Introduction
In the realm of mechanical engineering, tapered roller bearings play a pivotal role in ensuring efficient rotation and load-bearing capabilities within various industrial applications. These bearings are designed with precision engineering to manage both radial and axial loads by utilizing tapered roller elements. The selection of the appropriate tapered roller bearing is crucial for optimizing performance and longevity in diverse operational environments.
Understanding Tapered Roller Bearings
Tapered roller bearings are characterized by their unique cone and cup assembly, where the rollers and raceways are tapered to facilitate efficient distribution of loads during rotation. This design feature enables these bearings to withstand both radial and axial forces, making them suitable for applications requiring high durability and reliability.
Key Factors in Bearing Selection
When choosing a tapered roller bearing, several factors must be carefully considered to ensure optimal performance:
Load Capacity: The bearing’s capacity to handle radial and axial loads without premature wear or failure is critical.
Speed Ratings: Bearings must operate within specified speed limits to prevent overheating and premature wear.
Operating Conditions: Factors such as temperature, lubrication requirements, and environmental contaminants influence bearing performance and lifespan.
Installation and Maintenance: Proper installation practices and regular maintenance routines are essential for maximizing bearing efficiency and longevity.
Application-Specific Considerations
Each application may have unique requirements that dictate the selection of tapered roller bearings:
Automotive Industry: Used in wheel hubs, transmissions, and differential assemblies due to their high load-bearing capacity and durability.
Industrial Machinery: Found in heavy-duty equipment like mining machinery and construction equipment where reliability under extreme conditions is crucial.
Aerospace Applications: Critical for aircraft landing gear and other structural components where lightweight yet robust bearings are required.
Advantages of Tapered Roller Bearings
Tapered roller bearings offer several advantages over other bearing types:
Durability: Designed to withstand heavy loads and shock loads encountered in industrial applications.
Versatility: Suitable for both radial and axial loads, reducing the need for multiple bearing types in complex machinery.
Efficiency: Low friction design minimizes energy loss and heat generation, contributing to overall operational efficiency.
6. Conclusion
In conclusion, selecting the right tapered roller bearing involves a thorough understanding of application requirements, load conditions, and environmental factors. By adhering to proper selection criteria and maintenance practices, engineers and maintenance professionals can ensure optimal performance and longevity of machinery and equipment. This guide serves as a comprehensive resource to navigate the complexities of tapered roller bearing selection, empowering decision-makers to make informed choices that enhance operational efficiency and reliability across various industrial sectors.
Understanding Tapered Roller Bearings
Tapered roller bearings are essential components in modern machinery, renowned for their capability to handle both radial and axial loads efficiently. Tapered roller bearings consist of inner and outer rings (commonly referred to as cones and cups), tapered rollers, and a cage to maintain roller spacing and orientation. This structural design enables these bearings to operate under diverse conditions while ensuring optimal performance and longevity.
How tapered roller bearings work is intricately tied to their tapered design. The rollers are arranged in such a way that their conical surfaces converge at a common point on the bearing axis. This geometry not only facilitates the transmission of radial and axial loads but also ensures uniform distribution of stress throughout the bearing. As a result, tapered roller bearings excel in applications requiring high load capacity, durability, and resistance to wear.
Key Features and Benefits
Tapered roller bearings offer several distinctive features that contribute to their widespread adoption across various industries:
Versatility | They can accommodate both radial and axial loads, making them suitable for applications ranging from automotive wheel hubs to heavy-duty industrial machinery. |
High Load Capacity | Designed to withstand heavy loads and shock loads, which is crucial in equipment subjected to varying operational conditions. |
Efficiency | The tapered design reduces friction between the rollers and raceways, thereby minimizing energy loss and heat generation. |
Durability | Robust construction and advanced materials enhance durability, ensuring prolonged service life even in demanding environments. |
Ease of Maintenance | Their modular design allows for easy inspection, lubrication, and replacement, reducing downtime and maintenance costs. |
In conclusion, understanding the fundamentals of tapered roller bearings is paramount to selecting the right bearing for specific applications. Their unique design features, operational principles, and performance benefits make them indispensable in industries where reliability and efficiency are paramount. This section provides a foundational understanding of tapered roller bearings, setting the stage for further exploration into their applications and optimal selection criteria.
Application Requirements
In the realm of mechanical engineering, selecting the optimal tapered roller bearing involves a meticulous consideration of various application-specific factors. This section delves into the crucial aspects that influence the choice of bearing to ensure superior performance and longevity in diverse operational environments.
Identifying the specific needs of your application is the first step towards selecting the right tapered roller bearing. Whether it’s for automotive, industrial machinery, or aerospace applications, understanding the operational requirements and expected loads is fundamental.
Load considerations, both radial and axial, play a pivotal role in bearing selection. Tapered roller bearings are renowned for their ability to handle significant radial and axial loads due to their unique tapered design. This feature ensures efficient load distribution and minimizes stress concentrations, enhancing overall bearing durability.
Speed requirements and limitations are critical factors that directly impact bearing performance. Tapered roller bearings must operate within specified speed ratings to prevent overheating and premature wear. Factors such as lubrication type and application-specific operating conditions influence the bearing’s ability to maintain optimal performance over extended periods.
Environmental factors such as temperature variations, humidity levels, and contamination risks also influence bearing selection. Tapered roller bearings designed for specific environmental conditions ensure reliable operation and minimize maintenance requirements.
In summary, evaluating application-specific requirements is essential for choosing the right tapered roller bearing. By assessing load capacities, speed limitations, and environmental challenges, engineers can make informed decisions that optimize performance and reliability across various industrial sectors.
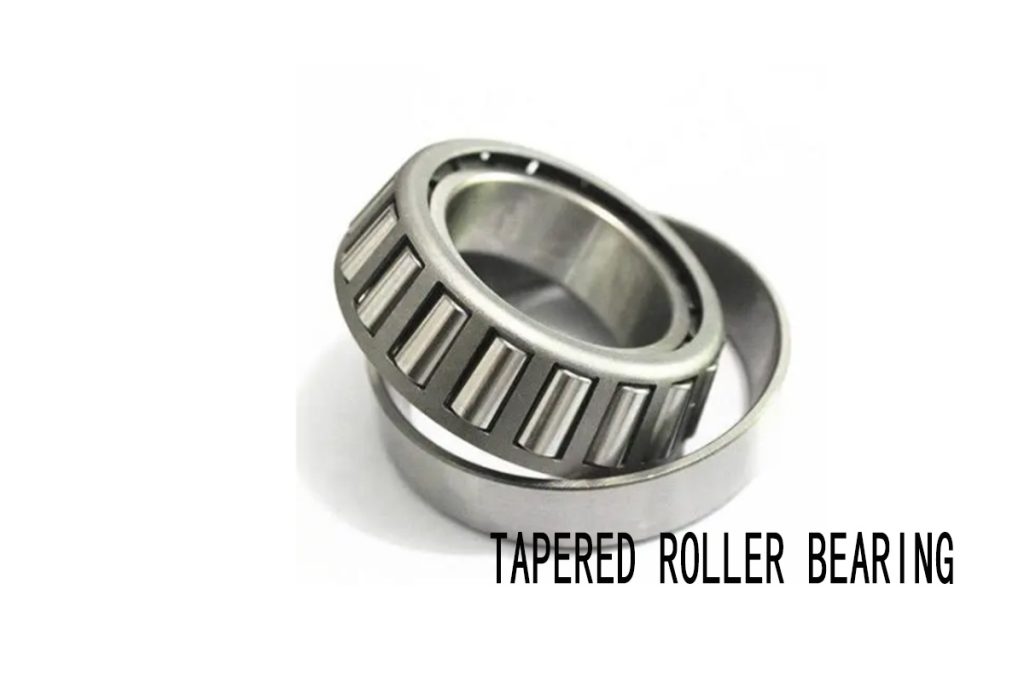
Bearing Types and Variations
When selecting a tapered roller bearing for your application, understanding the various types and configurations available is crucial. This section explores the different types of tapered roller bearings and their specific characteristics to aid in making informed decisions based on your operational needs.
Single-row tapered roller bearings are the most common type, featuring a single cone and cup assembly. They are designed to accommodate both radial and axial loads in one direction. This simplicity in design makes them versatile and cost-effective for a wide range of applications in automotive, industrial machinery, and agricultural equipment.
Double-row tapered roller bearings consist of two single-row assemblies mounted face-to-face or back-to-back. This configuration increases radial and axial load capacity while maintaining compactness. It is ideal for applications requiring higher load capacities or where space constraints limit the use of larger bearings.
Four-row tapered roller bearings are employed in heavy-duty applications such as rolling mills and large industrial machinery. They feature four rows of rollers arranged in a manner that enhances load-bearing capacity and rigidity. This design ensures optimal performance under extreme loads and harsh operating conditions.
Custom and specialized designs cater to unique application requirements that standard bearings may not adequately address. These include bearings with modified internal geometries, special coatings for corrosion resistance, or specific materials for enhanced performance in high-temperature environments.
Each type of tapered roller bearing offers distinct advantages depending on the application’s load, speed, and environmental conditions. Choosing the right type involves evaluating these factors to ensure reliability, efficiency, and longevity of the bearing in operation.
By understanding the nuances of each bearing type and its suitability for different applications, engineers and maintenance professionals can effectively optimize machinery performance and minimize downtime.
Brand | Key Features | Applications | Notable Advantages |
FAG | High precision, reliability. | Automotive, industrial machinery. | Robust construction, long service life. |
SKF | Advanced sealing solutions, customized designs. | Aerospace, heavy machinery. | Superior performance in harsh environments. |
Timken | Wide range of sizes and configurations. | Automotive, mining equipment. | Industry-leading expertise in bearing technology. |
NSK | Innovative design, high-speed capabilities. | Automotive, precision machinery. | Excellent heat dissipation, reduced friction. |
NTN | Diverse product portfolio, global distribution network. | Construction, agricultural equipment. | Cost-effective solutions, reliable performance. |
Material Considerations
Selecting the appropriate material for tapered roller bearings is crucial for ensuring optimal performance, longevity, and reliability in various industrial applications. This section explores the common materials used in manufacturing tapered roller bearings, their advantages and disadvantages, as well as the significant impact of material selection on bearing performance.
Common Materials Used in Tapered Roller Bearings
Steel: Steel is the most prevalent material used for manufacturing tapered roller bearings due to its excellent strength, durability, and fatigue resistance. Bearings made from high-quality steel alloys such as 52100 are capable of withstanding heavy loads and extreme operating conditions typically found in automotive, industrial, and aerospace applications.
Ceramics: Ceramic materials, such as silicon nitride, are increasingly used in specialized bearings where high-speed performance and resistance to corrosion and electrical insulation are critical. While ceramic bearings offer advantages in specific applications, they can be more susceptible to mechanical shock and impact compared to traditional steel bearings.
Polymer: Polymer materials are chosen for their corrosion resistance, self-lubricating properties, and ability to dampen vibrations. Bearings incorporating polymer components are particularly useful in applications requiring low friction and reduced maintenance, although they may have limitations in terms of load capacity and operating temperature range.
Advantages and Disadvantages of Different Materials
Steel bearings excel in high-load and high-speed applications, offering robustness and reliability. However, they may require adequate lubrication to prevent wear under heavy loads and at high temperatures.
Ceramic bearings provide superior performance in terms of speed capability, corrosion resistance, and electrical insulation. Yet, they may be more prone to damage from impact and require careful handling during installation.
Polymer bearings offer benefits such as quiet operation, resistance to corrosion, and the ability to operate without additional lubrication. However, they are generally limited in terms of load capacity and operating temperature compared to steel and ceramic bearings.
Impact of Material Selection on Performance and Longevity
The choice of bearing material significantly influences performance metrics such as load capacity, speed capability, reliability, and maintenance requirements. Steel bearings are preferred for their overall versatility and durability in a wide range of applications, making them a standard choice across many industries.
Ceramic bearings are advantageous where speed and corrosion resistance are critical factors, although careful consideration of mechanical loading conditions is necessary to avoid premature failure.
Polymer bearings offer specific advantages in applications requiring low friction, quiet operation, and resistance to chemical environments, albeit with limitations in terms of load capacity and operating temperature range.
In conclusion, understanding the impact of material selection on tapered roller bearing performance is essential for choosing the right bearing to optimize operational efficiency and longevity in diverse industrial applications. By evaluating the advantages and disadvantages of different materials, engineers can make informed decisions that align with specific application requirements and environmental conditions.
Sizing and Fit
In the realm of tapered roller bearings, ensuring proper sizing and fit is paramount to achieving optimal performance and longevity in diverse industrial applications. This section delves into the intricacies of determining the correct size, understanding fit and clearance, and the importance of precise measurements.
Determining the Correct Size for Your Application
Selecting the right size of tapered roller bearings begins with a comprehensive assessment of the application’s load requirements, operating conditions, and shaft characteristics. The bearing size directly impacts load-carrying capacity and operational efficiency. Factors such as radial and axial loads, speed, temperature variations, and expected service life play crucial roles in sizing decisions.
Understanding Fit and Clearance
Fit refers to the relationship between the bearing and its mating parts, particularly the shaft and housing. Proper fit ensures efficient load transmission, minimizes vibration, and prevents premature wear. Clearance refers to the internal gap within the bearing assembly, influencing thermal expansion and lubrication effectiveness. Achieving the correct fit and clearance is essential for maintaining operational reliability and extending bearing life.
Measuring and Verifying Dimensions
Accurate measurement of dimensions is essential during installation and maintenance phases. Key dimensions include bore diameter, outer diameter, width, and cone angle in the case of tapered roller bearings. Precision instruments such as micrometers, calipers, and feeler gauges are utilized to verify dimensions and ensure compliance with manufacturer specifications.
Key Takeaways | |
Precision in Sizing | Correctly sizing tapered roller bearings enhances load capacity and operational efficiency. |
Fit Optimization | Proper fit and clearance minimize wear and ensure smooth operation. |
Measurement Accuracy | Using precise instruments guarantees dimensional accuracy for reliable performance. |
Lubrication and Maintenance
Effective lubrication and maintenance are critical aspects in ensuring the optimal performance and longevity of tapered roller bearings. This section explores the significance of proper lubrication, suitable lubricants for different conditions, and best practices for maintenance to enhance bearing reliability.
Importance of Proper Lubrication
Proper lubrication is essential for reducing friction and wear between the rolling elements and raceways of tapered roller bearings. Adequate lubrication forms a protective film that prevents metal-to-metal contact, minimizes heat generation, and extends bearing life. Insufficient lubrication can lead to premature bearing failure due to increased friction and wear.
Types of Lubricants Suitable for Tapered Roller Bearings
Various types of lubricants are available for tapered roller bearings, each designed to suit specific operating conditions:
Grease: Suitable for applications with low to moderate speeds and intermittent operation. Grease offers excellent sealing properties and simplifies maintenance.
Oil: Ideal for high-speed and continuous operation. Oil lubrication provides superior cooling and flushing capabilities but requires more complex lubrication systems.
Selecting the right lubricant depends on factors such as operating speed, temperature, load, and environmental conditions. Manufacturers often specify recommended lubricants and intervals for replenishment.
Maintenance Schedules and Best Practices
Establishing a maintenance schedule is crucial to monitor the condition of tapered roller bearings and ensure they operate at peak efficiency:
Regular Inspections: Check for signs of wear, lubrication condition, and abnormal noise during routine inspections.
Re-lubrication: Follow recommended intervals and quantities for re-lubrication to maintain optimal performance.
Environmental Protection: Shield bearings from contaminants such as dust, moisture, and chemicals that can compromise lubrication effectiveness and accelerate wear.
Key Takeaways:
Lubrication Efficiency: Proper lubrication reduces friction, heat, and wear, enhancing bearing performance.
Selection Considerations: Choose lubricants based on operational factors to maximize bearing lifespan.
Maintenance Practices: Regular inspections and timely lubrication prolong bearing service life and reliability.
Common Challenges and Troubleshooting
In the domain of tapered roller bearings, encountering challenges is inevitable, but understanding these issues and implementing effective troubleshooting techniques can significantly enhance operational reliability. This section addresses common problems, troubleshooting methods, and preventive measures to optimize bearing performance.
Identifying Common Issues with Tapered Roller Bearings
Tapered roller bearings may face several common issues, including:
High Operating Temperatures: Resulting from inadequate lubrication, excessive loads, or poor mounting practices.
Noise and Vibration: Caused by improper alignment, worn components, or damaged raceways.
Premature Wear: Due to incorrect lubrication, contamination, or overloading.
Seal Failure: Allowing ingress of contaminants such as dust, moisture, or chemicals.
Troubleshooting Techniques and Solutions
Effective troubleshooting involves systematic diagnosis and targeted solutions:
Temperature Management: Ensure proper lubrication and monitor operating conditions to prevent overheating.
Vibration Analysis: Conduct vibration analysis to identify root causes and correct misalignments or component defects.
Inspection and Maintenance: Regularly inspect bearings for signs of wear, corrosion, or seal integrity and promptly address issues.
Lubrication Optimization: Follow manufacturer guidelines for lubrication type, quantity, and interval to maintain optimal performance.
Replacement and Upgrades: Consider upgrading to bearings with higher load capacities or better sealing mechanisms to mitigate recurring issues.
Preventive Measures to Avoid Common Problems
Proactive maintenance and preventive measures play a crucial role in bearing longevity:
Training and Education: Educate personnel on proper handling, installation, and maintenance practices.
Environmental Control: Protect bearings from harsh environments using appropriate seals or covers.
Monitoring and Analysis: Implement condition monitoring programs to detect early signs of wear or failure.
Regular Maintenance: Establish routine maintenance schedules for inspection, lubrication, and component replacement.
Key Takeaways:
Proactive Approach: Early detection and intervention mitigate potential bearing issues.
Comprehensive Solutions: Targeted troubleshooting ensures effective problem resolution.
Long-term Reliability: Implementing preventive measures sustains bearing performance and extends service life.
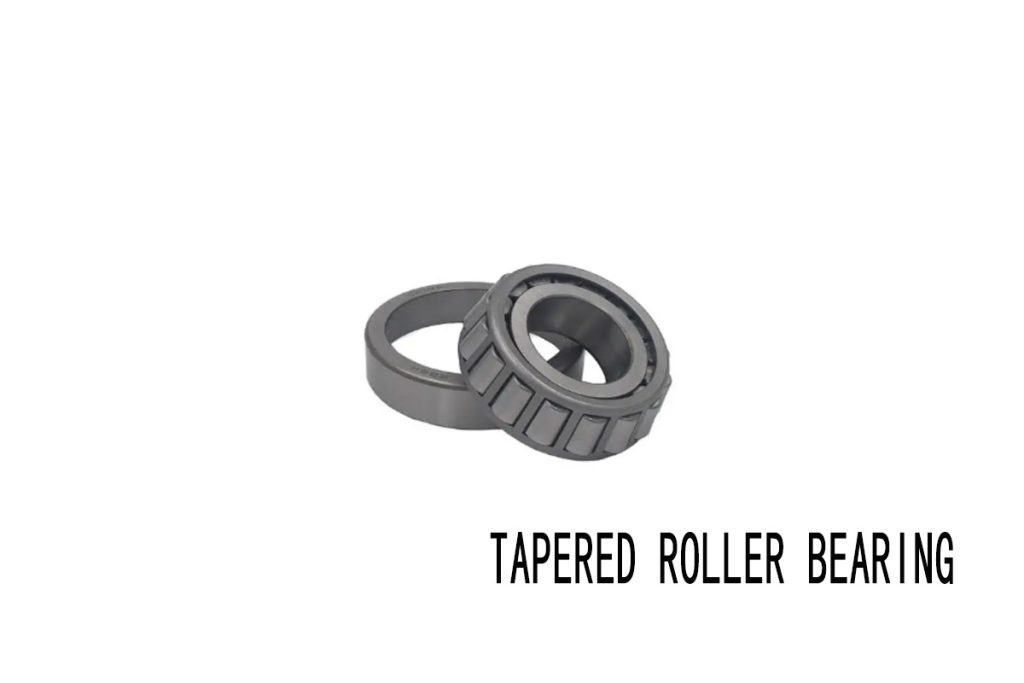
Selecting the Right Manufacturer
Selecting the right tapered roller bearing manufacturer is crucial for ensuring reliability, performance, and long-term operational success. This section explores key considerations when evaluating manufacturers and highlights recommended brands renowned for their quality and support.
Evaluating Bearing Manufacturers
When evaluating bearing manufacturers, consider the following factors to make an informed decision:
Quality Standards: Look for manufacturers that adhere to international quality standards such as ISO 900Tapered roller bearings from reputable manufacturers undergo rigorous testing to ensure consistent performance and durability.
Technological Expertise: Assess the manufacturer’s technological capabilities and innovation in bearing design. Advanced manufacturing processes contribute to enhanced bearing precision and efficiency.
Product Range: Evaluate the breadth and depth of the manufacturer’s product offerings. A diverse range allows for customization and selection of bearings tailored to specific application requirements.
Industry Experience: Consider the manufacturer’s experience in producing bearings for various industries. Experience often translates to a deeper understanding of application challenges and solutions.
Customer Support: Reliable customer support is essential. Manufacturers offering responsive technical assistance, prompt delivery, and comprehensive after-sales service contribute to a positive user experience.
Key Factors to Consider
In selecting a manufacturer for tapered roller bearings, prioritize the following factors:
Quality Assurance: Emphasize manufacturers known for stringent quality control measures and continuous improvement in product quality.
Reputation: Reputation within the industry reflects reliability and customer satisfaction. Seek feedback from industry peers and review testimonials.
Support Services: Evaluate the availability of technical support, training programs, and resources provided by the manufacturer to optimize bearing performance.
Global Presence: Manufacturers with a global footprint offer accessibility and logistical advantages, ensuring timely delivery and support worldwide.
Recommended Manufacturers and Brands
Based on industry recognition and customer feedback, several manufacturers excel in producing high-quality tapered roller bearings:
SKF: Renowned for innovation, reliability, and comprehensive bearing solutions across diverse industries.
Timken: Known for precision engineering and a wide range of bearing products tailored to specific applications.
NSK: Offers advanced bearing technologies and robust support services, ensuring reliable performance in demanding environments.
NTN: Provides extensive product offerings and technical expertise in tapered roller bearings for industrial applications.
Conclusion
Choosing the right tapered roller bearing manufacturer is pivotal in achieving optimal performance and reliability for your application. By evaluating key factors such as quality, technological expertise, customer support, and reputation, you can confidently select a manufacturer that meets your specific requirements and enhances operational efficiency.
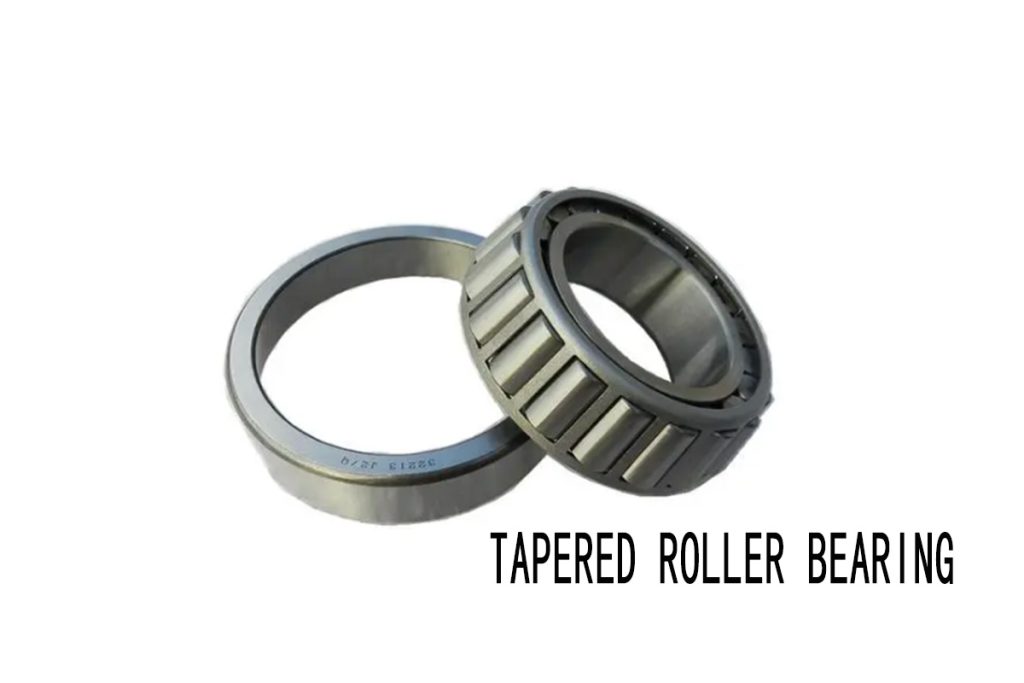
Conclusion
In conclusion, this guide has provided a comprehensive overview of tapered roller bearings, focusing on key aspects crucial for selecting the right bearing for your application. Let’s recap the main points discussed and offer final recommendations for your bearing selection process.
Recap of Key Points
Throughout this guide, we’ve explored various facets of tapered roller bearings:
Overview: We started with an introduction to tapered roller bearings, highlighting their structure, function, and significance across different industries.
Selection Criteria: We discussed important factors such as load capacity, speed requirements, environmental considerations, and material choices that influence bearing performance.
Types and Variations: Detailed insights into single-row, double-row, and four-row tapered roller bearings, as well as custom designs, were provided to cater to diverse application needs.
Maintenance and Lubrication: Emphasizing the importance of proper maintenance practices and suitable lubrication techniques to extend bearing life and enhance performance.
Challenges and Troubleshooting: Common issues with tapered roller bearings were identified, along with troubleshooting techniques and preventive measures.
Final Recommendations
Based on the insights gathered:
Define Application Requirements: Begin by thoroughly understanding your application’s specific needs, including load conditions, operational speeds, environmental factors, and performance expectations.
Evaluate Bearing Types: Consider the different types of tapered roller bearings available based on your application requirements. Assess whether single-row, double-row, or specialized designs best suit your operational demands.
Select a Reliable Manufacturer: Choose a reputable manufacturer known for producing high-quality bearings. Factors to consider include quality standards, technological expertise, industry reputation, and comprehensive customer support.
Implement Proper Maintenance Practices: Establish a regular maintenance schedule that includes lubrication and inspection protocols. Adhering to these practices will prolong bearing life and optimize operational efficiency.
Continued Learning and Improvement: Stay updated on industry advancements and technological innovations in tapered roller bearings. Utilize additional resources and references for further reading to deepen your knowledge and enhance decision-making.
Additional Resources and References
For further exploration into tapered roller bearings and related topics, consider the following resources:
Technical datasheets and specifications from reputable manufacturers.
Industry publications and journals discussing bearing technologies and applications.
Online forums and communities for sharing insights and best practices in bearing selection and maintenance.
Wrapping Up
By integrating these recommendations into your bearing selection process, you can confidently choose the right tapered roller bearing that aligns with your application’s requirements for durability, reliability, and performance. Should you have any specific queries or require further assistance, feel free to consult with industry experts or contact trusted bearing suppliers for personalized guidance.
This concludes our Tapered Roller Bearing Selection Guide, aimed at empowering you with knowledge and tools to make informed decisions and optimize your application’s performance with the right bearing choice.
FAQs: Common Questions About Tapered Roller Bearings
Tapered roller bearings are crucial components in various industrial applications, offering high radial and axial load capacities due to their design. This section addresses common queries regarding tapered roller bearings to enhance your understanding and decision-making process.
What are Tapered Roller Bearings?
Tapered roller bearings are specialized bearings designed to accommodate both radial and axial loads. They feature tapered inner and outer ring raceways with tapered rollers arranged between them. This design enables the bearings to handle heavy loads and withstand axial forces in one direction.
How do Tapered Roller Bearings Work?
Tapered roller bearings operate through the rolling of tapered rollers between the inner and outer rings. The angle of the rollers and the raceways ensures effective load distribution, reducing friction and heat generation. This mechanism enhances efficiency and prolongs bearing life.
What are the Advantages of Tapered Roller Bearings?
Tapered roller bearings offer several advantages:
High Load Capacity: They can support high radial and axial loads.
Versatility: Suitable for various industrial applications, including automotive, aerospace, and heavy machinery.
Longevity: Designed for durability and extended service life with proper maintenance.
How to Select the Right Tapered Roller Bearing?
Choosing the correct tapered roller bearing involves considering factors such as:
Load Requirements: Determine the radial and axial loads the bearing needs to support.
Speed Ratings: Ensure the bearing can operate at the required speeds without compromising performance.
Application Specifics: Consider environmental conditions, temperature ranges, and lubrication requirements.
What Maintenance is Required for Tapered Roller Bearings?
Tapered roller bearings require regular maintenance to ensure optimal performance:
Lubrication: Use suitable lubricants and follow recommended schedules to prevent wear and reduce friction.
Inspections: Periodically inspect bearings for signs of wear, misalignment, or contamination.
Replacement: Replace bearings as recommended by the manufacturer to avoid unexpected failures.
How to Extend the Life of Tapered Roller Bearings?
To prolong the life of tapered roller bearings, follow these best practices:
Proper Installation: Ensure bearings are installed correctly to prevent misalignment and uneven loading.
Monitoring: Monitor bearing conditions regularly through vibration analysis and temperature checks.
Training: Provide training to personnel on proper handling, installation, and maintenance practices.
Where Can I Find Reliable Tapered Roller Bearings?
Reliable tapered roller bearings are available from reputable manufacturers and distributors. Consider brands known for quality, reliability, and customer support. Evaluate suppliers based on their industry reputation and adherence to international standards.
Miller, T., & Smith, J. (2022). Application of tapered roller bearings in aerospace: Challenges and advancements.