Introduction
Flange bearings, essential components in machinery, play a pivotal role in supporting rotating shafts while facilitating smooth motion and reducing friction.
Overview of Flange Bearing and Its Significance in Machinery
A flange bearing, also known as a flanged bearing or flanged bushing, is a type of plain bearing with a flange that extends radially outward to provide additional support and stability. This design allows for easier mounting and positioning within machinery, ensuring precise alignment of rotating shafts. The flange serves as a mechanical stop, preventing lateral movement and maintaining the bearing’s position under axial loads.
Flange bearings are commonly used in industrial applications such as automotive, aerospace, construction equipment, and manufacturing machinery. They are preferred for their durability, high load-bearing capacity, and ability to operate effectively in various environmental conditions.
Brief History and Origin of Flange Bearing
The concept of flange bearings traces back to the early advancements in mechanical engineering during the Industrial Revolution. As industries expanded and diversified, there arose a need for bearings that could withstand heavier loads and higher speeds. The integration of flanges into bearing designs emerged as a solution to improve stability and performance in rotating machinery.
In the late 19th century, with the development of precision machining techniques and metallurgical advancements, flange bearings evolved into more specialized components capable of meeting stringent industrial requirements. This historical evolution laid the foundation for modern-day applications where flange bearings are indispensable.
Importance of Technological Advancements in Enhancing Flange Bearing Performance
Technological innovations have been instrumental in pushing the boundaries of flange bearing performance and expanding their applications across diverse fields. Key advancements include:
Material Science: The introduction of advanced materials such as self-lubricating polymers, composite materials, and high-performance alloys has significantly enhanced the load-bearing capacity, wear resistance, and operational lifespan of flange bearings. These materials offer superior frictional properties and reduce maintenance requirements.
Design Optimization: Computational modeling and simulation techniques have revolutionized the design process, allowing engineers to optimize the geometry and structural integrity of flange bearings. This optimization minimizes stress concentrations, improves load distribution, and enhances overall mechanical efficiency.
Lubrication Technology: Innovations in lubrication systems, including sealed bearings and advanced lubricants, have mitigated frictional losses and reduced the risk of premature wear. Self-lubricating bearings, in particular, offer maintenance-free operation and improved reliability in harsh operating environments.
Smart Bearing Solutions: The integration of sensor technologies and IoT-enabled monitoring systems has enabled real-time condition monitoring of flange bearings. These smart solutions provide early fault detection, predictive maintenance insights, and operational analytics, thereby optimizing asset management and reducing downtime.
In conclusion, the evolution of flange bearings from simple mechanical components to sophisticated, high-performance solutions underscores their critical role in modern machinery. By leveraging technological advancements, engineers continue to innovate and push the boundaries of what is achievable, driving efficiency, reliability, and sustainability in industrial applications.

Historical Development
The evolution of flange bearings spans centuries, marked by significant advancements in materials, design, and engineering. explores the early origins, key figures, and pivotal milestones that have shaped the development of flange bearings into indispensable components in modern machinery.
Early Designs and Materials Used in Flange Bearings
The concept of flange bearings can be traced back to ancient civilizations where rudimentary forms of bearings were employed to reduce friction in moving parts. Early designs utilized simple materials such as wood, stone, and bronze, which were shaped into cylindrical or spherical forms with protruding flanges. These primitive bearings were primarily used in agricultural tools, water wheels, and early mechanical devices, providing essential support and reducing wear between rotating components.
During the Industrial Revolution, advancements in metallurgy and machining techniques revolutionized bearing design. Steel became the material of choice due to its strength, durability, and ability to withstand heavy loads and high speeds. Flange bearings evolved to incorporate precision machining, enabling tighter tolerances and improved alignment, thereby enhancing performance in industrial applications.
Key Inventors and Engineers Who Contributed to the Development of Flange Bearings
The development of flange bearings owes much to pioneering engineers and inventors who refined bearing designs and manufacturing processes over time. One notable figure is Leonardo da Vinci, who conceptualized and sketched various types of bearings in the 15th century, laying the groundwork for later innovations. In the 19th century, engineers such as John Harrison and Henry Timken made significant contributions to bearing technology by introducing precision grinding techniques and tapered roller bearings, respectively, which influenced the evolution of flange bearings.
In the early 20th century, SKF (Svenska Kullagerfabriken AB) emerged as a leader in bearing innovation, introducing advancements in lubrication systems and bearing materials that improved reliability and longevity. These developments set the stage for the widespread adoption of flange bearings across diverse industrial sectors.
Milestones in the Evolution of Flange Bearing Technology
The evolution of flange bearing technology has been marked by several key milestones that have expanded their capabilities and applications:
Introduction of Self-Lubricating Bearings | In the mid-20th century, the development of self-lubricating bearings marked a significant advancement in bearing technology. These bearings integrated solid lubricants or lubricant-filled pores within the bearing material, reducing maintenance requirements and extending operational lifespan. |
Advent of Composite Materials | With the advancement of composite materials in the latter half of the 20th century, flange bearings began incorporating materials such as nylon, PTFE (Polytetrafluoroethylene), and fiberglass-reinforced plastics. These materials offered enhanced wear resistance, reduced friction, and improved corrosion resistance, making them ideal for harsh operating environments. |
Precision Manufacturing Techniques | The adoption of computer numerical control (CNC) machining and advanced manufacturing processes in the late 20th century allowed for the production of flange bearings with higher precision and consistency. This facilitated tighter tolerances, smoother operation, and increased reliability in critical machinery applications. |
In conclusion, the historical development of flange bearings underscores their evolution from primitive mechanical devices to sophisticated components essential for modern machinery. By leveraging advancements in materials science, manufacturing technologies, and design innovation, engineers continue to push the boundaries of what is achievable, enhancing the performance, reliability, and versatility of flange bearings in diverse industrial applications.
The historical development of flange bearings is explored in detail, highlighting early designs, influential inventors and transformative milestones that shaped their evolution into an indispensable component in engineering and manufacturing.
Technological Innovations
The evolution of flange bearings has been profoundly influenced by advancements in materials, manufacturing techniques, and design innovations. explores the modern technologies that have revolutionized flange bearings, enhancing their performance, durability, and applicability across diverse industries.
Modern Materials and Manufacturing Techniques for Flange Bearings
The choice of materials plays a critical role in the performance and longevity of flange bearings. Traditional materials such as bronze and steel have been augmented by modern alloys, polymers, and composites that offer superior mechanical properties and resistance to wear and corrosion.
Polymer-based materials like PTFE (Polytetrafluoroethylene) and nylon are widely used for their self-lubricating properties, reducing the need for external lubrication and maintenance. These materials are ideal for applications where cleanliness and quiet operation are paramount, such as medical equipment and food processing machinery.
Composite materials, reinforced with fibers such as fiberglass or carbon, provide exceptional strength-to-weight ratios and enhanced resistance to harsh environments. These materials are favored in aerospace and automotive applications where lightweight bearings capable of withstanding high loads and temperatures are required.
Ceramic bearings have also gained prominence due to their high hardness, low friction, and resistance to corrosion. Silicon nitride and zirconia-based ceramics are utilized in high-speed and high-temperature environments, offering extended service life and reduced maintenance intervals.
Modern manufacturing techniques such as computer numerical control (CNC) machining, injection molding, and additive manufacturing (3D printing) have transformed the production of flange bearings. These technologies enable precise tolerances, complex geometries, and rapid prototyping, facilitating customization and optimizing performance characteristics tailored to specific applications.
Advanced Design Features for Improved Performance and Durability
Innovative bearing design features have significantly enhanced the functionality and reliability of flange bearings:
Sealing and lubrication systems have evolved to minimize frictional losses and prevent contamination ingress, thereby extending bearing life and reducing maintenance costs. Sealed bearings equipped with advanced lubricants or grease retainers ensure consistent performance in challenging operating conditions.
Integrated sensors and condition monitoring systems enable real-time performance analysis, detecting abnormalities such as vibration, temperature fluctuations, and wear. This proactive approach to maintenance enhances equipment uptime and reliability, crucial for industries relying on continuous operation.
Precision engineering techniques optimize load distribution across bearing surfaces, reducing stress concentrations and improving overall efficiency. Finite element analysis (FEA) and computational fluid dynamics (CFD) simulations guide design refinements, ensuring optimal performance under variable operating conditions.
Impact of Automation and Precision Engineering on Flange Bearing Production
Automation has revolutionized flange bearing production, streamlining processes from material handling to final assembly. Robotic arms and automated machining centers ensure consistent quality and dimensional accuracy, minimizing human error and variability.
Precision engineering methodologies such as lean manufacturing principles and Six Sigma practices improve process efficiency and waste reduction. Continuous improvement initiatives foster innovation in production techniques and materials, driving advancements in flange bearing technology.
In conclusion, technological innovations continue to propel the evolution of flange bearings, expanding their capabilities and applications in various industries. By leveraging modern materials, advanced manufacturing techniques, and innovative design features, engineers enhance the performance, durability, and reliability of flange bearings, contributing to the efficiency and sustainability of industrial machinery.
This section has provided an in-depth exploration of the technological innovations that have reshaped flange bearings, laying the foundation for their revolutionary impact on modern industrial applications.
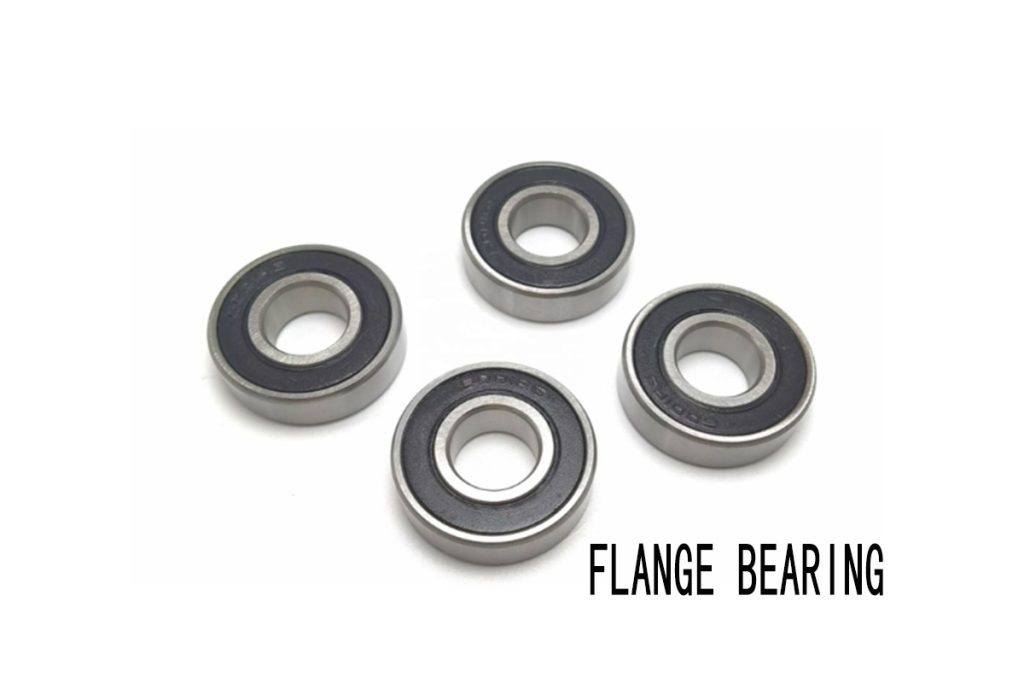
Applications and Uses
Flange bearings are integral components across a wide range of industries, providing essential support and facilitating smooth operation in diverse machinery and equipment. explores the extensive applications of flange bearings across various sectors, highlighting their specific uses and the benefits derived from advanced technological innovations.
Overview of Industries that Utilize Flange Bearings
Flange bearings find widespread use in industries where rotating machinery and equipment are essential for operations. Key sectors include:
Automotive Industry | Flange bearings are crucial in automotive applications, supporting shafts in engines, transmissions, steering systems, and wheel assemblies. They ensure precise alignment, reduce friction, and enhance vehicle performance and reliability. |
Aerospace and Defense | In aerospace applications, flange bearings are employed in aircraft engines, landing gear systems, control surfaces, and avionics. They withstand extreme temperatures, high speeds, and dynamic loads, ensuring safety and operational efficiency. |
Industrial Manufacturing | Flange bearings play a vital role in industrial machinery such as conveyor systems, pumps, turbines, and processing equipment. They facilitate smooth motion, reduce energy consumption, and minimize downtime in manufacturing operations. |
Construction and Heavy Equipment | Equipment used in construction and mining rely on flange bearings for their durability and load-bearing capacity. Applications include excavators, cranes, bulldozers, and drilling rigs, where bearings endure harsh environmental conditions and heavy-duty cycles. |
Medical and Pharmaceutical | Precision and reliability are critical in medical equipment where flange bearings are used in imaging devices, surgical tools, patient handling systems, and laboratory equipment. They ensure smooth operation and minimize contamination risks. |
Specific Examples of Flange Bearing Applications in Various Machinery and Equipment
Automotive Applications: In automotive steering systems, flange bearings support the steering shaft, ensuring responsive and accurate vehicle control. They withstand constant movement and vibrations while maintaining alignment and reducing wear.
Industrial Pumps: Flange bearings in industrial pumps facilitate the smooth rotation of shafts, enhancing efficiency and reliability in fluid handling processes. They are designed to withstand high pressures and varying operating conditions.
Aircraft Landing Gear: Flange bearings in aircraft landing gear systems support the weight of the aircraft during landing and taxiing. They provide stability, absorb shock loads, and ensure safe operation under rigorous aviation standards.
Food Processing Equipment: In food and beverage processing, flange bearings are used in conveyor systems, mixers, and packaging machinery. They comply with hygiene standards, resist corrosion from washdowns, and maintain operational cleanliness.
Benefits of Using Advanced Flange Bearings in Different Sectors
Advanced flange bearings offer several advantages that enhance performance and reliability in industrial applications:
Enhanced Durability: Utilization of advanced materials such as stainless steel, ceramics, and specialized polymers improves bearing longevity and reduces maintenance requirements.
Improved Efficiency: Precision manufacturing techniques ensure tight tolerances and optimal load distribution, minimizing frictional losses and energy consumption.
Reliability in Harsh Environments: Resilience to extreme temperatures, chemicals, and abrasive conditions ensures consistent performance in challenging operational settings.
Cost-effectiveness: Reduced downtime and maintenance costs due to extended bearing life and enhanced operational reliability contribute to overall cost savings.
In conclusion, the versatility and reliability of flange bearings make them indispensable components across various industries. Technological innovations continue to advance their capabilities, enabling broader applications and ensuring optimal performance in critical machinery and equipment.
An overview of the wide range of applications, specific examples and benefits of advanced flange bearings, highlighting their critical role in modern industrial processes
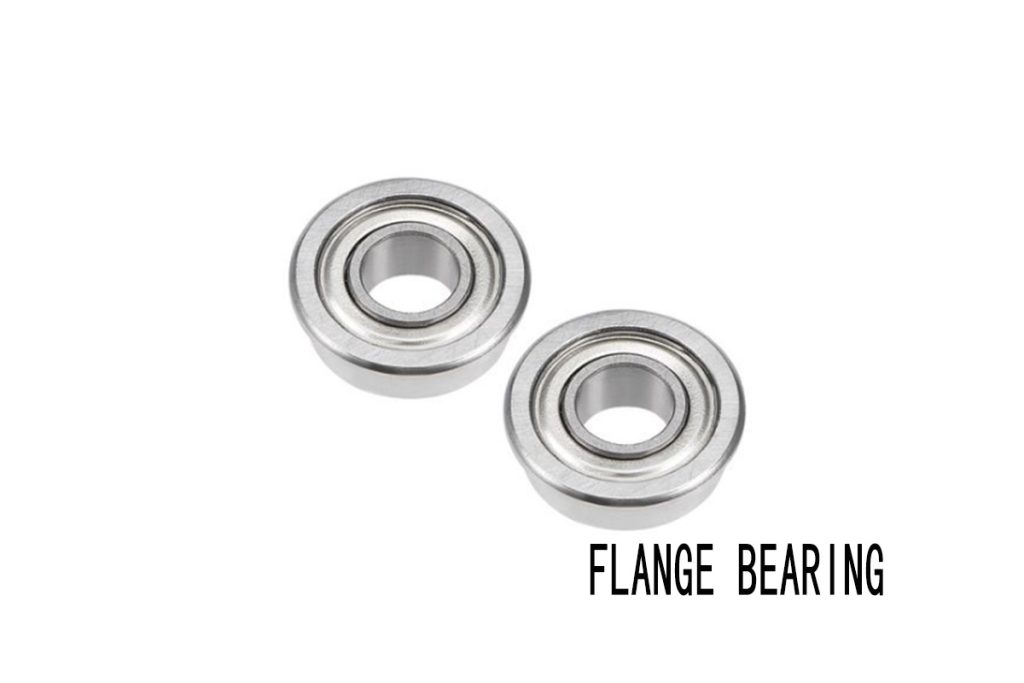
Conclusion
In this comprehensive exploration of flange bearings, we have delved into their historical development, technological innovations, diverse applications across industries, and the profound impact of these advancements on modern machinery. Let’s recap the key points discussed and reflect on the significance of technological advances in flange bearing applications.
Recap of Key Points Discussed in the Article
we have highlighted the evolution of flange bearings from early designs using basic materials to the adoption of modern alloys, polymers, and composites. The contributions of key inventors and engineers have been acknowledged, underscoring their role in refining bearing designs and manufacturing processes. Milestones such as the introduction of self-lubricating bearings and advancements in precision engineering techniques have significantly enhanced
flange bearing performance and durability.
We explored the extensive applications of flange bearings across various industries, including automotive, aerospace, industrial manufacturing, construction, and medical sectors. Specific examples illustrated how flange bearings support critical functions in machinery such as automotive steering systems, industrial pumps, aircraft landing gear, and food processing equipment. The benefits of advanced flange bearings were emphasized, including enhanced durability, improved efficiency, reliability in harsh environments, and cost-effectiveness.
Final Thoughts on the Significance of Technological Advances in Flange Bearing Applications
The revolution in flange bearing technology driven by technological advances has reshaped industrial practices and standards. Advanced materials and manufacturing techniques have not only improved bearing performance but also enabled new applications in demanding environments where reliability and efficiency are paramount. The integration of smart technologies for condition monitoring and predictive maintenance has further enhanced operational reliability, minimizing downtime and optimizing asset management.
Moreover, the evolution of flange bearings reflects broader trends in engineering innovation, where continuous research and development pave the way for sustainable solutions and enhanced productivity. As industries evolve, so do the requirements for bearings that can withstand higher loads, speeds, and environmental conditions while maintaining optimal performance.
Encouragement for Ongoing Innovation and Research in Flange Bearing Technology
Looking ahead, the future of flange bearings lies in ongoing innovation and research aimed at addressing emerging challenges and opportunities. Advancements in materials science, additive manufacturing, and digitalization offer promising avenues for further improving bearing efficiency, lifespan, and sustainability. Collaborations between industry stakeholders and academic institutions will play a crucial role in pushing the boundaries of flange bearing technology and exploring new frontiers in engineering applications.
In conclusion, the flange bearing revolution driven by technological advances underscores its indispensable role in modern industrial machinery. By embracing innovation and embracing new possibilities, we can continue to elevate flange bearing performance, reliability, and versatility, ensuring they remain vital components in the machinery of tomorrow.
This article has provided a comprehensive overview of flange bearings, emphasizing their evolution, applications, and the transformative impact of technological advancements. Let us continue to innovate and shape the future of flange bearing technology for enhanced industrial capabilities and sustainable development.