Historical Origins of Roller Bearings
Roller bearings, though now integral to modern machinery, have ancient origins that trace back thousands of years. The earliest known forms of roller bearings can be found in ancient civilizations, where they were ingeniously crafted to solve mechanical challenges of the time. These ancient designs, while rudimentary compared to modern standards, laid the foundation for the development of the roller bearings we know today.
One of the earliest known uses of roller bearings can be seen in ancient Egyptian civilization, where cylindrical objects were placed beneath heavy stones to facilitate their movement. These cylindrical objects acted as rudimentary rollers, reducing friction and enabling the transportation of massive stone blocks for construction purposes. This early application demonstrates the basic principle of using rolling elements to support heavy loads and reduce friction, a concept that remains fundamental to roller bearing design.
Similarly, ancient Greek and Roman engineers utilized rudimentary roller bearings in various applications, including the construction of chariots and siege engines. Wooden axles fitted with cylindrical rollers or balls provided smoother rotation and reduced friction, enhancing the efficiency and performance of these mechanical devices. These early roller bearing designs showcased the ingenuity of ancient engineers in harnessing the power of rolling elements to improve mechanical systems.
As civilization progressed, so did the evolution of roller bearings. During the Middle Ages, advancements in metallurgy enabled the production of more durable and efficient roller bearing components. Iron and bronze were forged into smoother, more precise shapes, allowing for smoother rotation and increased load-bearing capacity. The emergence of water and wind-powered mills further drove the demand for reliable roller bearings, spurring innovation and refinement in their design and construction.
By the Industrial Revolution, roller bearings had become indispensable components in machinery and equipment across various industries. Innovations in manufacturing processes, such as precision machining and assembly techniques, led to the mass production of standardized roller bearings. This revolutionized industries such as transportation, manufacturing, and agriculture, enabling unprecedented levels of productivity and efficiency.
In conclusion, the historical origins of roller bearings date back to ancient civilizations, where they were used to solve practical engineering challenges. From rudimentary designs crafted from wood and stone to modern precision-engineered marvels, roller bearings have undergone a remarkable evolution. Today, roller bearings continue to play a crucial role in modern engineering, driving innovation and progress across diverse industries.
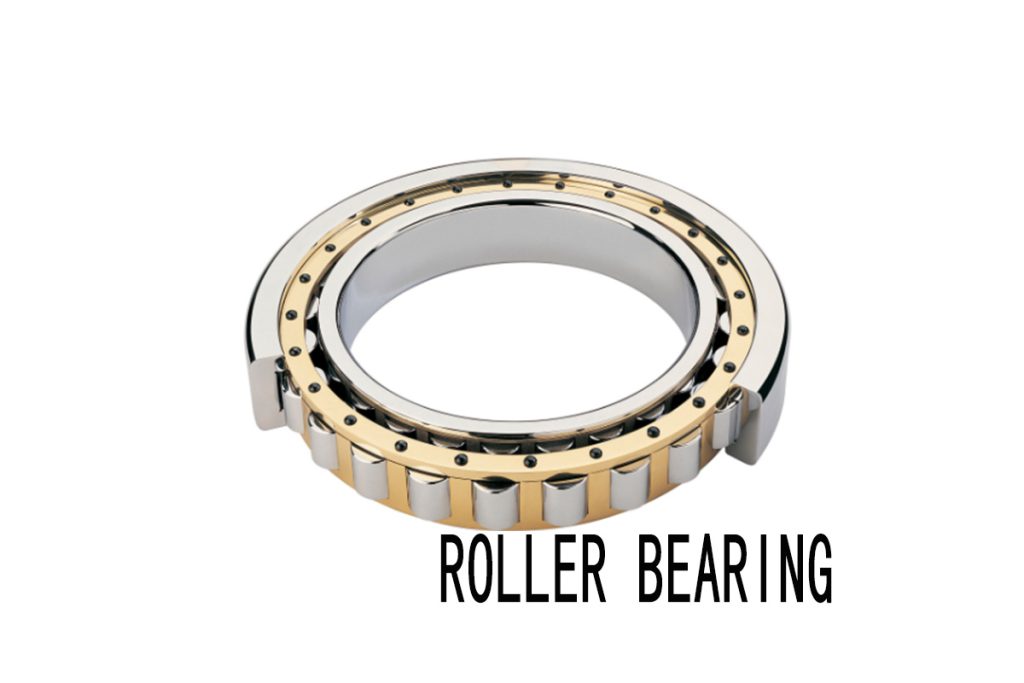
Development through the Industrial Revolution
The Industrial Revolution marked a pivotal period in the evolution of roller bearings, driving significant advancements in their design, production, and application. As industries expanded and machinery became more complex, the demand for reliable and efficient roller bearings grew exponentially. During this transformative era, roller bearings underwent crucial developments that laid the foundation for their widespread use in modern engineering.
One of the most notable advancements during the Industrial Revolution was the transition from wooden and stone bearings to metal roller bearings. Innovations in metallurgy enabled the production of stronger and more durable bearing components, capable of withstanding higher loads and operating speeds. Iron and steel emerged as preferred materials for roller bearing construction, offering superior strength and wear resistance compared to traditional materials.
The invention of precision machining techniques revolutionized roller bearing production, allowing for the mass production of standardized bearings with consistent dimensions and performance. This shift towards precision manufacturing facilitated interchangeability between bearings, simplifying maintenance and repair procedures for industrial machinery. Engineers could now select bearings based on standardized specifications, rather than relying on custom-made components.
During this period, numerous patents were granted for innovative roller bearing designs and configurations. One such patent was awarded to Jules Suriray in 1794 for his invention of the tapered roller bearing, which featured conical rollers and raceways designed to handle both radial and axial loads. This groundbreaking design paved the way for the development of modern tapered roller bearings, widely used in automotive transmissions and industrial machinery.
The Industrial Revolution also witnessed advancements in lubrication techniques, essential for reducing friction and prolonging bearing life. The introduction of grease lubrication systems enabled more efficient and reliable lubrication of roller bearings, improving their performance and longevity in demanding operating environments. Additionally, advancements in sealing technology helped protect bearings from contamination and moisture ingress, further enhancing their reliability and durability.
In conclusion, the Industrial Revolution was a transformative period that propelled the evolution of roller bearings from ancient designs to modern engineering marvels. Through significant advancements in metallurgy, manufacturing processes, and lubrication technology, roller bearings became indispensable components in industrial machinery, driving progress and innovation across diverse industries. The innovations of this era continue to shape the design and functionality of roller bearings in the present day, highlighting their enduring significance in modern engineering.
Modern Engineering and Material Science
In the realm of roller bearing production, modern engineering and material science play integral roles in shaping the evolution of these essential components. Advancements in materials and manufacturing processes have led to the development of roller bearings with enhanced durability, load capacity, and performance characteristics.
Materials Used in Roller Bearing Production | |
High-Strength Alloys | Modern roller bearings are constructed using a variety of materials carefully selected to meet specific application requirements. High-strength alloys, such as chrome steel and stainless steel, are commonly utilized for bearing components like inner and outer rings, rollers, and cages. These alloys offer excellent mechanical properties, including high tensile strength, fatigue resistance, and corrosion resistance, making them ideal for demanding operating conditions. |
Ceramic Materials | In addition to metallic alloys, ceramic materials have gained prominence in roller bearing applications, particularly in high-speed and high-temperature environments. Silicon nitride (Si3N4) and zirconia (ZrO2) ceramics exhibit superior hardness, thermal stability, and low coefficient of friction compared to traditional steel alloys. As a result, ceramic roller bearings offer reduced wear, increased service life, and enhanced performance in challenging operating conditions. |
Role of Material Science in Roller Bearing Enhancement
Material science plays a crucial role in advancing the performance and functionality of roller bearings. Through rigorous research and development efforts, engineers strive to identify novel materials and improve existing alloys to address evolving industry demands. The optimization of material composition, microstructure, and processing techniques enables the production of roller bearings with superior mechanical properties and performance characteristics.
Material science also contributes to the development of specialized coatings and surface treatments designed to further enhance bearing performance. Thin film coatings, such as diamond-like carbon (DLC) and titanium nitride (TiN), provide lubricity, wear resistance, and corrosion protection, extending the service life of roller bearings in harsh operating environments.
Modern Manufacturing Processes
Modern manufacturing processes play a pivotal role in ensuring the quality and reliability of roller bearings. Precision machining techniques, such as CNC (Computer Numerical Control) grinding and turning, enable the production of bearings with tight tolerances and smooth surface finishes. These processes ensure precise dimensional accuracy and proper fitment, essential for optimizing bearing performance and longevity.
Heat treatment processes, including quenching and tempering, are employed to enhance the mechanical properties of bearing components. Through controlled heating and cooling cycles, roller bearing materials undergo transformation, resulting in increased hardness, toughness, and fatigue resistance. Heat treatment also relieves internal stresses and improves dimensional stability, ensuring consistent performance under varying load conditions.
In conclusion, modern engineering and material science have propelled the evolution of roller bearings from ancient designs to modern engineering marvels. By leveraging advanced materials and manufacturing processes, engineers continue to push the boundaries of roller bearing performance, reliability, and efficiency, driving innovation across diverse industries and applications.
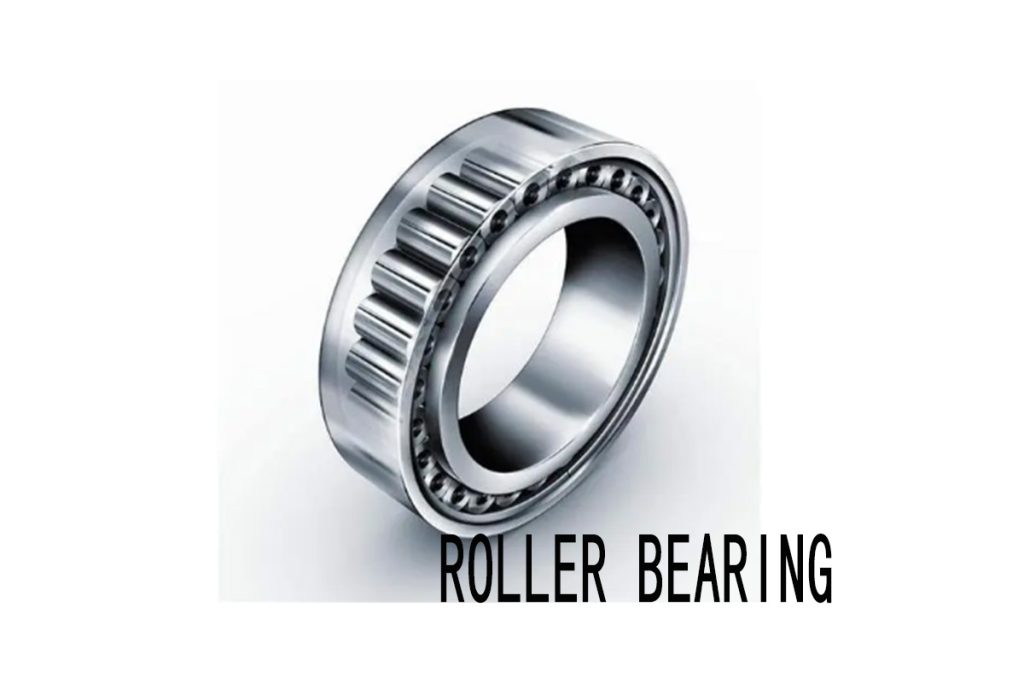
Applications in Contemporary Industries
Roller bearings have evolved from their ancient designs to become indispensable components in a wide array of contemporary industries. Their versatility, efficiency, and durability make them essential for various applications, ranging from automotive to renewable energy sectors.
Automotive Industry
In the automotive sector, roller bearings play a crucial role in numerous vehicle components, including engines, transmissions, wheels, and steering systems. They facilitate smooth rotation and movement, reducing friction and wear, thereby enhancing overall vehicle performance and fuel efficiency. Whether in wheel hubs, crankshafts, or camshafts, roller bearings contribute to the reliable operation of vehicles under diverse driving conditions.
Aerospace and Aviation
Roller bearings are vital in the aerospace and aviation industries, where precision, reliability, and weight reduction are paramount. These bearings support critical aircraft components such as landing gear, flight control systems, engines, and auxiliary power units. By minimizing friction and ensuring precise motion control, roller bearings contribute to the safety, efficiency, and longevity of aircraft, enabling smooth takeoffs, landings, and flight operations.
Manufacturing and Machinery
In manufacturing and machinery applications, roller bearings are ubiquitous, supporting rotating shafts and components in various industrial equipment. From conveyor systems and machine tools to pumps and compressors, roller bearings facilitate smooth motion, reduce energy consumption, and minimize maintenance requirements. Their ability to withstand heavy loads, high speeds, and harsh operating conditions makes them indispensable for optimizing productivity and uptime in manufacturing facilities worldwide.
Renewable Energy Sector
Roller bearings play a vital role in renewable energy generation systems, such as wind turbines and solar trackers. In wind turbines, large-diameter bearings support the rotor shaft, enabling efficient energy conversion from wind power to electrical power. Similarly, in solar trackers, roller bearings facilitate the precise alignment of solar panels to maximize energy capture from the sun. By providing reliable operation and minimal maintenance requirements, roller bearings contribute to the sustainability and viability of renewable energy technologies.
Specific Roller Bearing Types for Varied Applications
The diverse applications of roller bearings necessitate the development of specialized bearing types tailored for specific operating conditions. For example, tapered roller bearings are commonly used in automotive wheel hubs and gearbox applications due to their ability to support axial and radial loads simultaneously. Cylindrical roller bearings are preferred for high-speed, precision machinery applications, offering low friction and high rigidity.
In conclusion, roller bearings have undergone a remarkable evolution from ancient designs to become indispensable components in modern engineering marvels. Their widespread applications across diverse industries underscore their significance in enhancing efficiency, reducing friction, and extending the lifespan of machinery in contemporary society.
Innovations and Future Trends
The evolution of roller bearings has been marked by continuous innovation, driving advancements in technology and engineering. As we look towards the future, several cutting-edge innovations are shaping the next generation of roller bearings, revolutionizing their applications and performance capabilities.
Innovations in Roller Bearing Technology | |
Smart Bearings with Embedded Sensors | One of the most significant innovations in roller bearing technology is the development of smart bearings equipped with embedded sensors. These sensors monitor crucial parameters such as temperature, vibration, and lubrication conditions in real-time, providing valuable insights into bearing health and performance. By detecting early signs of wear or impending failure, smart bearings enable proactive maintenance, minimizing downtime and preventing costly equipment damage. Furthermore, data collected from these sensors can be analyzed to optimize bearing design, lubrication strategies, and operational efficiency. |
Advanced Lubrication Systems | Another area of innovation in roller bearing technology is the advancement of lubrication systems. Traditional lubricants have been replaced by high-performance greases and oils tailored for specific operating conditions, such as high temperatures, extreme speeds, or corrosive environments. Additionally, innovative lubrication techniques, such as oil mist and air-oil systems, ensure optimal lubrication distribution and longevity, enhancing bearing performance and reliability. These advanced lubrication systems contribute to extended bearing service life, reduced maintenance requirements, and improved energy efficiency in various industrial applications. |
Trends in Roller Bearing Design | Looking ahead, several trends are shaping the future of roller bearing design. Miniaturization is driving the development of compact and lightweight bearings for use in portable devices, robotics, and medical equipment. Enhanced sustainability is driving the adoption of eco-friendly materials and manufacturing processes, reducing environmental impact throughout the bearing lifecycle. Increased precision in bearing design, enabled by advanced manufacturing technologies such as 3D printing and nanotechnology, is leading to tighter tolerances, smoother operation, and higher performance capabilities. |
Future Outlook | The future of roller bearing technology holds immense promise, with continued innovation driving advancements in performance, reliability, and functionality. Smart bearings will become increasingly intelligent, leveraging artificial intelligence and machine learning algorithms to predict maintenance needs and optimize performance in real-time. Advanced materials, such as ceramic and composite materials, will further enhance bearing durability, corrosion resistance, and load-carrying capacity. Moreover, as industries continue to evolve, roller bearings will play a pivotal role in enabling new technologies such as electric vehicles, renewable energy systems, and automation solutions. |
In conclusion, the roller bearing industry is experiencing a period of unprecedented innovation and evolution, from ancient designs to modern engineering marvels. With ongoing advancements in technology and engineering, roller bearings are poised to continue driving progress across a wide range of industries, shaping the future of manufacturing, transportation, and beyond.
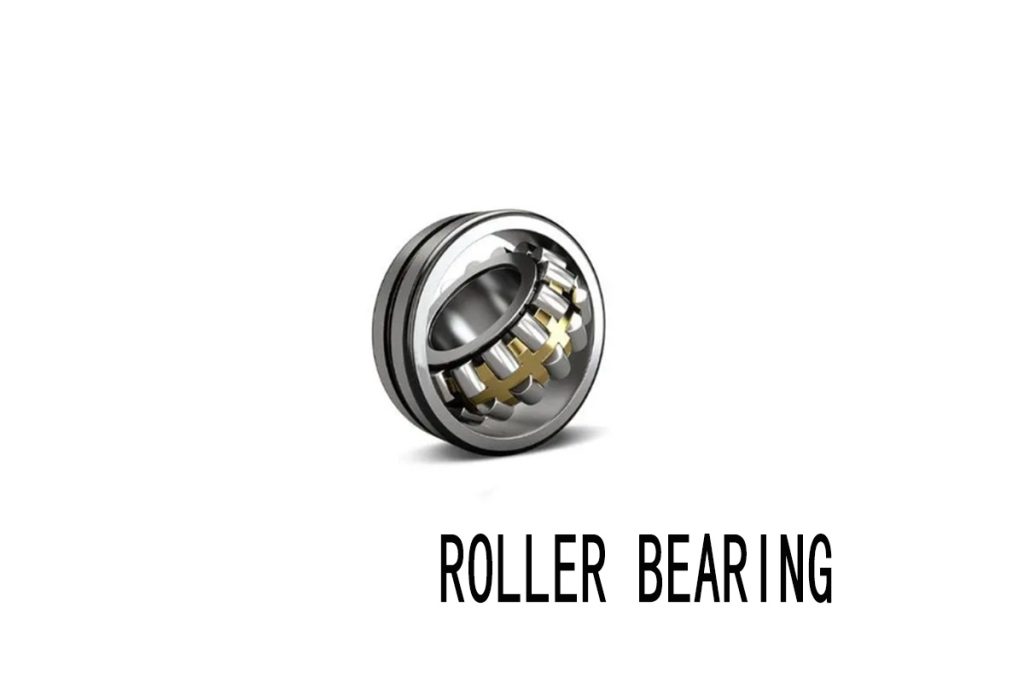
Conclusion
The journey of roller bearings, from their humble beginnings to their current state of engineering marvels, is a testament to human ingenuity and innovation. Roller bearings have traversed through history, evolving with the changing needs of society and technological advancements.
Reflecting on the historical origins, roller bearings have been an integral part of various civilizations, dating back to ancient times. Early designs, although rudimentary, laid the groundwork for the sophisticated bearings we have today. Through the Industrial Revolution, significant advancements propelled roller bearings into mainstream use, revolutionizing industries and shaping modern engineering practices.
In contemporary times, roller bearings find applications across diverse industries, including automotive, aerospace, manufacturing, and renewable energy. Their versatility and reliability make them indispensable components in machinery and equipment, contributing to efficiency, reducing friction, and extending operational lifespan.
Looking ahead, the future of roller bearings is poised for further innovation and advancements. Emerging trends such as smart bearings with embedded sensors and advanced lubrication systems promise to enhance performance and reliability. Miniaturization, enhanced sustainability, and increased precision are driving forces shaping the next generation of roller bearing technology.
As we conclude this exploration of roller bearing evolution, it’s imperative for engineers and industry professionals to remain vigilant about staying informed about the latest trends and innovations. By embracing new technologies and pushing the boundaries of engineering, we can continue to unlock the full potential of roller bearings and drive forward progress in modern engineering.
In essence, roller bearings have come a long way, evolving from ancient designs to modern engineering marvels, and their journey of innovation continues to shape the future of technology and industry.