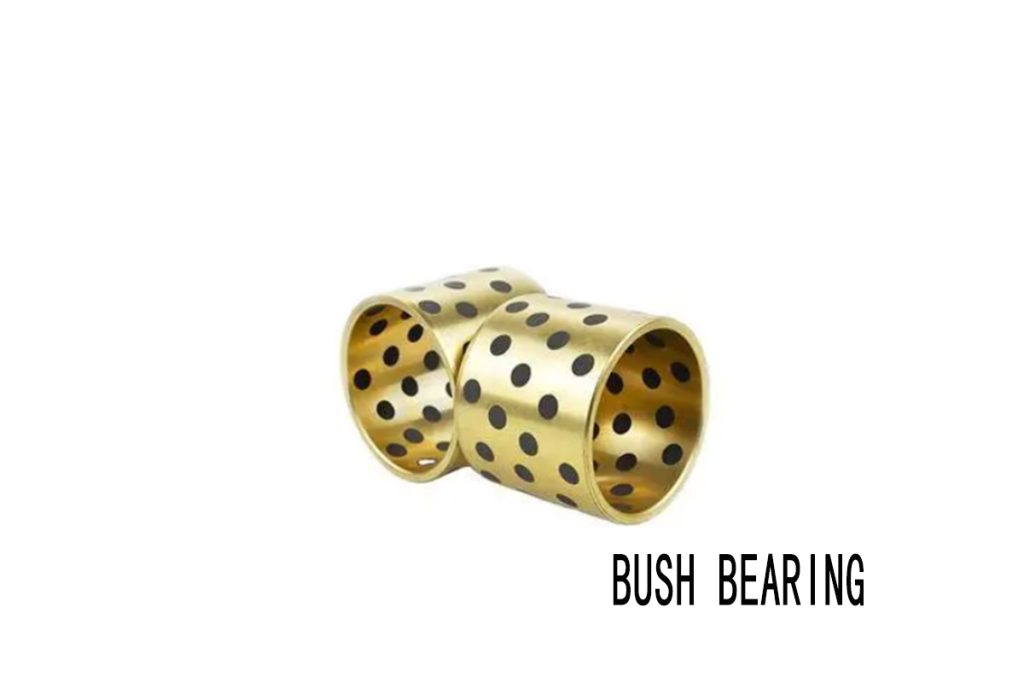
Conclusion
Summary of Key Points Covered in the Guide
This Bush Bearing Guide: Best Practices for Longevity and Performance has provided a comprehensive overview of the essential aspects to consider when working with bush bearings. We began by understanding what bush bearings are and their various types, followed by the crucial criteria for selecting the right bearings for specific applications. We delved into the importance of proper installation techniques and the necessity of regular lubrication to ensure optimal performance. The guide also covered routine maintenance procedures and highlighted signs of wear and tear to watch out for, along with offering tips to extend the lifespan of bush bearings.
Final Thoughts on the Importance of Proper Bush Bearing Care
The longevity and performance of bush bearings are significantly influenced by how well they are maintained and cared for. Proper selection, installation, lubrication, and maintenance are not merely best practices but essential steps that ensure the efficiency and reliability of machinery. Neglecting these aspects can lead to premature bearing failure, increased downtime, and higher operational costs. Thus, understanding and implementing these best practices is vital for anyone involved in the maintenance and operation of equipment that utilizes bush bearings.
Encouragement for Continuous Learning and Application
The field of bush bearings is continually evolving, with ongoing advancements in materials, design, and technology. Staying informed about the latest developments and continually refining maintenance practices can lead to improved performance and extended service life of the bearings. We encourage readers to engage in continuous learning and apply the knowledge gained to their specific applications. By doing so, they can ensure the optimal performance and longevity of their bush bearings, thereby enhancing the overall efficiency of their machinery and operations.
FAQs: Common Questions About Bush Bearings
What are the main types of bush bearings?
Bush bearings come in several types, including solid bush bearings, split bush bearings, flanged bush bearings, sintered bush bearings, and composite bush bearings. Each type offers unique benefits and is suitable for specific applications.
How often should bush bearings be lubricated?
The lubrication schedule for bush bearings depends on the application and operating conditions. Regular re-lubrication is necessary to maintain optimal performance. Always follow the manufacturer’s recommendations for lubrication intervals.
What are the signs of wear and tear in bush bearings?
Common signs of wear and tear include unusual noises, increased vibration, overheating, and visible damage to the bearing surface. Regular inspection and maintenance can help identify and address these issues early.
Can bush bearings operate without lubrication?
While some bush bearings, such as sintered and certain polymer bearings, can operate with minimal lubrication, most require regular lubrication to reduce friction and prevent wear. Always refer to the manufacturer’s guidelines for the specific lubrication requirements of your bearings.
How do I choose the right bush bearing for my application?
When selecting bush bearings, consider factors such as load capacity, size, speed, and environmental conditions like temperature and corrosion resistance. Proper selection ensures that the bearing can withstand the operational demands and enhances its longevity.
What is the importance of proper installation for bush bearings?
Proper installation is crucial for ensuring that bush bearings function correctly and have a long service life. Incorrect installation can lead to misalignment, increased wear, and premature failure. Following a step-by-step installation guide and using the right tools can help avoid common mistakes.
By addressing these common questions, we aim to provide a clear understanding of bush bearings and promote best practices for their use and maintenance. With the right knowledge and approach, users can ensure their bush bearings perform optimally and last longer, contributing to the overall efficiency and reliability of their equipment.
Miller, A., & Chen, H. (2022). “Recent Innovations in Bush Bearing Design and Technology.” Journal of Advanced Manufacturing Technology,